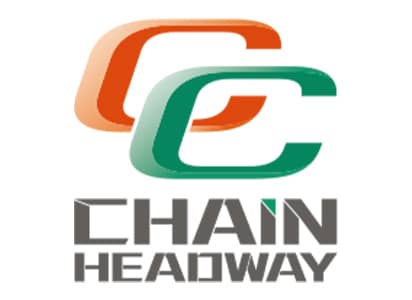
CHAIN HEADWAY CO., LTD.
CC CHAIN HEADWAY

News
more
One of the major challenges in metalworking is the complexity of operations that are difficult to replace with machinery. These processes often require expensive customized equipment. General mechanical equipment is often limited by product versatility and struggles to meet the specific needs of various metalworking tasks. In the machining process, surface treatment is a crucial step that not only affects the appearance of the workpiece but also directly influences its functionality and performance. Chain Headway’s DMB Diamond Grinding Brush brings new possibilities to metalworking.By integrating diamond grinding brushes into mechanical equipment, it successfully reduces reliance on manual labor while addressing issues of labor shortage and instability.The DMB Diamond Grinding Brush can be applied to a variety of workpiece materials, including aluminum, steel, nickel-based alloys, and tungsten carbide, as well as other hard and brittle materials. Using different grit sizes (#200, #600, and #1000) of diamond grinding brushes, it can address tool dulling, glass ceramics, quartz, nickel-based alloys, and all heat treated surfaces. It effectively removes cutting marks, deburrs, polishes surfaces, and removes rust, resulting in a smooth and polished workpiece surface.Key Features of DMB Diamond Brushes-Efficient Deburring and Polishing: Can remove burrs and achieve a polishing effect, with high strength, excellent resilience, and fatigue resistance.-High Hardness Processing: Capable of processing materials with a maximum hardness of up to HRC60°.-High Heat Resistance: Withstands temperatures up to 180°C.-Extended Lifespan and Maintenance: The DDB Diamond Dressing Board can restore the brush’s flatness, extending its service life and saving time and labor costs.-Time and Effort Saving: Improves surface roughness efficiently.DMDiamond Brushes are available in three types and sizes for various applications : To address diverse processing conditions and different sizes, shapes, and materials of workpieces, users can select the appropriate diamond grinding brush. This is particularly useful for flat or irregularly shaped workpieces, allowing for easy adaptation to different processing needs. Therefore, the Chain Headway Diamond Brush series has developed three sizes:Straight Shank Diamond Brushes, ⌀10-25mmShell Type Diamond Brushes, ⌀50-100mmStraight Shank T-type Diamond Brushes, ⌀25.4-63.5mmUsage of DMB Diamond Brushes-The grinding path should be completely larger than the workpiece, so the selected grinding brush diameter should be larger than the workpiece diameter.-It is recommended to set the cutting depth(Ap) of the diamond brush to 0.5~2mm and the speed(S) to 1000~4000 rpm. It should be used with cutting fluid for cooling.-The cutting diameter of the diamond brush should be between 25%~45% for optimal deburring results.-For removing burrs on edges, such as when milling with cutting tools, the spindle should rotate clockwise, and it’s recommended to use the diamond brush in reverse rotation of the spindle. Real Machining CaseCase One: Removing Machining MarksCase Two: DeburringCase Three: Surface PolishingThe exceptional performance of the DMB Diamond Brush allows for stable and precise machining of metal workpiece surfaces, saving both labor costs and significantly enhancing production efficiency. Additionally, it can meet diverse machining requirements, effectively improving workpiece surface roughness and bringing higher benefits to the production process.
10. 01. 2024
more
Shrink-fit tool holders which are made of special stainless material have become increasingly popular for high speed and high accuracy machining operations. The lack of moving parts in the tool head and strong, even grip on the tool shank make shrink-fit tool holders extremely cost effective. Cutting tool and tool holder life is extended because the exact fit reduces overheating during operation caused by vibration and imperfect alignment.
The holder must be heated to enable the tool to be inserted. The heater must heat the tool head evenly and make it hot enough that it expands just enough to fit the tool into the aperture. At Chain Headway we have designed a hot air heater that provides uniform and controlled heating at a competitive price. Hot air heaters take longer to heat the tool holder which are made of stainless material but offer very good value.
In our research and development, we studied the heating options available and analyzed their strengths and weaknesses. As a result, we believe we have produced the best hot air shrink-fit tool holder heater available today.
We focused on the following features that we found to be the most significant in workflow and quality control:
1.Airflow Management
Multiple apertures and controlled airflow supply even heating to the tool holder, reducing thermal stress.
2.Ergonomic Design
Convenient switch locations and sizes, tool holder mounts which rotate on bearings, and reliable clamping systems all improve the operator experience.
3.Operational Safety
Machine stability and ergonomic design reduce the risk of accidents.
4.Cycle Times
Exhaust apertures scaled to tool size allow less hot air to escape, and the tool holder is heated more quickly.
It is very important that the tool holder is heated evenly to ensure precise tool fitting, and reduce stress.
As a leading manufacturer of shrink fit tools to partners across the globe, Chain Headway will be your shrink-fit tool heater solutions.
11. 09. 2021
Contact Information
- www.chain-headway.com
- No.232, Wuquan Rd., Qingshui Dist., Taichung City 436037, Taiwan
- +886-4-26265252
- +886-4-26267941