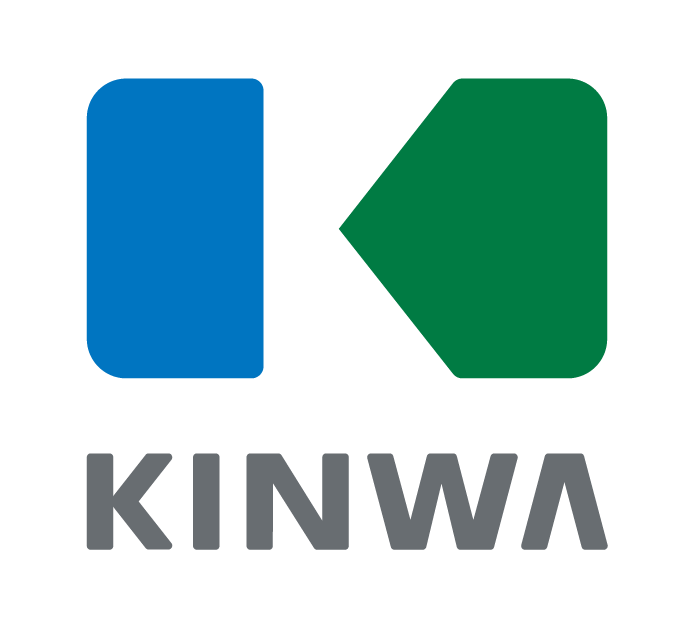
CHIN HUNG MACHINERY CO., LTD.
KINWA

News
more
A Comprehensive Guide to Ensuring Factory and Equipment Safety After an EarthquakeAfter an earthquake, even if everything seems intact on the surface, there could be hidden risks, especially in factory equipment and production environments. If these risks are not promptly inspected and addressed, they may affect production efficiency or even lead to more significant safety hazards.We have compiled a post-earthquake inspection guide that highlights the following key areas:Calibration and Testing of Precision Machines: Including the alignment of spindles, tools, and guide rails.Comprehensive Factory Environment Inspection: Such as checking the stability of stacked materials, the safety of lifting equipment, and structural integrity of walls.Inspection of Fire and Emergency Systems: Ensuring the proper functioning of fire safety systems and emergency escape routes.This article will help you quickly understand the necessary inspection and precautionary measures after an earthquake, ensuring that your factory and equipment operate in a safe and secure condition.👉 Read the full article and start your inspections today🔗 Safety First, Stability AlwaysTogether, let's safeguard safety and ensure stable production!
01. 21. 2025
more
🎉 Celebrating 40 Years of KINWA Lathes: Driving New Heights in the Industry!Since its founding in 1968, KINWA Lathes by JINN FA Precision has been committed to delivering highly efficient and precise turning solutions to manufacturers worldwide. The iconic CL-10 Lathe, launched in 1985, not only earned international acclaim but also became a cornerstone of success for countless businesses, contributing significantly to Taiwan’s industrial growth.✨ To commemorate the 40th anniversary of the CL-10 Lathe, we are excited to offer an exclusive limited-time promotion!From now until March 31, 2025, purchase any KINWA machine to enjoy exclusive benefits. This is the perfect opportunity to upgrade your production capabilities and join us in driving the next wave of industrial innovation.💡 Product Highlights:CL-10 Lathe: Renowned for its reliable multi-angle machining capabilities, trusted by industries like hand tools and sanitary ware.The New CL-100 Lathe: Enhanced with a dual V-guideway, extended Z-axis travel, and superior stability for even greater precision and versatility.⏳ Don’t miss out on this limited-time offer!We invite you to join us in advancing industrial excellence. For details, contact your nearest distributor or our sales team.#Manufacturing #MachiningTechnology #TaiwanExcellence #LatheInnovation #KINWA40Years #IndustryUpgrade #CNCPrecisionMachiningThe related news report is as follows.金和車床CL-10榮耀40年 推出優惠購機方案 - 商情 - 工商時報
01. 02. 2025
more
🎉 Congratulations to Team Taiwan for a 4-0 victory over Japan and winning the WBSC Premier12 Championship!A new chapter in Taiwan's baseball history has been written! In the 2024 WBSC Premier12 tournament, Team Taiwan defeated the formidable Japanese team, ending their 27-game winning streak and breaking a 20-year winless streak against Japan. This historic victory, the first-ever Premier12 championship for Taiwan, is a moment of pride for the entire nation!To celebrate this extraordinary achievement, KINWA LATHE is launching a Limited-Time Discount Offer:📌 Promotion Period: From now until December 31, 2024📌 Details: Enjoy special discounts on all products! Contact your local distributors or our sales team for more information.Promotion HighlightsSuperior Quality Recognized by Japan: KINWA lathe machines are known for their precision and reliability, earning accolades in international markets.Exclusive Discounts: Celebrate Team Taiwan’s championship win with unbeatable discounts. It’s the perfect time to upgrade your equipment!Taiwan's Hidden Champion, Partnering with You: As a trusted partner in the industry, we’ve been empowering businesses worldwide with innovative solutions for years.Contact Us Now📧 Email: ufkinwa@ms15.hinet.net🌐 Website: www.kinwa-lathe.com
11. 25. 2024
more
We are excited to announce that KINWA Lathe will be participating in JIMTOF 2024, the Japan International Machine Tool Fair, held at Tokyo Big Sight from November 5th to November 10th, 2024. As one of the world’s premier exhibitions for machining technology, we are thrilled to showcase our highly acclaimed traditional lathes at booth E2047.Our traditional lathes offer exceptional mobility and can flexibly machine various workpieces without the need for CNC programming, making them ideal for small to medium-sized factories and manufacturers. Whether you're looking for stable and reliable equipment or aiming to increase production flexibility, our traditional lathes are designed to meet your needs.Exhibition Details:Exhibition Dates: November 5th - November 10th, 2024Venue: Tokyo Big SightBooth Number: E2047We warmly invite you to visit our booth and experience firsthand how our traditional lathes can enhance your productivity and operational efficiency. We look forward to seeing you at JIMTOF 2024!
10. 16. 2024
more
KINWA (KINWA Lathe): A Fifty-Year Legacy of Corporate Spirit and InnovationThe Spirit of Sustainable Management: KeepingSince its establishment in 1968, KINWA has always adhered to the spirit of sustainable management. For us, "Keeping" means continuously optimizing our business operations and protecting the environment, ensuring the long-term development and prosperity of the company. Our goal is not only to achieve immediate success but also to build a solid foundation for future generations.The Spirit of Inheritance"Inheritance" holds a significant place in the core philosophy of KINWA. We cherish the knowledge and technology accumulated over the past 50 years and are committed to passing these valuable technical legacies on to the next generation. Through continuous education and training, we ensure the preservation and development of our professional knowledge and craftsmanship.Guiding Improvement: NavigateAt KINWA, "Navigate" represents our commitment to continuous improvement. We constantly seek new methods to optimize our processes and services, ensuring that we can meet market changes and fulfill customer needs. Our goal is to guide industry standards through innovation and efficiency.Winning Customer SatisfactionIn this highly competitive market, "Win" for us means winning customer satisfaction. KINWA values each customer's experience and is dedicated to providing products and services that exceed expectations. Our success is built on the foundation of establishing long-term customer relationships.Quality First: Accuracy"Accuracy" is another key value of KINWA, representing our commitment to quality first. Whether it's product design, manufacturing, or service, we adhere to the highest quality standards. This attention to precision and detail is the cornerstone of earning our customers' trust and respect.Conclusion: KINWA Moving ForwardFor fifty years, KINWA has been continuously progressing and innovating. Our corporate spirit—'Keeping Sustainable Management,' 'Inheritance of Technical Knowledge,' 'Navigate Continuous Improvement,' 'Win Customer Satisfaction,' and 'Accuracy in Quality'—not only represents our past but also guides our future. As we move towards the next fifty years, KINWA will continue to uphold these core values, creating greater value for our employees, customers, and society.
01. 11. 2024
more
Here, we delve into the close relationship between Chin Ho Lathe and Chin Hung Precision Co., Ltd., exploring the rich and unique history of this brand.The Birth and Development of Chin Ho LatheThe story of Chin Ho Machine Factory began in 1968, when our founder started an impressive manufacturing journey with just one lathe. In 1973, with the official establishment of Chin Ho Machine Factory, we focused on manufacturing high-quality lathes, quickly establishing our own brand in the industry, known as "Chin Ho Lathe."The Transformation of Chin Hung MachineryWith the progress of time and growing market demands, by 1980, we not only expanded our factory size but also upgraded our company to a limited company, renaming it "Chin Hung Machinery Co., Ltd". Despite this change in name, the core values and commitments of the "Chin Ho Lathe" brand remained constant.Enhancing the International Brand ImageIn order to further enhance our image in the international market, we started using the Japanese pronunciation of "Chin Ho", "KINWA," as part of our brand name in 2000. This move not only highlighted our global vision but also brought broader recognition to the brand.Innovation in Brand Identity SystemBy 2023, we innovated once again, launching a new brand identity system "KINWA". It combines a blue rectangle symbolizing the rotating workpiece and a green pointed shape representing the turning tools, cleverly integrating a hidden letter 'K,' symbolizing our relentless pursuit of innovation and commitment to brand heritage.Gratitude and Future OutlookOver the years, whether as "Chin Ho Lathe" ,"KINWA Lathe" or "Chin Hung Machinery Co., Ltd.," we have always maintained the same professional spirit and heritage, continually providing our customers with the highest quality lathe products. We are extremely grateful to every customer and partner for their support and trust over the years. Looking forward, we will continue to strive, constantly innovate, and take our brand to an even broader future.We look forward to witnessing the next milestone of "KINWA" with you!#IndustrialManufacturing #TraditionalInnovation #QualityAssurance #ChinHoLathe #ChinHungMachinery
12. 15. 2023
more
In-Depth Guide to Purchasing Traditional Lathes: Key Considerations Shared by Industry ExpertsIn today's industrial manufacturing sector, selecting the right lathe is pivotal for enhancing production efficiency and ensuring product quality. For businesses and professionals planning to purchase a traditional lathe, understanding the key considerations is crucial. Here are the seven essential factors to consider, as recommended by industry experts:1. Application and Workpiece SpecificationsWhen choosing a lathe, the first consideration should be the type, size, and material of the workpieces you intend to process. Your choice of lathe should be based on whether it's used for general metalworking, heavy-duty machining, or precision engineering.2. Lathe SizeThe bed length, swing over the bed, and maximum turning diameter of the lathe are critical factors that determine the size of workpieces you can process. Choosing a lathe with the appropriate dimensions ensures that your machining needs are met.3. Power and Speed RangeSelecting the appropriate speed range based on the material and machining requirements is crucial. Consider the spindle speed of the lathe and whether it offers the suitable speed gears and ranges for your specific needs.4. Accuracy and RepeatabilityDifferent production requirements call for varying levels of accuracy and repeatability. For applications requiring high precision, choosing a lathe with high accuracy specifications is key.5. Brand and After-Sales ServiceOpting for a well-known brand can generally guarantee better quality and service. Good after-sales service not only provides necessary technical support but also saves on future maintenance and repair costs.6. Safety FeaturesOperational safety is an aspect that cannot be overlooked in industrial manufacturing. Ensure that the chosen lathe is equipped with adequate safety features, such as emergency stop switches and guards, which are essential for the safety of the operators.7. Budget and PriceAfter considering all technical specifications and functional requirements, your choice should also take into account the budget. Selecting a lathe that fits your budget while meeting all your needs is a wise decision.Additional TipsBeyond these basic elements, when selecting a lathe, you should also consider additional accessories, tools, and the expandability of the lathe. These factors can impact your final purchasing decision.Purchasing a traditional lathe is an important and complex process. With these professional insights, you can make a more informed choice, ensuring that your investment yields the maximum return.
11. 30. 2023
more
Amidst the tide of advanced technology in today's manufacturing industry, traditional lathes have emerged as a captivating craft. Despite the gradual rise of CNC lathes, the unique heritage craftsmanship and technological allure of traditional lathes remain undeniable. Through the manipulation of mechanical handwheels and manual operations, traditional lathes demonstrate exceptional turning and threading capabilities, solidifying their position as an excellent choice for processing rotationally symmetric components.1. Exquisite Craftsmanship:Operating traditional lathes demands proficient artisanal skills, precise tool manipulation, and an abundance of professional knowledge. Leveraging the finesse of mechanical handwheel manipulation, workpieces gracefully rotate on the spindle, while the toolholder is manually adjusted by the operator for precise cutting. This intricate manual operation imbues each processing step with an artistic significance, ensuring the precision and quality of the finished product. The synergy between artisans' dexterity and extensive experience makes the traditional lathe a tool for crafting art.2. Fusion of Tradition and Modernity:Despite the clear advantages of automation and efficiency held by CNC lathes, the flexibility and adjustability of traditional lathes continue to attract customers with unique processing requirements. For non-standard-shaped components, traditional lathes offer adaptability, rendering them the unparalleled choice. This fusion of traditional and modern technology enhances the competitive edge of traditional lathes in the market.3. Heritage and Technological Allure:With a history spanning centuries, traditional lathes have witnessed the passing down of techniques through generations. The allure of inherited craftsmanship is deeply embedded in the fabrication of every component, and each operation pays homage to history and continuity. The preservation of craftsmanship is not merely a technical continuation but also the perpetuation of past wisdom, allowing historical value to shine in the modern era.4. Enhancing Product Quality:For certain specialized components, traditional lathes remain indispensable. In sectors like aerospace, medical, and high-precision instrument manufacturing, traditional lathes offer heightened accuracy and surface quality during machining, ensuring products meet the highest quality standards. This advantage in exceptional quality positions traditional lathes as indispensable players in critical fields.5. Future Outlook:Despite the pressures of competition from CNC lathes, traditional lathes are far from obsolete. Craft enthusiasts and artisans still uphold the traditional lathe as a precious tool, viewing it not only as a manufacturing device but also as a revered asset. Looking ahead, traditional lathes are poised to seamlessly integrate with CNC lathes and other modern machining technologies, unveiling new possibilities. The future of traditional lathes is poised for diversity, evolving into a masterpiece that intertwines modern technology and ancient craftsmanship.In summary, traditional lathes embody not only the inheritance of craftsmanship but also an inexhaustible technological allure. Their exceptional role in the modern manufacturing industry will continue to be vital as times evolve. Whether as a testament to the past or a revelation of the future, traditional lathes will persist in guiding the development of manufacturing, scripting a new chapter in the legend of craftsmanship. Let us collectively witness the resplendence of this remarkable skill in the future!
09. 26. 2023
more
Expert Insights into Machine Tool Knowledge: Exploring Lathe Categories and ApplicationsMachine tools play a pivotal role in the manufacturing sector, and among these tools, the lathe stands out as a common and indispensable machine tool. The lathe is renowned for its capability to process symmetrical components, and based on its distinct characteristics, we can categorize lathes into several primary types, each of which we will delve into.1. Functional Classification:Conventional Lathe:This type of lathe employs mechanical handwheels or manual controls to finely manage the cutting process. While it requires the operator's direct involvement, conventional lathes remain a practical choice in specific contexts.CNC Lathe (Computer Numerical Control Lathe):Equipped with a computer numerical control system, CNC lathes can automatically govern the cutting process. This not only enhances production efficiency but also ensures higher machining accuracy, rendering them an integral part of modern manufacturing.2. Structural Classification:Flat Bed Lathe:In flat bed lathes, the tool post remains parallel to the ground, and the workpiece is positioned on a horizontal bed. This design provides enhanced stability for operations, making it suitable for a variety of machining tasks.Slant Bed Lathe:In slant bed lathes, the tool post is angled, and the workpiece is positioned on a tilted bed. This unique structure aids in the more efficient expulsion of chips, consequently elevating machining efficiency.Vertical Lathe:The tool post in vertical lathes is perpendicular to the ground, and the workpiece is processed on a vertical spindle. This design is commonly employed for specific machining requirements, such as hole drilling.3. Capability Classification:Single-Axis Lathe:Capable of machining solely along a single coordinate axis, single-axis lathes have limited capability. Nevertheless, they find utility in simple component machining tasks.Multi-Axis Lathe:Multi-axis lathes can simultaneously operate on multiple coordinate axes, providing enhanced machining versatility and flexibility. This is particularly critical for the machining of intricate components.4. Size-based Classification:Small-Sized Lathe:Suited for machining small-sized components, these lathes are ideal for precision work.Medium-Sized Lathe:Suitable for processing medium-sized components, medium-sized lathes find widespread application across various industrial sectors.Large-Sized Lathe:Designed to handle larger components, such as propeller shafts, large-sized lathes accommodate greater dimensions and weights.5. Process-based Classification:Conventional Lathe:Primarily employed for flat, cylindrical, and helical surface machining, conventional lathes enjoy a broad application spectrum, making them the preferred choice for many machining tasks.Specialized Lathe:Utilized for shaping components with unique shapes or purposes, such as multi-axis lathes and thread-cutting lathes, these machines are adept at tackling more challenging machining operations.Different types of lathes offer distinct advantages in various scenarios. By comprehending specific requirements, we can better select the appropriate lathe, ensuring efficient and precise machining processes. Whether it's a conventional lathe or an advanced CNC lathe, they all play pivotal roles in modern manufacturing.
09. 06. 2023
more
What is the Lathe? The Concept of Turning ProcessThe lathe, also known as a turning machine, is a type of machine used for performing turning operations.Turning process refers to the method of cutting and shaping an object's surface by rotating the object itself and using cutting tools, resulting in a smooth and symmetrical shape.This process is somewhat similar to the hand-throwing process in pottery making. Just like when crafting pottery, the clay keeps rotating, and the artisan shapes the clay into a symmetrical form by hand. Additionally, any rough or uneven parts can be smoothed out using bamboo strips to create a polished appearance.In the turning process, the object being worked on is referred to as the "workpiece," while the tools used for cutting are called "tools" or "cutting tools."To secure the rotating workpiece, a "fixture" or "clamping device" is utilized, and the axis that enables the rotation of the workpiece is known as the "spindle."Lathes can be classified into two types: vertical lathes and horizontal lathes. The "vertical lathe" has its spindle oriented vertically, while the "horizontal lathe" has its spindle parallel to the ground.Both vertical and horizontal lathes have their respective applications, used for different types of turning operations.#Lathe #Turning #Cutting Tools #Workpiece #Fixture #Spindle #Machining
08. 30. 2023
more
KINWA Brand, Worldwide Reputation of Quality
KINWA LATHE was established in Taichung City in 1973, manufacturing precision high-speed lathes as its foundation, in 1980, we moved the factory to Da-Ya District and reorganized as CHIN HUNG MACHINERY CO., LTD. Since 1990, we have been developing and manufacturing CNC lathes, greatly expanding our market presence. The KINWA brand has gained a well-known, worldwide reputation for high quality lathes.
KINWA’s broad range of excellent quality, high-speed precision lathes are found as standard equipment throughout many Taiwan and overseas manufacturing industries. With the development of CNC lathes, KINWA’s popular, high-tech, Gang-Type and Flat-bed CNC lathes have become essential the manufacturing industry. Over the years, KINWA LATHE has made huge progress in designing and providing customized precision high-speed and CNC lathes.
As the demand for automation growing, KINWA LATHE’s abundant experiences in precision lathe manufacturing enable us to help customers of hand tool manufacturing to plan linear robot automation of lathes and also to cooperate with customers who manufacture home appliance parts to use vibrator bowl to achieve the purpose of automation. Furthermore, we work with a world-famous shock absorber corporation to plan automated load/unload robots to accomplish the purpose of automation to increase productivity and yield rate throughout the entire plant.
With the post-pandemic price of raw materials continually raising, KINWA LATHE still insists on using components made in Taiwan by local manufacturers. We are keeping our commitment to providing only the best quality products and service for our worldwide customers.
11. 05. 2021
Contact Information
- www.kinwa-lathe.com
- No.10, Tianxin St.,Daya Dist., ,Taichung City 428010, Taiwan
- +886-4-25666113
- +886-4-25665254