Facing the Challenges in Machining of Tungsten Carbide
About Tungsten Carbide
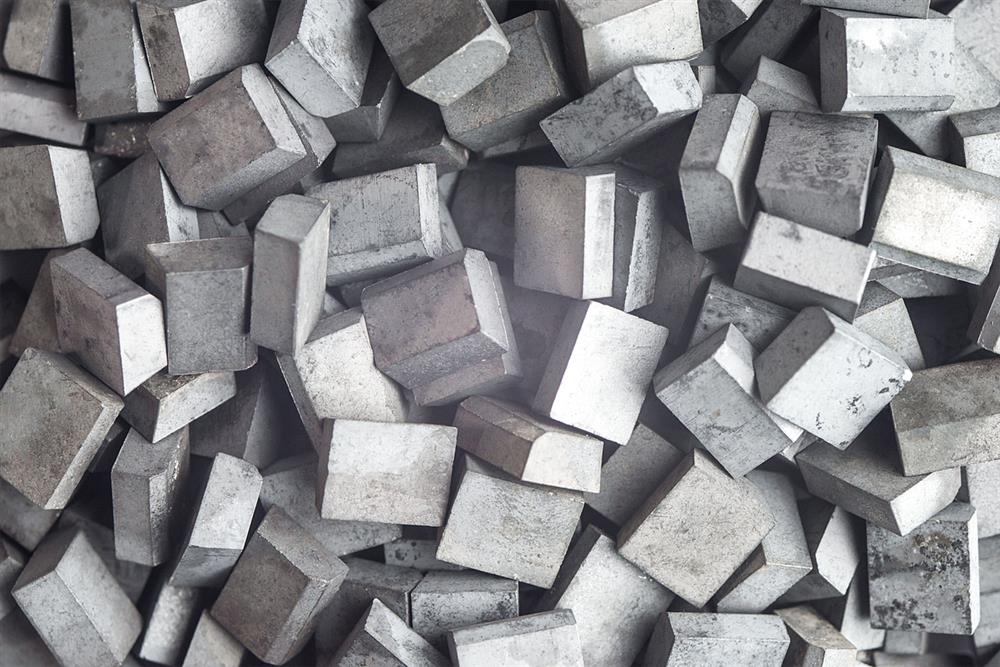
F1. brazed plates made of Tungsten Carbide material
Tungsten Carbide, also known as Cemented Carbide, is an alloy of tungsten and carbon. It is a metal-like substance and is approximately 2 to 3 times as rigid and dense as steel. Tungsten Carbide is often referred to as a Hard Metal, since it possesses very high hardness in relation to other metals. The Mohs hardness rating of Tungsten Carbide is around 8.5 ~ 9, and it is an extremely stable substance which does not oxidize under normal temperatures and keeps its stable characteristics even in severe environments.
Tungsten Carbide’s hardness and resistance to heat make it an ideal material for cutting tools and high-performance wear parts to be used in the environments under high temperature and high speed. Due to its exceptional hardness and wear resistance, Tungsten Carbide has a wide range of application in many industry sectors such as metal machining, wear parts for mining, metal forming tools, cutting tips for saw blades, etc.
How Tungsten Carbide Machining Works?
Owing to the extremely high hardness of Tungsten Carbide, it is impossible to be machined by traditional machining process such as turning, milling, or drilling. Though it can be machined by special tools, including PCD, CNB, and ceramic tools, these cutting tools will easily wear out and lose the sharpness.
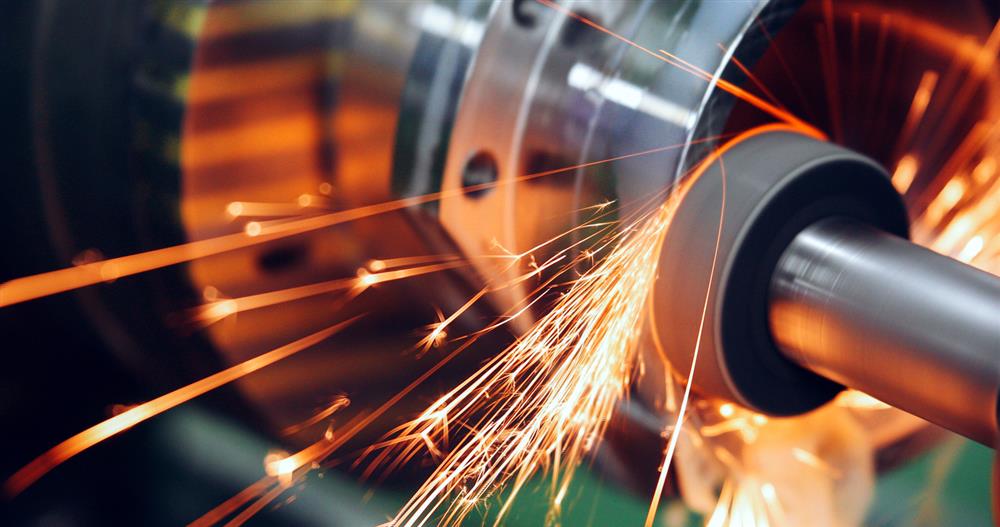
F2. metal material grinding process
Generally, Tungsten Carbide will be grinded with diamond tools or machined by electrical discharge machining (EDM). Though Tungsten Carbide is machinable by using these machining methods, the machining process is destined to face multiple difficulties and challenges.
Difficulties in Tungsten Carbide Machining
Tungsten Carbide Machining Challenges in Quality and Tool Life
Tungsten Carbide is incredibly hard and difficult to machine. Its hardness and brittleness make it easily cracked or chipped during the machining process, and it also chips the cutting tools very easily. Generally, it is impossible to be machined by traditional machining process. Though it can be machined by special tools, such as PCD, CNB, and ceramic tools, these cutting tools lose their sharpness easily.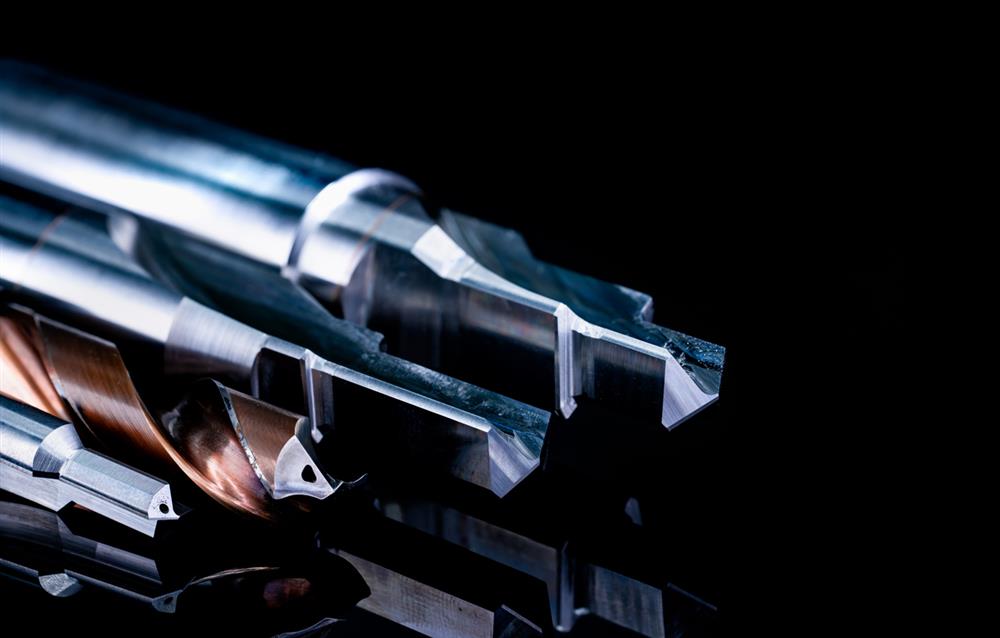
F3. carbide cutting tools for industrial applications
Tungsten Carbide Machining Challenges in Efficiency
The control of vibration and cutting force is extremely important to machining Tungsten Carbide, in virtue of its high density, rigidity, and brittleness. If the vibration and cutting force are not well-controlled, it is very subject to micro cracks and fragmentation. Therefore, the machining process is often extremely time-consuming and has constantly been tormenting the processing manufacturers when dealing with this material.What Does HIT Ultrasonic Machining Bring to Tungsten Carbide Machining?
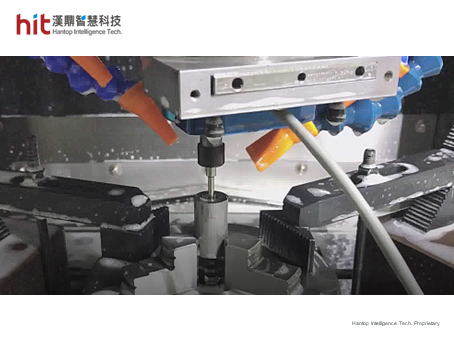
F4. Tungsten Carbide machining process
HIT’s ultrasonic-assisted machining technology provides the superimposition of the tool rotation with a high-frequency oscillation in longitudinal direction, generating over 20,000 times of micro-vibration per second. The mechanism helps reduce cutting forces and facilitates chip removal process.
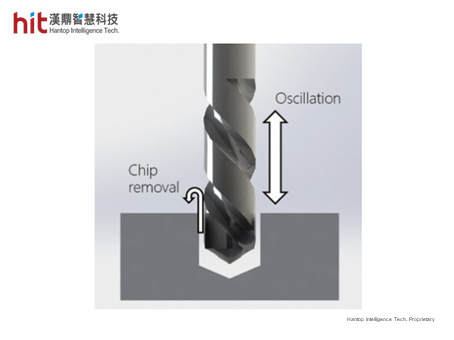
F5. HIT's ultrasonic machining technology with high-frequency oscillation in longitudinal direction facilitates chip removal process
The reduction in cutting forces not only decreases frictions between tools and workpieces, but also allows feed rates to be increased. This greatly improves the quality of workpieces and the stability of tool life, and saves quite an amount of processing time.
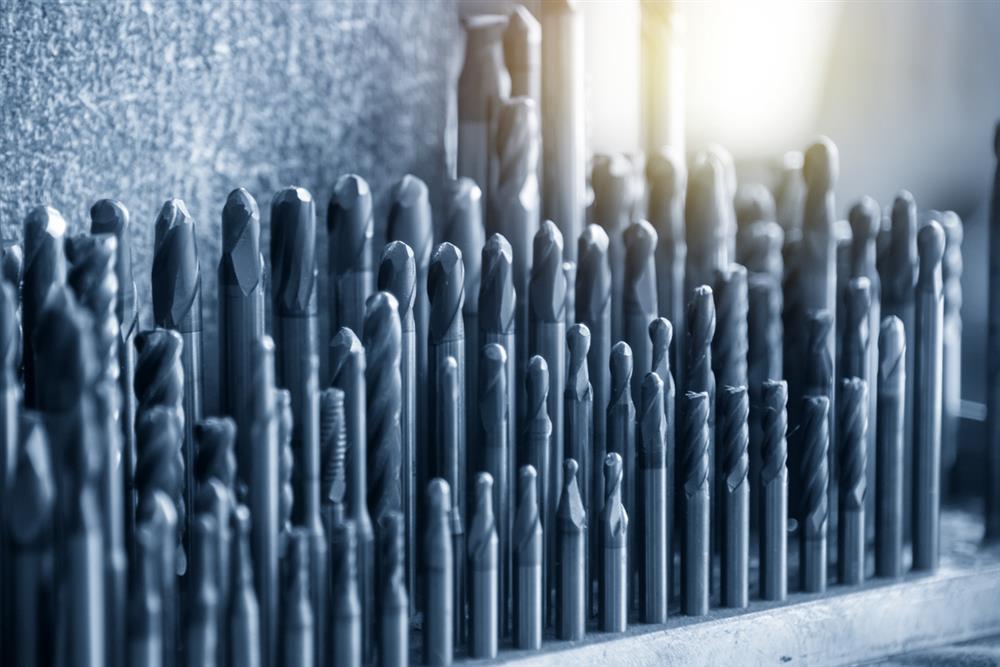
F6. HIT's ultrasonic machining technology helps reduction in cutting force, bringing more stability in tool life
Facilitating chip removal process diminishes frictions on both tools and workpieces caused by excessive amount of chips. HIT’s ultrasonic high-frequency micro-vibration allows chips to break easily and lessens the occurrences of entangled chips. This also displays a great benefit to both the quality of workpieces and the stability of tool life.
More information on HIT Ultrasonic Machining Technology
Two Successful HIT Cases of Tungsten Carbide Machining
Tungsten Carbide Machining Case 1 : (Slot) Trochoidal Milling
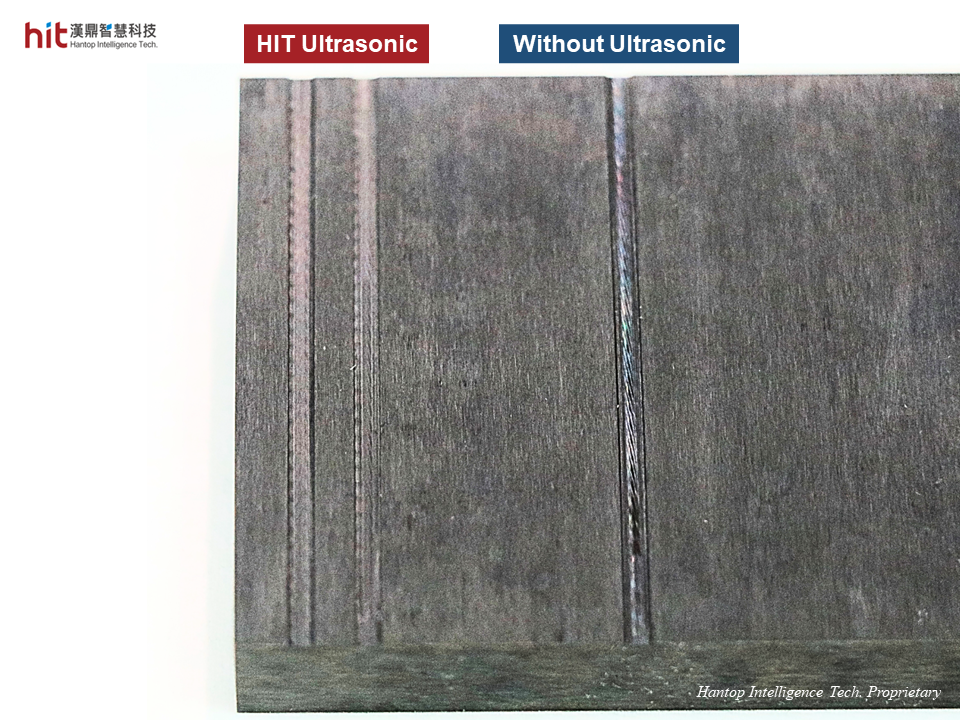
F7. Tungsten Carbide ultrasonic-assisted (slot) trochoidal milling workpiece
- With HIT ultrasonic, the high frequency micro-vibration allows the tool to constantly lift from workpiece. This brings better inflow of cutting fluid, offering better cooling effect and easier chip and carbonized diamond powder evacuation.
- F8. HIT ultrasonic-assisted slot trochoidal milling of tungsten carbide achieved better surface quality
- Under the same cutting parameters, with HIT ultrasonic, it helped reduce the surface roughness of the slots. There was no obvious tool marks or scratches left on the surface compared to that without ultrasonic.
- F9. HIT ultrasonic-assisted slot trochoidal milling of tungsten carbide brought better chip evacuation, preventing chips or carbonized diamond powder stuck on the tool
- Better chip and carbonized diamond powder evacuation helps reduce friction between tool and workpiece, which then reduces the cutting forces. This not only prolongs the tool life, but also helps enhance over 2x higher material removal volume.
More information on Tungsten Carbide: (Slot) Trochoidal Milling
Tungsten Carbide Machining Case 2 : Threading & Grinding
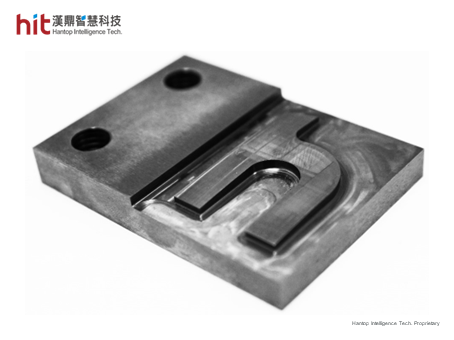
F10. Tungsten Carbide threading & grinding workpiece
HIT carried out threading (M10x1.5P) and grinding (h-shape) on a 50x70x10mm Tungsten Carbide workpiece. Using HIT’s ultrasonic tool holder HSKA63 with the integration of CTS, ATC, and CNC automation system, HIT completed the entire machining process within 5 hours, compared to over 12 hours by the traditional EDM process. The surface roughness of the h-shape grinding went from Ra > 0.8μm to the average of Ra < 0.1μm.
This feature is widely applied in the Precision Machinery industry, especially being used for Tungsten Carbide molds and punches.
More information on Tungsten Carbide : Threading & Grinding
Tungsten Carbide Machining FAQ
Q1 How do I know the tools I used to machine Tungsten Carbide can be fitted into HIT’s ultrasonic machining module system?
A1 HIT’s ultrasonic machining module has the ability to automatically scan for the proper frequency of the corresponding tool (within the standard frequency range of 20 – 32kHz). The system can even further adjust the frequency range, depending on specific tools used by the clients. Over the years, most of the tools in general have been validated to be available for HIT’s ultrasonic machining module system.
F11. HIT ultrasonic machining driver module
More information on HIT Ultrasonic Machining Module
Q2 How to adjust feed rates and amplitude when I start machining Tungsten Carbide with HIT’s ultrasonic machining module system?
A2 HIT aims to help clients face the challenges in Tungsten Carbide machining. This includes providing the optimum machining parameters and services to ensure clients having the best experiences in using HIT’s ultrasonic machining module system. It is not just buying a product from HIT, but obtaining the knowledge, services, and efforts from the most professional team.
F12. HIT ultrasonic tool holders
Tungsten Carbide Machining? Choose HIT
Contact us if you are looking for a better way to improve machining efficiency, quality, and tool life.