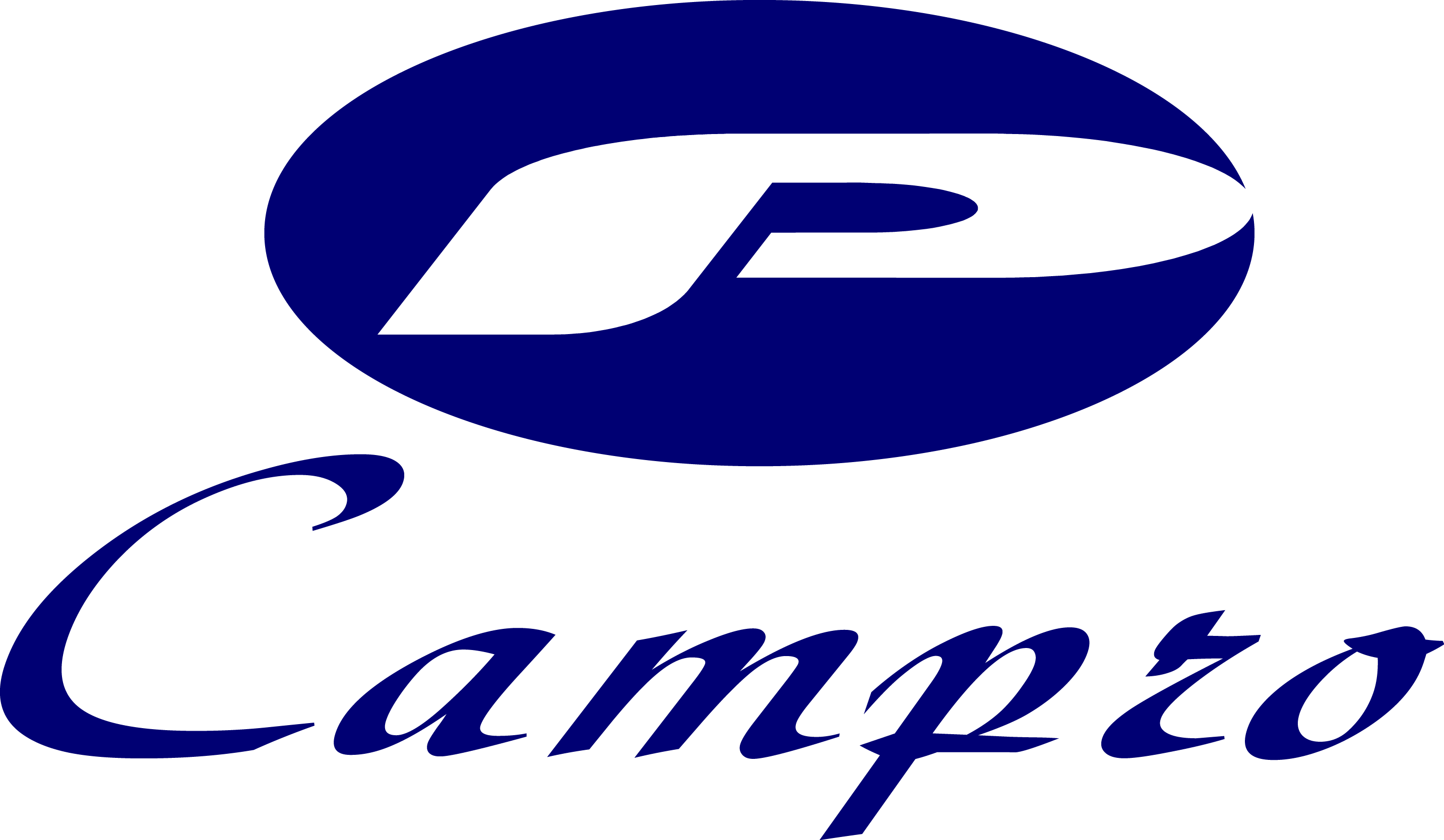
CAMPRO PRECISION MACHINERY CO., LTD.
Campro

News
more
Introduction In today's rapidly evolving
manufacturing industry, vertical machining centers play an indispensable role.
These efficient machines not only accelerate production processes but also
enhance machining quality, becoming the cornerstone of various industries such
as automotive, aerospace, and electronics manufacturing. As market demands
continue to evolve, the technology of these machining centers advances to meet
more precise machining requirements and higher production efficiencies. This
article aims to explore how to choose a vertical machining center that meets
future market demands, analyzing market trends and technological development
directions.
Market Trend Analysis Changes in market
demand are crucial factors influencing the choice of vertical machining
centers. As consumer expectations for product quality and production efficiency
rise, manufacturers must assess which models can most effectively meet these
needs. Modern market trends indicate a continuous rise in demand for
high-performance and multifunctional vertical machining centers. These machines
can quickly adjust and maintain high production efficiency, making them
particularly suitable for small-batch, diversified production models.
Technological innovation is also a key driver of changes in
market demand. For example, advancements in CNC technology have improved
machining precision while simplifying the operation process, making vertical
machining centers more user-friendly. Additionally, integrating advanced
measurement techniques and real-time monitoring systems allows the machine to
automatically adjust parameters during the machining process, further enhancing
product quality and efficiency.
Campro Machinery Product Line
Since 2016, Campro Machinery has actively invested in the
field of intelligent machinery, starting with factory visualization management
and gradually expanding to provide comprehensive smart factory solutions. We
have become pioneers in the digital era by integrating advanced technologies,
machine networking, and intelligent machinery, enabling machines to
automatically adjust parameters during the machining process, thereby enhancing
product quality and production efficiency.
Campro Machinery is a professional CNC machine tool
manufacturer, producing a variety of machining centers and lathes. Our vertical
machining centers are divided into four categories, each with different models:
·
CPV-B Series #40 Box Ways Vertical
Machining Center: This comprehensive machining
center pursues stability and versatility. It enhances the efficiency of
machines in the factory, featuring a three-axis box ways design for superior
stability. The entire structure is made of high-grade cast iron and undergoes
heat treatment to eliminate internal stress, ensuring optimal rigidity and
precision durability. The series offers X-axis travel ranges from 850 mm to
1600 mm for customer selection.
·
CPV-B Series #50 Heavy Duty (Box
Ways) Vertical Machining Center: In addition
to stability and versatility, the #50 spindle is more suitable for heavy
cutting. The series offers X-axis travel ranges from 1100 mm to 2200 mm for
selection.
·
CNV Series High Efficiency Vertical
Machining Center: Focused on economy and
efficiency, this is the best choice for a wide range of small to medium-sized
parts manufacturers and users pursuing high efficiency. The series offers
X-axis travel ranges from 550 mm to 1300 mm for selection.
·
NV Series High Performance Vertical
Machining Center: Compared to other linear
guideway vertical machining centers of the same size on the market, the NV
series offers a larger Y-axis travelling range. Its unique loop design and
spindle thermal symmetry design effectively reduce thermal deformation,
improving accuracy and stability. Meeting the demands of many metalworking
users, this machine combines high mobility, high rigidity, and high stability.
It can also add a 5-axis table to the standard worktable configuration,
increasing the feasibility of different machining operations.
Our complete product line meets various functional needs,
providing customers with a diverse range of options, from high precision to
high efficiency, from basic to advanced models, fully covering all application
requirements.
Considerations for Choosing a Vertical Machining Center
When selecting a vertical machining center, it is important
to consider various factors to ensure that the chosen equipment meets current
and future production needs.
Machining Requirements and Application Scenarios Different industries and products have varying requirements for
machining precision, speed, and flexibility. Companies should evaluate the
machine’s performance and suitability based on their specific machining needs.
For instance, precision machining requires equipment with high accuracy and
stability, while mass production demands efficient and reliable machines.
Technical Parameters and Performance
Technical parameters are one of the core considerations when choosing a
vertical machining center. These include spindle speed, travel range, rigidity,
stability, and control systems. These parameters directly affect the machine’s
machining capabilities and applicability.
Intelligent and Automated Functions The
demand for intelligence and automation in modern manufacturing is increasing.
Machines equipped with AI integration, automation technologies, and real-time
monitoring can improve production efficiency, reduce labor costs, and ensure
product quality.
Brand Reputation and After-Sales Service
Choosing a brand with a good reputation ensures the quality and performance of
the machine. Additionally, comprehensive after-sales service provides timely
technical support and maintenance, ensuring the normal operation and longevity
of the machine.
Cost-Effectiveness Analysis Companies
should conduct a cost-effectiveness analysis based on their budget. It is
essential to choose a vertical machining center that offers the best value for
money while meeting machining needs and technical requirements to achieve
optimal investment returns.
Future Technological Developments In
terms of technological advancements in vertical machining centers, the
integration of artificial intelligence (AI) is significantly enhancing the
accuracy of machining decisions and optimizing production processes. AI can
automatically adjust machine settings to accommodate changing machining
demands, thereby increasing production efficiency and reducing human
intervention.
Additionally, automation technology enables vertical
machining centers to perform unattended production, which not only lowers labor
costs but also improves the stability of production quality. These technologies
enable machines to flexibly handle small-batch and diversified production
needs, aligning with modern manufacturing's dual requirements for high
efficiency and flexibility.
Conclusion
When choosing a vertical machining center, it is crucial to
consider how the machine can adapt to rapidly changing market demands and
technological trends. Case studies have shown that selecting a vertical
machining center equipped with advanced technology and flexibility is a wise
investment for businesses. This not only ensures product quality and production
efficiency but also prepares companies for future market challenges.
Based on the analysis presented in this article, future
vertical machining centers will need to integrate AI and automation
technologies more extensively to enhance operational efficiency and precision.
Moreover, to meet diverse production needs, the design of these machines should
focus more on modularity and scalability.
In summary, when selecting a vertical machining center, it
is important to consider not only its current technical specifications and
performance but also its future adaptability and development potential. Such
forward-thinking will enable businesses to maintain a competitive edge in
future market competition and achieve sustained business success.
Summary
Choosing a suitable vertical machining center requires
considering multiple factors, including machining needs and application
scenarios, technical parameters and performance, intelligent and automated
functions, brand reputation and after-sales service, and cost-benefit analysis.
Businesses should comprehensively evaluate these factors based on their needs
and market trends to ensure that the selected equipment can perform optimally
in both current and future production environments.
By selecting a vertical machining center with advanced
technology and flexibility, companies can enhance production efficiency and
product quality while also adapting to future market challenges and changes.
Campro Machinery is dedicated to providing comprehensive, advanced machining
solutions that help customers maintain a leading position in a competitive
market and achieve long-term business success.
07. 10. 2024
more
PrefaceAs the global manufacturing industry enters the era of intelligentization, the application of Artificial Intelligence (AI) technology in the field of Computer Numerical Control (CNC) machining has become a major driving force for industrial advancement. Since 2016, Campro Machinery has invested in the field of intelligent machinery, starting with factory visualization management. Now, the company can provide a range of smart manufacturing factory solutions, becoming a machining solution provider capable of keeping up with the digitalization trend. This article aims to delve into how AI plays a revolutionary role in CNC machining technology, not only improving production efficiency and enhancing quality but also leading the manufacturing industry towards greater automation and flexibility. Through specific technical analysis and future trend forecasts, we will demonstrate how AI technology creates significant value in CNC machining and predict how this technological collaboration will shape the future of the manufacturing industry. Through this in-depth analysis, readers will gain a comprehensive understanding of AI's application in modern manufacturing and witness a truly meaningful industrial revolution.I. Introduction: Introducing the Revolutionary Role of AI in CNC MachiningOver the past few decades, Computer Numerical Control (CNC) technology has dramatically transformed the manufacturing industry. With continuous technological advancements, CNC machining equipment can now execute complex machining tasks with unprecedented precision and efficiency. However, as market demand increases and production scales expand, traditional CNC technology faces new challenges: how to further improve production efficiency, reduce costs, and achieve higher levels of automation and flexibility. In this context, the introduction of Artificial Intelligence (AI) technology is gradually sparking a revolution in the field of CNC machining.The core capability of AI lies in its ability to process and analyze vast amounts of data, making it a crucial player in the automation and optimization of manufacturing processes. In CNC machining, AI can be used to analyze machine operation data and adjust machining parameters in real-time to accommodate different machining conditions or material properties. This intelligent adaptability not only enhances machine operational efficiency but also significantly improves machining quality and consistency.More importantly, AI enables predictive maintenance and fault diagnosis for CNC machines. By continuously monitoring the machine's operational status and performance, AI systems can identify potential machine faults and maintenance needs, allowing for proactive intervention before issues arise. This not only extends the machine's lifespan but also significantly reduces maintenance costs and unplanned downtime.Furthermore, AI applications are driving CNC technology toward higher levels of automation. For instance, through machine learning algorithms, CNC machines can learn and optimize their machining strategies based on past machining experiences. This learning capability not only boosts machining efficiency but also enables machines to handle a wider variety of machining tasks, better adapting to changing production demands.In summary, the application of AI in CNC machining is initiating a revolution in the manufacturing industry. By integrating AI technology with CNC machines, manufacturing enterprises can enhance production efficiency and product quality while achieving greater operational flexibility and cost-effectiveness. Looking ahead, as AI technology continues to develop and improve, its impact on the CNC machining field will become even more profound, bringing more innovation and transformation to the global manufacturing industry.II. The Core Role and Implementation of AI TechnologyThe application of Artificial Intelligence (AI) in the field of CNC machining is not just a technological innovation but an industrial transformation. The core role of AI technology lies in its ability to significantly enhance machining efficiency, precision, and adaptability, all achieved through intelligent data analysis and machine learning.Firstly, AI can optimize the machining paths of CNC machines through data analysis. In traditional CNC machining, setting machining parameters often relies on the operator's experience and intuition. While this method is feasible, it may lack precision or efficiency when dealing with complex or unfamiliar machining tasks. AI technology, by analyzing past machining data, can accurately predict the optimal machining parameters, such as spindle speed, feed rate, and cutting depth, and automatically adjust these parameters to suit different material properties and machining requirements.Additionally, AI's machine learning capabilities enable CNC machines to continuously learn and improve from actual machining processes. By continuously collecting machining data, AI systems can identify any unexpected behaviors or factors that may lead to defects in the machining process and adjust machining strategies to prevent similar issues from recurring. This self-optimization capability not only improves machining consistency and quality but also reduces reliance on human intervention.AI technology also enables real-time monitoring and control of the machining process. Through various sensors installed on CNC machines, AI systems can monitor the machining status in real-time, such as tool wear, motor load, and machine vibration. This information is immediately analyzed, and AI can respond instantly to any detected abnormalities by adjusting machining parameters or pausing operations to prevent damage and ensure the quality of the final product.Through these advanced functionalities, AI not only elevates the technical level of CNC machining but also greatly enhances the intelligence and automation of production processes. As these technologies continue to develop and be applied, AI will play an increasingly important role in the field of CNC machining, driving the manufacturing industry toward a more efficient and precise future.III. Enhancing Production Efficiency and Reducing WasteIn modern manufacturing, enhancing production efficiency and reducing resource waste are crucial goals for the sustainable development of enterprises. The application of Artificial Intelligence (AI) in CNC machining technology provides an efficient and sustainable solution to achieve these goals. AI not only improves operational efficiency but also reduces material and energy waste through intelligent process optimization.Firstly, AI can significantly enhance the production efficiency of CNC machines. Through predictive maintenance and fault warning systems, AI can analyze machine operation data to predict mechanical failures and maintenance needs, thereby reducing unexpected machine downtime. This predictive capability not only ensures optimal machine operation but also effectively extends equipment lifespan, reducing economic losses caused by sudden failures. Additionally, AI's real-time adjustment functionality can automatically optimize machine operating parameters, such as speed and cutting force, during the machining process to adapt to different conditions. This not only increases production speed but also reduces material waste and energy consumption.Secondly, AI plays a critical role in reducing material waste. Through precise data analysis, AI can optimize cutting paths and material configurations to ensure the most efficient use of every piece of raw material. This not only enhances material utilization but also reduces waste generated during the production process. In the machining of high-value materials, such as aerospace aluminum or titanium alloys, this optimization is particularly important as material costs represent a significant portion of the overall production cost.Moreover, AI excels in energy management. It can intelligently regulate machine energy consumption based on actual production demands, such as automatically lowering energy usage during low-load periods or maximizing the use of low-energy modes without affecting production efficiency. This intelligent energy management not only reduces operational costs for enterprises but also contributes to environmental protection.In summary, the application of AI in CNC machining brings considerable economic and environmental benefits by enhancing production efficiency and reducing waste. This allows enterprises to respond more effectively to market changes and demands, driving the entire industry towards a more sustainable and intelligent future.IV. Quality Control and Process MonitoringIn modern manufacturing, ensuring product quality and monitoring the stability of the production process are of paramount importance. The application of AI technology in CNC machining not only enhances production efficiency but also significantly improves the accuracy of quality inspection and the real-time monitoring of processes. This technological innovation makes the manufacturing process more reliable, greatly reduces the production of defective products, and ensures the consistency of product quality.AI systems can utilize advanced sensing technologies and data analysis to monitor the machining status of CNC machines in real time. This includes monitoring tool wear, the dimensional accuracy of workpieces, and mechanical feedback during the machining process. With this data, AI can instantly detect any abnormalities that could lead to quality issues, such as excessive tool wear or deviations in machining parameters. Once these issues are detected, AI systems can automatically adjust machine parameters or pause the machining process until the problems are resolved, ensuring that every product meets high-quality standards.Furthermore, the application of AI enhances product consistency during the manufacturing process. In large-scale production, even minor variations can result in significant quantities of non-conforming products. AI systems can learn and record the successful machining conditions of each production run and apply these conditions to subsequent production, ensuring that all products meet the same high standards. This not only reduces quality fluctuations but also boosts customer confidence in the product quality.AI also plays a crucial role in reducing human errors. In traditional CNC operations, human factors often lead to product quality issues. The introduction of AI allows for the automation of many decisions and operations, reducing the likelihood of human errors. For instance, AI systems can automatically execute complex machining programs, reducing the need for manual adjustments by operators, thereby lowering error rates and enhancing overall product quality.In summary, the application of AI technology in quality control and process monitoring brings revolutionary improvements to the CNC machining field. Through real-time monitoring and intelligent adjustments, AI not only enhances product quality but also increases the stability and reliability of the manufacturing process. For modern manufacturing industries striving for defect-free production and high customer satisfaction, this holds immeasurable value.V. Future Prospects and Industry ApplicationsAs AI technology continues to develop and improve in CNC machining, its future application prospects appear even broader and more profound. AI will not only enhance existing manufacturing processes but also create new industry applications, leading the manufacturing sector towards greater efficiency, higher precision, and increased intelligence. Below are some important future prospects and potential industry applications of AI in CNC machining.Firstly, the further development of AI will make CNC machining more intelligent and automated. With advancements in machine learning and data analysis capabilities, future CNC machines will be able to more accurately predict machining outcomes and autonomously adjust machining strategies to meet complex and changing production requirements. This adaptive machining capability will not only improve production efficiency but also ensure product quality across various production scenarios.Additionally, AI will promote the application of CNC machining technology in more industries. For example, in the aerospace and automotive manufacturing sectors, where precision and reliability of parts are critical, AI-driven CNC technology can provide higher machining precision and better material utilization. In the medical industry, precision CNC machining can be used to manufacture highly complex medical instruments and implants, and the application of AI can ensure these products meet stringent safety and performance standards.The development of AI technology also drives CNC machining towards green manufacturing and sustainable development. By optimizing machining paths and energy control, AI helps reduce energy consumption and minimize waste generated during the production process. This not only helps manufacturing industries lower operational costs but also aligns with global environmental protection and sustainable development trends.With the integration of Internet of Things (IoT) technology, future CNC machining will become smarter and more interconnected. Various machines and production equipment in factories will be networked, allowing for real-time data exchange and analysis. This will enable comprehensive monitoring and management of the production process and coordinate production activities globally, enhancing overall operational efficiency.In summary, the further development of AI will bring significant changes and limitless possibilities to the field of CNC machining. From improving production efficiency to expanding new application areas, from enhancing quality control to promoting sustainable manufacturing, AI will play an increasingly important role in the future of manufacturing, bringing profound impacts to the global manufacturing industry.VI. Conclusion: Long-Term Prospects for the Collaboration between AI and CNC MachiningWith the widespread application of Artificial Intelligence (AI) technology in the manufacturing industry, especially in the field of CNC machining, we are witnessing a technological revolution that not only changes production methods but also redefines industrial standards. AI's contributions to enhancing CNC machining technology are significant, with promising and lasting prospects for collaboration. This is evident not only in the improvements in production efficiency and quality control but also in how AI is driving the manufacturing industry towards a smarter, greener, and more efficient future.Firstly, AI has already achieved remarkable success in improving the efficiency and precision of CNC machining technology. Through real-time data analysis and machine learning, AI systems can optimize machining processes, reduce equipment failures, and minimize production interruptions, thereby lowering production costs and improving product quality. This technological advancement benefits individual enterprises and enhances the overall competitiveness of the manufacturing industry.Moreover, the application of AI fosters continuous innovation in the manufacturing industry. As technology evolves, new AI algorithms and learning models are being developed, enabling CNC machines to handle more complex tasks and providing higher adaptability and better user experiences. This not only promotes further technological development but also brings new business opportunities and market potential to the manufacturing industry.The ongoing integration of AI technology is also pushing the manufacturing industry towards sustainable development. Through more precise data analysis and energy management, AI helps achieve more environmentally friendly production processes, reducing energy consumption and waste generation. This responds to global calls for environmental protection and aligns with the long-term development strategies of enterprises.Finally, as the global economic and technological environment evolves, the integration of AI and CNC machining technology will continue to deepen. This technological collaboration is not only a driving force for the modernization of the manufacturing industry but also key to realizing the long-term development strategies of enterprises. In the future, we can foresee AI playing an increasingly important role in improving production efficiency, reducing costs, enhancing product quality, and exploring innovative fields.In conclusion, the combination of AI and CNC machining technology brings revolutionary changes to today's manufacturing industry and lays a solid foundation for future development. This ongoing collaboration will ensure that the manufacturing industry can maintain innovation and competitiveness while continuously driving industrial progress and economic growth in the face of future challenges.ConclusionThrough this comprehensive exploration of the application of Artificial Intelligence (AI) in CNC machining technology, we can clearly see that AI is not only a driving force in modern manufacturing but also a key to future innovation and development. AI's achievements in enhancing machining efficiency, precision, and quality control have already demonstrated its irreplaceable value. Looking ahead, as technology continues to advance, AI will play an even more crucial role in the CNC machining field. It will not only propel the manufacturing industry towards higher efficiency and precision but also accelerate the transition towards sustainable and intelligent manufacturing. Through continuous technological innovation and strategic application, the combination of AI and CNC machining technology will continue to have a profound impact on the global manufacturing industry, ensuring that enterprises remain at the forefront in the competitive market.
06. 25. 2024
more
When we speak to AR (Augmented Reality)
technology, many people would come out the popular mobile game “Pokemon GO” in
their mind. Can you image that now they also use AR technology in machine tool
industry?
In the past, the use of AR had to be
experienced by downloading an APP. This time, we brought the WebAR technology
to you. You can enable the AR function via smart phone web. How convenient, isn’t
it?!
Now,
let’s do some finger exercise by picking up your smart phone to know CNV-750 capacity and 3 axes movements visually
and intuitively!
08. 04. 2022
Contact Information
- www.camprocnc.com
- No.12, Jingke 1st Road, Nantun Dist., Taichung City 408018, Taiwan
- +886-4-23500501
- +886-4-23500213