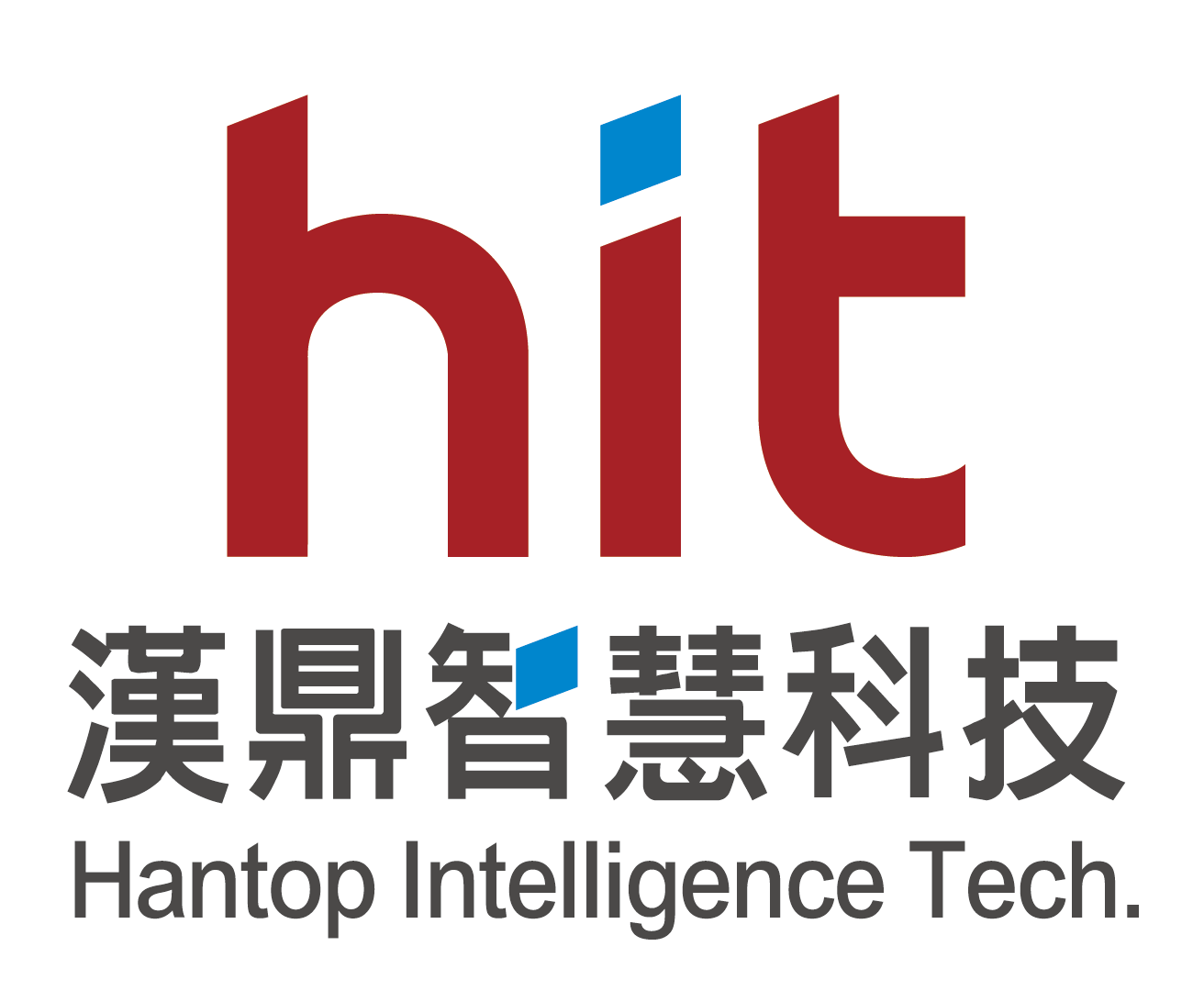
HANTOP INTELLIGENCE TECHNOLOGY CO., LTD.
Hantop Intelligence Tech.

Video
/ 12. 20. 2024
👍🏻 Machining Efficiency +5.5x
👍🏻 Tool Life +5x
👍🏻 Greatly Reduced Burrs
HIT utilized the ultrasonic machining module for profile milling (roughing) of STAVAX mould steel. The high frequency micro-vibration helped reduce cutting force and cutting heat under low rotation speed cutting. Radial depth of cut (Ae) was increased compared to the original process. This brought much shorter process time, reduction in tool wear, and prevention of massive burrs around workpiece.
💡Learn more about Ultrasonic-assisted 【Machining of Precision Mould】at https://www.hit-tw.com/advantage.aspx?id=1
STAVAX is a high-quality stainless plastic mould steel with excellent corrosion resistance, wear resistance, and machinability. It is mainly used for mould-making applications, such as plastic moulds (optical lenses, cosmetic packaging), medical device moulds (syringes, artificial joints), and automotive part moulds (light housings, trims).
Due to its high hardness and toughness, it may increase tool wear during cutting operations. Furthermore, during high-temperature processing, residual stress can cause material deformation, affecting machining precision.
💡Learn more about Ultrasonic-assisted Machining of【Advanced Materials】at https://www.hit-tw.com/advantage.aspx
👉🏻Want to know more about ultrasonic module products? Feel free to CONTACT US at https://www.hit-tw.com/contact.aspx 👈🏻
-
Hantop Intelligence Tech.
✨Optimized Machining Process of Advanced-Material with Ultrasonic Machining Module✨
☎️ +886-4-2285-0838
📧 sales@hit-tw.com
/ 08. 19. 2024
👍🏻 2x Higher Machining Efficiency
👍🏻 3x Better Workpiece Quality
👍🏻 Great Reduction in Tool Wear
HIT utilized the ultrasonic machining module for profile grinding of aluminum oxide (Al2O3) ceramic. Along with HIT's new product - Ultrasonic Electroplated Diamond Grinding Tool, the high frequency micro-vibration of ultrasonic brought easier removal of ceramic particles. The reduction in grinding force and tool wear not only contributed to great workpiece quality but also allowed for an increase in feed rate, which enhanced 2x of the overall machining efficiency.
💡Learn more about the case study【HIT Ultrasonic-assisted Profile Grinding of Aluminum Oxide Ceramic】at https://www.hit-tw.com/advantagedetails.aspx?id=292
Aluminum Oxide (Al2O3) ceramic is widely applied in the semiconductor industry, especially being made into key components for semiconductor manufacturing equipment, such as Ceramic Electrostatic Chuck (ESC, E-chuck). It uses electrostatic force to chuck/hold down wafer to ensure stability during wafer dicing process.
The high frequency micro-vibration of HIT ultrasonic-assisted machining technology offers better mechanism in flushing ceramic particles from the grinding tool. With HIT's new product - Ultrasonic Electroplated Diamond Grinding Tool, it helps bring great reduction in grinding force and tool wear. HIT aims to provide customers upgraded machining process with lower costs and high productivity!
💥NEW Product Launch!! HIT Ultrasonic Electroplated Diamond Grinding Tool💥
🔹 HIT customized ultrasonic electroplated grinding tool with exclusive formulation.
🔹 Work perfectly with HIT Ultrasonic Machining Module.
🔹 Maximize the benefits of CNC grinding process with HIT ultrasonic.
👉🏻Want to know more about the new product? Feel free to CONTACT US at https://www.hit-tw.com/contact.aspx 👈🏻
/ 05. 10. 2024
Learn Ultrasonic Machining in 1 Minute 💡
【What is Ultrasonic Machining?】
HIT #Ultrasonic-assisted #Machining Mechanism: Provides the tool over 20,000 times per second of high #frequency micro-#vibration in longitudinal (Z-axis) direction, which can be applied in #CNC #Drilling, #Milling, and #Grinding process.
【Benefits of Ultrasonic Machining?】
Especially for hard-to-cut and hard & brittle materials...
(including #metal, hard #steel, #ceramics, #glass, etc.)
👉🏻#MachiningEfficiency: hammering action generates micro-cracks on workpiece to help enhance #material #removal rate (#MRR).
👉🏻 #ToolLife: Cutting chips become smaller and bring easier #chip #evacuation, resulting in less tool wear and reduction of cutting force.
👉🏻 #WorkpieceQuality: Low #cutting #force diminishes #friction and greatly reduces size of #EdgeCracks, which enhances #surface and #hole quality.
【Why Choose HIT Ultrasonic?】
✨Wide selection of #toolholder specification (BT, CAT, HSK series) corresponds with common machine tool brands. Easy #installation of #module system.
✨#NonContact #power #transmission via ultrasonic power transmitter:
🔹Rotation speed is not limited by spindle speed.
🔹Less consumables and lower #energy #consumption (#ESG).
✨Searching for proper frequency of the cutting tool by automatic frequency-scan and frequency-lock; altering ultrasonic #oscillation #amplitude (according to different materials) by adjusting the ultrasonic power level.
💡Learn more HIT's application cases at https://www.hit-tw.com/advantage.aspx
💝Welcome to the World of Ultrasonic!
-
Hantop Intelligence Tech.
✨Solution Provider of Advanced-Material Machining Technology & Smart Automation Modules✨
☎️ +886-4-2285-0838
📧 sales@hit-tw.com
Feel free to contact us at https://www.hit-tw.com/contact.aspx
SHARE🔗|LIKE👍|SUBSCRIBE📌|CLICK ON🔔
👉Follow HIT on Facebook : https://www.facebook.com/hantopIntelligence
👉Follow HIT on LinkedIn : https://www.linkedin.com/company/hantopintelligence/
/ 05. 09. 2024
Ultrasonic Machining of Tungsten Carbide : (Slot) Trochoidal Milling|Hantop Intelligence Tech.
👍🏻 Better Surface Quality: Surface Roughness (Ra) - 2x lower
👍🏻 Longer Tool Life: Total Material Removal Volume (per tool) - over 2x higher
In conventional CNC machining, the strong cutting force and the constant contact between the tool and workpiece would consequently accelerate and intensify the tool wear, especially for a material as hard as tungsten carbide. The rapid wear of tool would increase the friction between tool and workpiece, resulting in serious damage to the surface quality.
The high frequency micro-vibration of HIT ultrasonic-assisted machining technology allowed for intermittent contact between the tool and workpiece. This greatly reduced cutting heat produced by constant contact between the tool and workpiece during conventional CNC machining. It also brought easier inflow of the cutting fluid. With easier chip and carbonized diamond powder evacuation, cutting forces were immensely reduced. Surface quality can be 2x better with 2x longer tool life under high speed machining.
💡Learn more about the case study at https://www.hit-tw.com/advantagedetails.aspx?id=200
💡Learn more about Ultrasonic Machining on Tungsten Carbide at https://www.hit-tw.com/newsdetails.aspx?nid=298
/ 05. 09. 2024
👍🏻 80% Higher Machining Efficiency
👍🏻 3x Longer Tool Life
👍🏻 90% Better Surface Quality
Nickel alloy (Inconel 718) is corrosion-resistant, heat-resistant, and has high mechanical strength. It is widely applied in the aerospace industry and primarily used as the material of aircraft turbine engine components, turbine blade, and other aircraft fasteners.
However, the work-hardening property of this kind of HRSA (Heat-Resistant SuperAlloy) has made chips with high hardness difficult to evacuate under continuous cutting. This leads to BUE (Built-Up Edge) on the tool blade, which not only increases tool wear but also damages the surface quality of workpiece.
The high frequency micro-vibration of HIT ultrasonic-assisted machining technology allowed for intermittent contact between the tool and workpiece. This greatly reduced cutting heat produced by constant contact between the tool and workpiece during conventional CNC machining. It also brought easier inflow of the cutting fluid. With easier chip evacuation, cutting forces were immensely reduced. Surface quality can be 90% better with 3x longer tool life under high speed machining.
💡Learn more about the case study at https://www.hit-tw.com/advantagedetails.aspx?id=221
💡Learn more about Ultrasonic-Assisted Circular Pocket Milling of Nickel Alloy (Inconel 718) at https://www.hit-tw.com/advantagedetails.aspx?id=223
/ 05. 09. 2024
👍🏻 4x Higher Machining Efficiency
👍🏻 75% Longer Tool Life
👍🏻 1.5x Better Surface Quality
Nickel alloy (Inconel 718) is corrosion-resistant, heat-resistant, and has high mechanical strength. It is widely applied in the aerospace industry and primarily used as the material of aircraft turbine engine components, turbine blade, and other aircraft fasteners.
However, the work-hardening property of this kind of HRSA (Heat-Resistant SuperAlloy) has made chips with high hardness difficult to evacuate under continuous cutting. This leads to BUE (Built-Up Edge) on the tool blade, which not only increases tool wear but also damages the surface quality of workpiece.
The high frequency micro-vibration of HIT ultrasonic-assisted machining technology allowed for intermittent contact between the tool and workpiece. This greatly reduced cutting heat produced by constant contact between the tool and workpiece during conventional CNC machining. It also brought easier inflow of the cutting fluid. With easier chip evacuation, cutting forces were immensely reduced. Surface quality can be 1.5x better with 75% longer tool life under high speed machining.
💡Learn more about the case study at https://www.hit-tw.com/advantagedetails.aspx?id=223
💡Learn more about Ultrasonic-Assisted Keyway Side Milling of Nickel Alloy (Inconel 718) at https://www.hit-tw.com/advantagedetails.aspx?id=221
/ 05. 08. 2024
Ultrasonic Grinding of Quartz Glass : Micro-channel Trochoidal Machining | Hantop Intelligence Tech.
HIT utilized ultrasonic machining module for micro-channel trochoidal machining of quartz glass. The high frequency micro-vibration helped reduce cutting forces, which made the max. size of edge-cracks around the micro-channels 2x smaller than that without ultrasonic. Easier inflow of cutting fluid brought better particle flushing, resulting in the reduction of tool wear.
💡Learn more about HIT Ultrasonic-assisted Machining at https://www.hit-tw.com/
Due to the high hardness and brittleness of quartz glass, the risk of trochoidal grinding of quartz glass resides in massive chipping and edge-cracks around the micro-channels. The prevention of edge-cracks on the product is essential, for it may lead to turbulent flows within the microfluidic system. Therefore, it usually needs to go through etching for post-process to remove edge-cracks. The larger the cracks, the more time it will need to take to remove the edge-cracks during the etching process.
HIT ultrasonic-assisted trochoidal machining of quartz glass helped reduce cutting forces. This made the maximum size of edge-cracks 2x smaller than that without ultrasonic. The tool constantly lifting from workpiece allowed for easier inflow of cutting fluid, which not only brought better particle flushing but also less tool wear.
💡Learn more about Ultrasonic Machining on Quartz Glass case at https://www.hit-tw.com/advantagedetails.aspx?id=189
/ 05. 08. 2024
Ultrasonic Grinding of SiC (Silicon Carbide) : (Helical) Circular Ramping|Hantop Intelligence Tech.
HIT utilized ultrasonic machining module for (helical) circular ramping of SiC (silicon carbide). The high frequency micro-vibration helped reduce cutting forces, which helped improve surface roughness by 72%. Ultrasonic-assisted grinding mechanism also brought better particle flushing, preventing the tool from ceramic dust accumulation.
💡Learn more about HIT Ultrasonic-assisted Machining at https://www.hit-tw.com/
SiC (Silicon Carbide) bears excellent chemical and mechanical stability with high-temperature and thermal shock resistance, which also makes it an ideal material for semiconductor fabrication commodities, such as SiC substrates, SiC wafer susceptors, SiC wafer carriers, SiC E-chucks, etc.
However, due to the high hardness and brittleness of silicon carbide, the risk of (helical) circular ramping SiC resides in poor surface quality with massive tool marks. If the grinding forces are not well-controlled (due to serious cumulative ceramic particles stuck in the pores of grinding tool) during the process, it would take more time to do tool dressing in order to restore the grinding ability of the tool.
HIT ultrasonic-assisted (helical) circular ramping of SiC (silicon carbide) helped reduce grinding forces. This helped improve the surface roughness (Sa) by 72% with mitigating tool marks on the surface. The tool constantly lifting from workpiece allowed for easier inflow of cutting fluid, which brought better particle flushing and prevented the tool from massive ceramic dust accumulation.
💡Learn more about Ultrasonic Machining on SiC case at https://www.hit-tw.com/advantagedetails.aspx?id=188
/ 05. 07. 2024
Ultrasonic Machining of S45C Medium Carbon Steel : Gun Drill Deep Drilling|Hantop Intelligence Tech.
HIT utilized the ultrasonic machining module for the deep hole drilling on S45C Meidum-Carbon Steel with gun drill. With the aspect ratio being 25x, under the same rotation speed, the entire machining efficiency was enhanced 2 times higher than that without ultrasonic. The high frequency micro-vibration of HIT ultrasonic-assisted machining technology allowed for intermittent contact between the tool and workpiece, achieving better chip and cutting heat removal with only 40bar of coolant through spindle (CTS). The chip size was 91% smaller than that without ultrasonic, which greatly reduced tool wear.
💡Learn more about HIT Ultrasonic-assisted Machining at https://www.hit-tw.com/
With HIT ultrasonic-assisted machining technology, the ultrasonic module can be installed onto the current CNC machines, without using specialized gun drilling systems. The high frequency micro-vibration of HIT ultrasonic-assisted machining technology allowed for intermittent contact between the tool and workpiece. This greatly reduced cutting heat produced by constant contact between the tool and workpiece during conventional CNC machining. It also brought easier inflow of the cutting fluid. The machining mechanism also helped with chip breakage. The chips became 91% smaller and broke naturally once it reached to certain volume, under the machining condition of 40bar of CTS. With better chip and cutting heat removal, the tool wear was immensely reduced. Overall, the machining efficiency was enhanced 2 times higher with less energy consumption, which also helps in fulfilling the ESG responsibility.
💡Learn more about Ultrasonic Machining on Tungsten Carbide at https://www.hit-tw.com/newsdetails.aspx?nid=298
💡Learn more about Ultrasonic Machining on Titanium Alloy at https://www.hit-tw.com/newsdetails.aspx?nid=300
/ 05. 06. 2024
Ultrasonic Machining of Tungsten Carbide : M2 Internal Threading|Hantop Intelligence Tech.
HIT utilized the ultrasonic machining module for the M2 internal threading on Tungsten Carbide. The high frequency micro-vibration of HIT ultrasonic-assisted machining technology allowed for intermittent contact between the tool and workpiece, achieving better chip and cutting heat removal. This greatly reduced tool wear and ensured the complete profile of M2 internal thread under 3 times higher machining efficiency.
💡Learn more about HIT Ultrasonic-assisted Machining at https://www.hit-tw.com/
The high hardness and wear resistance tungsten carbide have brought great challenges and difficulties for industrial manufacturers, especially for the machining of M2 internal thread. Generally, EDM (Electrical Discharge Machining) is the most commenly used machining process when it comes to the machining of tungsten carbide. However, it would inevitably create a white layer upon the machining surface, resulting in worse workpiece quality. The followed-up manufacturing steps to remove the white layer were needed and could be extremely time-consuming.
The high frequency micro-vibration of HIT ultrasonic-assisted machining technology allowed for intermittent contact between the tool and workpiece. This greatly reduced cutting heat produced by constant contact between the tool and workpiece during conventional CNC machining. It also brought easier inflow of the cutting fluid. With better chip and cutting heat removal, the tool wear was immensely reduced. With the fact that less machining processes were needed compared to EDM, the entire machining efficiency was greatly enhanced while achieving the completeness of M2 internal thread on tungsten carbide.
💡Learn more about Ultrasonic Machining on Tungsten Carbide at https://www.hit-tw.com/newsdetails.aspx?nid=298
/ 05. 05. 2024
Ultrasonic Machining of Al2O3 Ceramic : M2 Internal Threading|Hantop Intelligence Tech.
HIT utilized the ultrasonic machining module for the M2 internal threading on 99.7% Aluminum Oxide (Al2O3). The high frequency micro-vibration of HIT ultrasonic-assisted machining technology allowed for intermittent contact between the tool and workpiece, achieving better chip and cutting heat removal. This greatly reduced tool wear and ensured complete profile of M2 internal thread dimension.
💡Learn more about HIT Ultrasonic-assisted Machining at https://www.hit-tw.com/
Aluminum Oxide (Al2O3) ceramic has excellent chemical resistance and thermal stability, which makes it widely applied in the semiconductor manufacturing processes (including etching and thin film processes), especially being made into the key components (such as ceramic electrostatic chuck) for wafer foundry.
However, the high hardness and brittleness of aluminum oxide have brought great challenges and difficulties for industrial manufacturers, especially for the machining of M2 internal thread dimension. In conventional CNC machining, the strong cutting force and the constant contact between the tool and workpiece would consequently accelerate and intensify the tool wear. The major diameter of the internal thread became smaller as the thread went deeper. Eventually, the screw could not be fully locked into the thread, resulting in serious impact on the quality of product.
The high frequency micro-vibration of HIT ultrasonic-assisted machining technology allowed for intermittent contact between the tool and workpiece. This greatly reduced the cutting heat produced by constant contact between the tool and workpiece during conventional machining. It also brought easier inflow of the cutting fluid. With better chip and cutting heat removal, the tool wear was immensely reduced. This ensured the completeness of the profile of M2 internal thread and successfully enhanced the quality of workpiece.
/ 05. 04. 2024
Ultrasonic Machining of SiC (Silicon Carbide) : Micro-Drilling|Hantop Intelligence Tech.
HIT utilized the ultrasonic machining module for the micro-drilling on SiC (Silicon Carbide). HIT's ultrasonic-assisted machining technology greatly enhanced the hole quality. The size of edge-cracks is reduced by 53%, compared to that without ultrasonic. The ultrasonic machining module offers the highest amount of precision and flexibility when it comes to fabricating components that require high quality, high precisional repeatability, and high yield rate.
💡Learn more about HIT Ultrasonic-assisted Machining at https://www.hit-tw.com/
Silicon carbide has a Mohs hardness rating of 9, making it an excellent material choice for high-precision mechanical components. The material also bears excellent chemical and mechanical stability with high-temperature and thermal shock resistance, which also makes it an ideal material for semiconductor fabrication commodities, such as substrates and showerheads. Showerheads are used for even distribution in the semiconductor industry. The hole quality and configuration of the concentrated holes on the product are important to maintain high yield rate of wafer foundry.
However, due to the high hardness of silicon carbide, the risk of machining SiC resides in poor hole quality with massive size of edge-cracks. If the thrust force and torque are not well-controlled during the drilling process, both the quality and positional precision of the holes will be severely impacted. HIT ultrasonic-assisted machining technology can help reduce cutting force/heat and allows for an easier chip removal process, resulting in great improvement in workpiece quality.
💡Read more about Ultrasonic Machining on SiC deep hole drilling case at https://www.hit-tw.com/advantagedetails.aspx?id=122
/ 05. 03. 2024
Ultrasonic Machining of Titanium Alloy (Ti-6Al-4V) : Side Milling|Hantop Intelligence Tech.
HIT utilized the ultrasonic machining module for Titanium Alloy (Ti-6Al-4V) side milling. HIT's ultrasonic-assisted machining technology allowed for 3 times faster of the cutting speed, resulting in the increase in feed rate and machining efficiency.
The high-frequency ultrasonic micro-vibration reduced the cutting force and cutting heat, which ensured better surface quality and improved the tool life.
The ultrasonic machining module offers the highest amount of precision and flexibility when fabricating components that require high quality, high precisional repeatability, and high yield rate.
💡Learn more at https://www.hit-tw.com/
SHARE🔗|LIKE👍|SUBSCRIBE📌|CLICK ON🔔
👉Follow HIT on Facebook : https://www.facebook.com/hantopIntelligence
👉Follow HIT on LinkedIn : https://www.linkedin.com/company/hantopintelligence/
Titanium alloy (Ti-6Al-4V) offers a combination of lightweight, high strength, low density, good corrosion resistance and ductility. It is also recognized for their exceptional resistance to a wide range of chemical environments provided by a thin, invisible but extremely protective surface oxide film.
These extraordinary properties make it ideal for numerous kinds of industrial applications, including biomedical industry (titanium bone plate, artificial joint), aerospace and defence industry (turbine blade, aircraft engine components), 3C electronic industry (Apple watch Ultra bezel, smartphone phone case), and electric car industry (underbody of Tesla Model S).
However, titanium alloy has bad thermal conductivity and work-hardening quality. This would accumulate massive amount of cutting heat during the machining process, resulting in the chips being repeatedly adhesive to both the tool and workpiece. The adhesive wear of the tool then leads to the breakage on the tool's rake face and worsens the surface roughness of the workpiece.
/ 05. 02. 2024
Ultrasonic Machining of Al2O3 Ceramic : Micro-Drilling|Hantop Intelligence Tech.
HIT utilized the ultrasonic machining module for the micro-drilling 99% Aluminum Oxide (Al2O3) ceramic. HIT's ultrasonic-assisted machining technology greatly enhanced the machining efficiency by 60%, and maintained high quality workpieces with no edge-cracks or burrs on the drilling holes by sight. The ultrasonic machining module offers the highest amount of precision and flexibility when it comes to fabricating components that require high quality, high precisional repeatability, and high yield rate.
💡Learn more at https://www.hit-tw.com/
Aluminum Oxide (Al2O3), is also known as Alumina. The major difficulties in machining Al2O3 reside in its material properties of high hardness and brittleness. Poor surface quality and subsurface damages have become serious challenges during the machining process. However, this material's excellent chemical resistance and thermal stability have made it ideal for semiconductor fabrication commodity applications.
In addition to aluminum oxide, HIT can also apply the ultrasonic machining technology to a wide range of demanding materials, including quartz glass, silicon carbide (SiC), tungsten carbide, titanium alloys, and even composites.
💡Read more HIT's application cases at https://www.hit-tw.com/advantage.aspx
💡Read more HIT's technical ceramic machining at https://www.hit-tw.com/newsdetails.aspx?nid=191
💡Watch other ultrasonic machining module video at https://www.hit-tw.com/applications.aspx
📩If you are looking for a better way to improve the machining efficiency, workpiece quality, and stability in tool life, please feel free to contact us at https://www.hit-tw.com/Contact.aspx
SHARE🔗|LIKE👍|SUBSCRIBE📌|CLICK ON🔔
👉Follow HIT on Facebook : https://www.facebook.com/hantopIntelligence
👉Follow HIT on LinkedIn : https://www.linkedin.com/company/hantopintelligence/
Contact Information
- www.hit-tw.com/
- No. 41, Gongyequ 21st Rd., Nantun Dist., Taichung City 408017, Taiwan
- +886-886-4-22850838
- +886-886-4-22850836