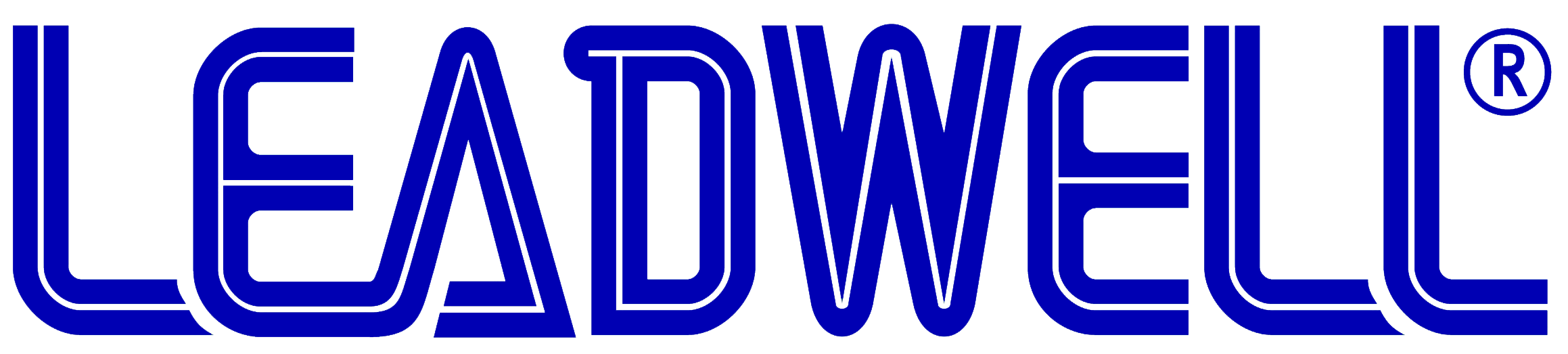
LEADWELL CNC MACHINES MFG., CORP.
LEADWELL

News
more
LEADWELL has been recognized with the prestigious "Gold Energy Conservation Label" for two of its products: the V-40IT 5-Axis Machining Center and the T-6SMY Dual-Spindle Horizontal Lathe, demonstrating its leadership in the field of green intelligent manufacturing. Additionally, the LT-208LSY Dual-Spindle Horizontal Lathe has been awarded the Silver Energy Conservation Label, further underscoring the company's outstanding achievements in energy-saving and carbon-reduction technologies.
The awarding of both Gold and Silver Energy Conservation Labels not only affirms Taiwan LEADWELL relentless efforts over the years but also symbolizes the company's commitment to the energy-saving and carbon reduction initiatives advocated by the Taiwan Machine Tool & Component Builders' Association (TMBA). These awards were established by TMBA to aid the tool machine industry in its green transformation, aimed at fostering the development of green machine tool products in Taiwan through the promotion of industry standards and energy-saving technologies.
LEADWELL is dedicated to providing energy-efficient and environmentally friendly products and services, always prioritizing customer needs. The company appreciates the hard work of all team members, especially their ongoing focus on multi-axis processing and intelligent manufacturing solutions, as well as their active participation in energy-saving, carbon reduction, and energy efficiency improvements.
The V-40IT 5-Axis Machining Center and the T-6SMY Dual-Spindle Horizontal Lathe are renowned for their high precision and efficiency. The V-40IT is capable of completing all machining processes in one setup, making it particularly suited for complex freeform surface work. The T-6SMY is favored in aerospace and automotive manufacturing due to its energy-efficient design and high-performance operation.
Furthermore, the LT-208LSY Dual-Spindle Horizontal Lathe features advanced technologies such as spindle thermal compensation, enhancing both production efficiency and quality. Its modular design has significantly reduced inventory levels and shortened preparation times, speeding up delivery schedules. These products all comply with ESG standards, showcasing LEADWELL leadership in the realm of green manufacturing.
12. 03. 2024
more
1.
**Innovating
for the Future**
In today's rapidly
evolving manufacturing sector, precision and efficiency are key to success. To
meet the increasingly stringent industrial standards and production demands, we
introduce the BC-800T 5-axis machining center. This machine not only represents
the forefront of technological innovation but also embodies our relentless pursuit
of precision in craftsmanship and operational efficiency. The following content
will delve into the unique features and superior performance of the BC-800T,
demonstrating its application value in modern manufacturing.
2.
**Core Technology and Design Advantages**
The BC-800T 5-axis
machining center combines precise craftsmanship and innovative technology,
showcasing a new realm of high-performance machine tools. This advanced machine
employs the latest five-axis simultaneous machining technology, achieving extremely
precise machining results and significantly reducing the need for workpiece
unloading and fixtures. Such design not only shortens processing time but also
significantly enhances production efficiency, making the production process
smoother and more economical.
3.
**Structural Stability and Precision
Machining**
The BC-800T is
meticulously designed, utilizing FEA analysis to ensure optimal performance and
reliability of the machine structure. Its ultra-wide base and saddle design
maintain excellent stability even during high-speed movements. Additionally,
the structural design of the BC-800T is optimized by maintaining a greater
distance between two linear guides, which reduces potential deformations caused
by the weight of the worktable and ensures better weight distribution to the
saddle, thereby achieving superior accuracy and minimizing distortion.
4.
**Power System and High-Speed Operations**
In terms of power
transmission, the BC-800T is equipped with dual nut ball screws on the X and Y
axes, DD motors on the rotary table, and roller guides on the X, Y, and Z axes,
all ensuring stability during high-speed movements. The rapid feed rates reach
36 meters per minute on the X and Y axes and 30 meters per minute on the Z
axis, allowing the BC-800T to perform tasks quickly and accurately. This rapid
feed capability enables the machine to handle large or complex workpieces
effectively, reducing downtime and thereby enhancing overall production
efficiency. This exceptional performance is particularly beneficial in
industrial applications requiring large volumes of precise machining,
significantly improving product quality and machining accuracy, ensuring each
workpiece meets the highest manufacturing standards.
5.
**Flexibility and Multifunctionality**
The BC-800T also
features an efficient three-axis bearing oil lubrication system, which helps
reduce thermal expansion and significantly extends the lifespan of machine
components. Moreover, its B-axis rotary table offers a ±110-degree range of
motion, and the C-axis rotary table provides a 360-degree range of motion,
supporting loads up to 400 kilograms with a diameter of 650mm, accommodating a
variety of machining needs. These rotary tables' design not only offers high
flexibility but also meets the processing requirements of various complex
shapes, allowing the BC-800T to handle workpieces of different materials and
specifications. This flexibility is especially suitable for industries like
aerospace, automotive manufacturing, and mold making, where workpieces vary
greatly in shape and require high precision. This not only enhances production
efficiency but also significantly expands the machine's application range.
6.
**Spindle Performance and Precision
Machining**
The main worktable of
the BC-800T measures 1700x650mm with a maximum load capacity of 1400 kilograms,
complemented by a high-performance built-in spindle with a maximum speed of
12,000 rpm. Additionally, its torque is 95 Nm in the Fanuc system and 120 Nm in
the Siemens system. The spindle's HSK-63T taper ensures a stable connection
between the tool and the machine. This combination of high speed and powerful
torque allows the BC-800T to easily handle hard materials while maintaining
smooth and precise cutting processes. This is advantageous for applications
requiring high-intensity cutting tasks, such as aerospace component
manufacturing or high-precision mold making.
7.
**Tool Management and Production Efficiency**
Furthermore, the
high-speed capability of the spindle, coupled with a precise control system,
allows the BC-800T to achieve industry-leading machining quality during
delicate surface finishing and complex detail processing. This machining
capability not only enhances the overall aesthetics of the product but also
ensures dimensional accuracy and surface smoothness during the machining
process, thereby reducing the need for subsequent finishing and enhancing the
final product's market competitiveness. The BC-800T also features a chain-type
tool magazine that can accommodate up to 30 tools, providing quick tool changes
and flexible handling of complex machining tasks. Enhanced chain durability and
tool change efficiency ensure the machine's efficiency and reliability during
extended operations. Laser and circular positioning accuracy tests, rotary center
diagnostics, and ISO precision tests ensure the BC-800T's accurate and reliable
performance, reducing waste, enhancing productivity, and increasing profits.
This efficient tool management system not only saves tool change time but also
enhances the continuity of the machining process, especially in mass production
or scenarios requiring frequent tool changes.
8.
**Tool Magazine Design and Operational
Convenience**
The design of the
tool magazine considers ease of operation and safety, with precise tool
positioning ensuring quick tool location and reducing the risk of operational
errors. Additionally, the enhanced durability of the tool magazine not only
improves its wear resistance but also ensures its lasting performance under
high load and high-frequency usage conditions. This tool magazine design allows
the BC-800T to quickly adapt to changes in production demands for diversified
and technically demanding machining tasks, enhancing the machine's market
adaptability and user experience.
9.
**Driving Industry Innovation and
Efficiency**
The launch of the
BC-800T 5-axis machining center marks a significant step forward in our
provision of efficient and precise solutions. Through continuous technological
innovation and a commitment to quality, we believe the BC-800T will bring
unprecedented production efficiency and operational experience to users.
Whether facing complex industrial challenges or everyday high-precision
requirements, the BC-800T provides reliable support, helping businesses enhance
their competitiveness and advance the industry.
06. 19. 2024
more
1. **Guide: How to
Recommend Efficient CNC Mill-Turn Machines for the Automotive Manufacturing
Industry**
In the automotive manufacturing industry,
choosing the right CNC mill-turn machine is crucial because the efficiency and
precision of these machines directly impact production quality and
cost-effectiveness. Here are some key considerations to help agents recommend
the most suitable CNC mill-turn machines for the automotive manufacturing
industry:
l Understanding the Specific Needs of the Automotive Manufacturing
Industry
The automotive manufacturing industry has
specific requirements for CNC mill-turn machines. These include high precision,
high speed, and high stability in machining capabilities, as automotive parts
must meet strict quality standards and production specifications. Additionally,
as automotive designs become increasingly complex, CNC machines need multi-axis
machining capabilities to handle intricate geometries and fine details.
l Evaluating Machine Specifications
Agents should thoroughly understand the
technical specifications of various CNC mill-turn machines, including spindle
speed, tool change time, machining range, and precision. For the automotive
manufacturing industry, high-speed, high-precision machines can significantly
enhance production efficiency and reduce defect rates. Therefore, agents need
to evaluate and recommend machines based on these technical indicators.
l Reliability and After-Sales Service
Automotive manufacturing is highly
dependent on equipment reliability. Machine stability and durability are vital,
so agents should choose brands with a good market reputation and strong
technical support. Additionally, high-quality after-sales service is crucial,
including prompt repair responses and regular maintenance services, ensuring
long-term stable operation and reducing the risk of production downtime.
2.
**Perspective: Choosing the
Best CNC Mill-Turn Machine Suppliers in the Global Market**
Choosing suitable CNC mill-turn machine
suppliers for the automotive manufacturing industry in the global market
requires in-depth analysis and careful decision-making. Here are some key steps
to help agents screen and evaluate the best suppliers in the global market:
l Evaluating Technical Strength
Firstly, the supplier's technical strength
is a core factor in decision-making. Agents should assess whether the supplier
possesses advanced technology and research and development capabilities and can
provide high-precision, high-speed, and high-stability CNC mill-turn machines.
The supplier's technical strength directly relates to product quality and
performance, so careful evaluation is necessary.
l Confirming Product Certification and Standards
In the global market, different countries
and regions have various certifications and standards for machinery and
equipment. Agents need to confirm whether the supplier's products meet local
safety standards and quality certifications, impacting the legality of product
imports and the safety and reliability of usage.
l Assessing After-Sales Service and Support
After-sales service and technical support
are important considerations when choosing suppliers. High-quality after-sales
service ensures that machines receive timely repairs and maintenance during
operation, reducing downtime and production losses. Agents should understand
the supplier's after-sales service network and technical support capabilities
to ensure they can meet the long-term needs of customers.
l Referencing Customer Reviews and Case Studies
Agents can reference other customers'
reviews and successful case studies to judge the supplier's reliability and
market reputation. Successful cases and good reviews can boost the supplier's
credibility, helping agents make more confident decisions.
3.
**Improving Automotive Parts Production
Efficiency: How Customers Choose CNC Mill-Turn Machines**
In the automotive manufacturing industry,
selecting the right CNC mill-turn machine is crucial for improving parts
production efficiency. Here are some key steps to help automotive manufacturing
customers choose the most suitable CNC mill-turn machine:
l Analyzing Production Needs
Firstly, customers need to analyze their
production needs in detail, including the types of parts, machining precision
requirements, batch sizes, and production speeds. These factors directly impact
the required machine specifications and performance. For example,
high-precision, multi-axis CNC mill-turn machines are ideal for parts requiring
high precision and complex geometries.
l Evaluating Machine Performance
Performance evaluation is key when choosing
CNC mill-turn machines. Customers should consider technical indicators such as
spindle speed, machining range, automatic tool change systems, and tool life.
High-performance machines can significantly improve production efficiency,
reduce production costs and defect rates, and ensure product consistency and
quality.
l Considering Operational Convenience and Maintenance
The operational convenience and maintenance
needs of machines are also important considerations in the selection process.
User-friendly machines can reduce training time and improve operator
efficiency. Additionally, low maintenance needs and convenient repair services
can reduce downtime and ensure continuous and stable production.
l Understanding After-Sales Service and Support
Choosing suppliers with excellent
after-sales service and technical support is crucial. Customers should
understand whether the supplier provides comprehensive after-sales services,
including installation and commissioning, operation training, regular
maintenance, and emergency repairs. High-quality after-sales service ensures
long-term stable operation and reduces production risks caused by machine
failures.
4.
**Case Study Analysis: Application of CNC
Mill-Turn Machines in the Automotive Manufacturing Industry**
Case study analysis is an effective way to
understand the application and effects of CNC mill-turn machines in the
automotive manufacturing industry. These cases demonstrate how these machines
significantly improve production efficiency and quality.
l Successful case studies showcase the significant advantages of CNC
mill-turn machines in the automotive manufacturing industry, including improved
production efficiency, reduced defect rates, and enhanced product quality. By
applying these advanced machines, automotive manufacturers can achieve
modernized and automated production, meet the ever-changing market demands, and
maintain a competitive edge. Agents can use these cases to demonstrate the
value and application effects of CNC mill-turn machines to potential customers,
promoting sales and establishing strong cooperative relationships.
5.
**The Long-Term Investment Value of CNC
Mill-Turn Machines in Automotive Manufacturing**
In the automotive manufacturing industry,
investing in CNC mill-turn machines is not only to address current production
needs but also to achieve long-term economic benefits and competitive
advantages. Here are some long-term investment values that CNC mill-turn
machines bring to automotive manufacturers:
l Improving Production Efficiency
CNC mill-turn machines can integrate
multiple machining processes, completing turning and milling in one setup,
significantly improving production efficiency. Efficient automatic tool change
systems and precise numerical control technology can shorten production cycles,
increase output, and meet the demand for rapid delivery.
l Reducing Production Costs
High-precision CNC machines can
significantly reduce defect rates, minimize r material waste, thereby lowering
production costs. Additionally, the durability and stability of these machines
mean fewer maintenance needs and downtime, further saving operational costs.
l Enhancing Product Quality
The high-precision machining capabilities
of CNC mill-turn machines ensure the consistency and quality of each part. This
is crucial for the automotive manufacturing industry, as high-quality parts can
improve overall vehicle performance and safety, enhance consumer confidence,
and boost brand image.
l Increasing Competitiveness
Investing in advanced CNC technology allows
automotive manufacturers to adapt to market changes and technological
challenges, maintaining a competitive edge. As automotive designs become
increasingly complex, CNC mill-turn machines with multi-axis machining
capabilities and flexibility can meet the growing product demands, winning more
market share.The TM-1700 series of fully automated
machining equipment from Taiwan LEADWELL Computer Machinery is designed to meet
the needs of high-efficiency precision machining. It can quickly manufacture
various industrial parts, including automotive, aerospace, and electronic
products. Our advanced machines are equipped with flexible parameter settings
and a variety of tool head options, making it possible to produce parts of
various specifications and sizes, greatly enhancing productivity and
operational efficiency.
06. 07. 2024
more
With twin spindle and twin turret structure, finite element analysis is used on a 45-degree slant bed design to support the rigid base for spindle and turret.Leadwell itself power turret not only magnifies all appropriate configurations to satisfy all machining requirements but also ensures machine quality andutuilization with intelligent function.
07. 25. 2022
Contact Information
- www.leadwell.com.tw
- No. 8, Xingke Rd., Houli Dist., Taichung City 421007, Taiwan
- +886-886-4-25589008
- +886-886-4-25589027