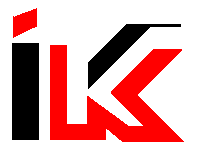
YIH KUAN ENT CO., LTD.
IK milling heads manufacturer

News
more
In mold manufacturing, workpiece structures are often not limited to flat surfaces or straight holes. Many products require angled cutting, side holes, cooling channels, or deep cavity machining. For traditional milling machines with linear spindle directions, these demands are often difficult to achieve. At this point, the angle milling head becomes an indispensable solution.Challenges in Mold MachiningCooling channels and side-hole machining: Molds often require angled or transverse holes to ensure efficient cooling during product forming.Deep cavities and complex geometries: Linear milling tools cannot always reach, and the spindle direction must be changed with an angle head.Balancing efficiency and precision: Traditional processes require repeated setups or multiple machines, which are time-consuming and increase the risk of errors.Yih Kuan's Angle Milling Head SolutionsYih Kuan offers a range of angle milling heads to help mold manufacturers achieve greater flexibility in their machining processes:IK-U90 Universal Angle HeadCapable of 360° rotation, ideal for multi-angle and complex structural cutting.IK-D90 Right Angle HeadStable precision, specialized for side holes and cooling channel machining.IK-D90L Extended TypeDesigned for deep cavity machining, with extended spindle length to avoid interference.With these modular angle milling heads, mold manufacturers do not need to purchase new machines. Instead, they can expand the machining capabilities of their existing equipment.Proven BenefitsA plastic mold manufacturer previously required two machining processes to complete cooling channel holes, and the error rate was high. After adopting Yih Kuan’s angle milling heads, the operation could be completed in just one setup, improving efficiency by 40% and significantly reducing scrap rates.In today’s competitive and deadline-driven market, such improvements not only lower costs but also play a key role in winning more orders.ConclusionAngle milling heads are not just auxiliary tools—they are essential “efficiency boosters” in mold machining.Yih Kuan will showcase a wide range of angle milling heads at the upcoming exhibition. We sincerely invite you to visit our booth, exchange ideas, and discover how upgrading your milling head can break machining limitations and unlock more possibilities for your factory.
08. 20. 2025
more
In modern manufacturing, vertical milling machines are a core asset on the shop floor. Their stability and versatility make them indispensable for transforming raw materials into high-precision components. At the heart of these machines lies the milling head — a component whose design and performance directly influence machining accuracy, surface finish, and overall productivity. For manufacturers aiming to break through production limits and improve quality, understanding and optimizing the milling head is not merely an option — it is a necessity.The Milling Head: The Hidden Power Behind PerformanceThe milling head houses the spindle and cutting tools while transmitting power and rotational force needed for cutting. Its structure and condition have far-reaching impacts across the entire machining process:Precision and Accuracy: A rigid, well-maintained milling head reduces vibration and deflection, allowing for tighter tolerances and more accurate part dimensions.Superior Surface Finish: An optimized head ensures smooth and consistent cutting, minimizing or eliminating the need for secondary finishing operations.Extended Tool Life: Reduced runout and vibration prolong cutting tool lifespan, saving costs on consumables and reducing unplanned downtime.Increased Material Removal Rates: Stable and efficient power transmission enables higher cutting speeds and feed rates, significantly improving throughput.Versatility: The right milling head expands your machine’s capabilities — from heavy roughing to fine finishing on a variety of materials.How to Optimize Your Milling Head: Key Areas to Focus On1. Choosing the Right Milling HeadNot all milling heads are built the same. When selecting or upgrading, consider the following:Spindle Speed and Torque: Match spindle characteristics to your cutting tools and materials. High-speed spindles suit small tools and fine work, while high-torque models are better for large-diameter tools and aggressive cutting.Rigidity and Structure: Look for robust builds, often using cast iron or high-grade steel, to ensure stiffness and vibration damping.Bearing Quality: Precision bearings are essential for minimizing runout and extending spindle life.Mounting Interface Compatibility: Ensure seamless integration with your existing machine structure to avoid costly modifications and misalignment.2. Proper Maintenance Is CriticalThe milling head is a precision assembly and demands careful maintenance:Regular Lubrication: Follow manufacturer guidelines to lubricate gears and bearings, preventing wear and overheating.Alignment Checks: Periodically verify the squareness and parallelism between the milling head and the machine table — key to accurate machining.Vibration Monitoring: Excessive vibration may indicate worn bearings or imbalance. Early detection helps avoid costly failures.Cleanliness: Keep the head free from chips, coolant residue, and dust that could contaminate lubricants or damage sensitive parts.3. Leveraging Advanced Features and TechnologyModern milling heads often come equipped with features to boost performance:Direct-Drive Spindles: With no belts or gears, these offer high rigidity, minimal vibration, and excellent thermal stability.Automatic Tool Changer (ATC) Interface: Efficient tool changes require tight integration with the ATC system — crucial for reducing manual intervention and setup time.Through-Spindle Coolant: Delivers coolant directly to the cutting edge for better chip evacuation, extended tool life, and improved surface finish.Thermal Compensation: Some advanced heads use sensors and software to offset thermal expansion, maintaining precision during long machining cycles.The Real-World Impact: Improving More Than Just a ComponentOptimizing your milling head is more than a component upgrade — it’s an investment in your entire production workflow. The benefits include:Lower Scrap Rates: Higher accuracy means fewer defects and less waste.Faster Turnaround Times: Improved efficiency leads to shorter lead times and faster delivery.Reduced Production Costs: Longer tool life, fewer stoppages, and less rework all contribute to significant cost savings.Enhanced Product Quality: Better surface finishes and tighter tolerances help meet and exceed customer expectations.YIH KUAN Insight: A Trusted Milling Head Partner for Peak Machine PerformanceIn the pursuit of reliable output and high-efficiency machining, the role of the milling head should never be underestimated. With over 50 years of experience in milling head design and manufacturing, YIH KUAN Enterprise specializes in upgrading vertical milling machines and conventional equipment. We provide a full range of solutions — from turret milling heads and heavy-duty spindles to modular upgrades and customized flange designs.We are more than just a supplier — we are your partner in production optimization. Through professional assessment, drawing integration, installation guidance, and post-sale support, YIH KUAN helps customers extend machine life, improve cutting conditions, and stay ahead in a competitive market.Now is the perfect time to re-evaluate the core of your machine. Let YIH KUAN help you unlock your machine’s full potential and rise to new levels of manufacturing excellence.
07. 25. 2025
more
In the world of precision machining, knee mills remain essential equipment across a wide range of industries—from mold and die making to automotive parts and prototyping. However, aging components or outdated technology can limit performance. That’s where Yih Kuan comes in. If you're considering a performance-enhancing upgrade, Yih Kuan Enterprise Co., Ltd. offers industry-leading solutions designed to elevate your knee mill’s capabilities with innovation, reliability, and long-term value.Expertise in Milling TechnologyWith decades of experience in the development and production of milling heads, Yih Kuan has earned its reputation as a trusted leader in the machining industry.We understand the structural challenges and mechanical dynamics of knee mills.Our vertical turret milling heads are engineered to deliver high torque, smooth spindle rotation, and stable cutting, making them perfect for both manual and CNC retrofits.Industries such as aerospace, mold & die, and maintenance machining rely on our precision heads to ensure dimensional accuracy and repeatable results.Innovative, Performance-Focused SolutionsYih Kuan isn’t just a parts supplier—we’re a technology partner. Our R&D team is focused on delivering solutions that meet today’s most demanding machining requirements.Our milling heads are equipped with modern spindle designs, advanced sealing systems, and heat-resistant components to extend tool life.Innovations like universal mounting compatibility, vibration-damping features, and improved oil-flow channels are designed to give our clients a competitive edge.Customization for Real-World ConditionsNo two shops are alike—and neither are their machines or workloads. That’s why Yih Kuan offers custom solutions tailored to your shop floor.Special tooling clearances? Unique cutting angles? We’ll build your milling head to match.Whether you're cutting hard steels or fine-tuning prototype molds, we ensure your head is ready for the job.Our design flexibility makes it easy to integrate with existing Bridgeport-style machines, whether you’re doing one-off pieces or light production runs.Built to Last: High-Quality ComponentsLongevity is critical when investing in upgrades. That’s why Yih Kuan prioritizes quality from the inside out.We use hardened steel, high-precision bearings, and CNC-machined housings to guarantee long-term durability.Our heads undergo rigorous inspection and performance testing before shipment, ensuring every unit performs reliably under load.Whether you run your knee mill eight hours a day or around the clock, our heads are designed to withstand it.Exceptional Customer SupportUpgrading machinery can be daunting—but with Yih Kuan, you’re not doing it alone.Our team provides complete technical support, including product selection, installation guidance, and after-sales service.Need help troubleshooting spindle vibration or alignment issues? Our responsive team is just a message away.We also offer instruction manuals, installation diagrams, and training resources to make sure your upgrade is smooth and efficient.Proven Results, Trusted WorldwideThousands of manufacturers—across Asia, Europe, and the Americas—have already chosen Yih Kuan to improve their knee mill performance.Many report 20–30% productivity improvements, especially in mold and die work, general repair machining, and small-part prototyping.Our products are recognized for stability, reliability, and consistent output, even under demanding cutting conditions.Don’t just take our word for it—our clients’ testimonials and long-term partnerships speak volumes.Built for the Future: Efficiency & SustainabilityModern machining isn’t just about precision—it’s about responsibility.Our milling heads are engineered with energy-efficient designs, reducing the strain on motors and drive systems.By extending machine life and reducing waste, we help our customers contribute to sustainable manufacturing practices.Less energy, fewer breakdowns, and longer tool life mean lower costs and a smaller carbon footprint.Conclusion: Upgrade with ConfidenceUpgrading your knee mill is more than just replacing a part—it's about unlocking new possibilities in precision, speed, and efficiency. With Yih Kuan, you’re not just investing in a component, but in a partnership that delivers long-term results.From R&D-driven design to rugged durability and expert support, Yih Kuan is the trusted name in turret milling head solutions. Let us help you modernize your knee mill—with performance you can measure and quality you can trust.Explore our vertical turret milling heads today:plist3-vertical-turret-milling-headContact our team for a custom consultation.
07. 09. 2025
more
Choosing the right milling head is a critical step in unlocking the full potential of your knee mill. Whether you're working in a mold and die shop, a maintenance department, or a small-volume prototyping facility, the correct milling head can dramatically improve machining accuracy, productivity, and equipment lifespan. With decades of hands-on experience and customer feedback, Yih Kuan Enterprise Co., Ltd. offers this practical guide to help you make the smartest investment in your machine shop.Key Factors to Consider1. Understand Your Machining NeedsStart by identifying the type of work your shop handles most often:Materials: Are you primarily machining steel, aluminum, cast iron, or non-ferrous metals like brass or copper? Harder materials may require higher torque and rigid construction.Precision Requirements: Fine finishing tasks require smooth spindle rotation and vibration control, while rough cuts may need torque over finesse.Special Functions: Do you need features such as angular milling (for sloped surfaces), deep cavity access, or multi-face machining?Tip: If your work often involves working at angles or on irregular surfaces, consider a milling head with tilt and swivel capability.2. Evaluate Milling Head FeaturesNot all milling heads are created equal. Pay attention to these critical specifications:Speed Range: Look for models that offer variable speed controls or step-pulley options. This allows for greater flexibility when switching between materials and cutting depths.Torque and Power: A powerful spindle motor is essential for heavy-duty tasks like deep slotting or pocketing hard metals.Machining Versatility: Choose a head capable of supporting milling, drilling, boring, slotting, and even tapping operations.Ease of Use: Controls for tilt, rotation, and spindle speed should be intuitive and ergonomic for daily operation.3. Ensure CompatibilityEven the best milling head is only effective if it fits your machine correctly.Mounting: Check your knee mill’s mounting flange and interface dimensions. Yih Kuan’s turret milling heads are designed to be compatible with most Bridgeport-style machines.Machine Balance: A heavier milling head may require reinforcement to the column or table to ensure stability.Electrical Requirements: Verify motor voltage and drive system compatibility with your current setup.4. Focus on Quality and DurabilityMilling heads endure high rotational speeds, intense pressure, and long operating hours. Make durability a priority:Materials: Look for heads made from hardened steel or castings with anti-corrosion treatment.Internal Components: High-quality spindle bearings, precision-ground gears, and sealed lubrication systems will ensure longer life and consistent performance.Thermal Resistance: Heat-treated and balanced spindles minimize warping during long or aggressive machining cycles.5. Explore Advanced TechnologiesModern manufacturing demands smarter solutions:Vibration Dampening: Heads with built-in dampening systems reduce chatter and improve surface finish.Programmable Adjustments: CNC-compatible heads with programmable angles or RPM controls enhance repeatability.Cooling Systems: Whether through forced air or internal coolant flow, cooling improves both accuracy and component longevity.6. Seek Expert AdviceBuying a milling head isn’t a one-size-fits-all decision:Consult Experts: Yih Kuan’s experienced team can help analyze your production environment and recommend the optimal solution.Request Demonstrations: If possible, test the head on your own machine to evaluate noise, vibration, and tool compatibility.Read Case Studies: See how other machine shops in similar industries have benefited from the right milling head upgrade.Additional Tips for Maintenance and LongevityRegularly inspect the milling head for wear and tear, especially after heavy use.Keep the milling head clean and properly lubricated to prevent rust and ensure smooth operation.Replace worn-out parts promptly to maintain the accuracy and efficiency of your milling head.Follow the manufacturer’s guidelines for installation, operation, and maintenance.Why Choose Yih Kuan?With a long-standing reputation for reliability and technical excellence, Yih Kuan offers more than just a product—we provide a long-term solution for your machining needs.Extensive Product Range: From vertical turret heads to angular milling heads and specialized solutions.Tailored Configurations: Customizable spindle types, mounting dimensions, and RPM ranges.Proven Quality: Manufactured using premium-grade materials, precision-machined components, and strict quality control protocols.Exceptional Service: We partner with our clients before, during, and after installation to ensure continued satisfaction and optimal performance.ConclusionYour knee mill is only as effective as the milling head it carries. Whether you need greater precision, more torque, or flexible angle adjustments, choosing the right head is an investment in productivity, quality, and profitability.With Yih Kuan’s decades of experience, high-quality milling heads, and expert support, you can upgrade with confidence. Let us help you transform your machine’s performance—and your bottom line.Explore our turret milling heads and contact us today for a consultation:plist3-vertical-turret-milling-head
06. 19. 2025
more
YIH KUAN ENTERPRISE will be participating in the Vietnam Industrial & Manufacturing Fair (VIMF 2025). We sincerely invite you to visit us and explore our expertise in modular milling head solutions.
At the exhibition, we will provide complete product catalogs and have technical staff on-site to explain milling head applications, model selection, and machine retrofit options—helping you optimize your machining process and enhance production efficiency.
Exhibition Dates: June 18 (Wednesday) – June 20 (Friday), 2025
Venue: WTC Expo, Binh Duong (World Trade Center Binh Duong New City)
Booth Number: 584
06. 17. 2025
more
Old Machines Can Still Be Saved!-Expert Solutions for Every Milling Head — No Matter the Brand!In the machining world, nothing is more frustrating than equipment failure—especially when it's an older turret or plano milling machine. When the original manufacturer has stopped production and spare parts are no longer available, does that mean you need to replace the whole machine?Not necessarily—most of the time, the problem lies in the milling head!Common Failure Symptoms:Significant loss of machining accuracySpindle runout, overheating, or unusual noiseWeak clamping or tool changes not working smoothlyOil seal leakage, unstable spindle speedExcessive vibration during cutting, high scrap rateIn many cases, the root cause is an aging or damaged milling head. Simply replacing it with the right new head can restore your machine and get you back to production!IK's Custom Milling Head Replacement Service:Compatible with All Machines, Regardless of Brand!Whether your machine is made in Taiwan or abroad—turret or plano type—as long as the milling head is the issue, YIH KUAN can provide a solution!Common Taiwanese Brands (Brand / Manufacturer):YCM (Yung Chin Machinery)KENT (KENT Industrial)TOPONE (HSU CHENG Machinery)CHIEN CHENG (CHIEN CHENG Machinery)TOP WELL (TONG WEI Machinery)FIRST (LONG CHANG Machinery)FEMCO (Far East Machinery)ING SUN (ING SUN Machinery)SONYU (SONYU Machinery)MAXIMART (MAXIN Machinery)JYIH SHYANG (JYIH SHYANG Machinery)International Brands:Bridgeport (USA), Sharp, Acra, Comet, JET, Chevalier… and other classic American and European models.Not on the list? No problem!If you can provide milling head dimensions, mounting interfaces, photos, or machine condition, YIH KUAN will design a custom-fit modular head for you.From measurement, flange matching, spindle configuration to performance upgrades—we offer a complete solution!Why Choose YIH KUAN?Specialized in modular milling head production, with standard, heavy-duty, and NC-upgrade typesSupports custom flange design, spindle specs, motor interfacesOffers angle heads, plano heads, and CNC gear-driven headsHelps upgrade old machines with air/oil drawbars, inverter motors, and auto lubrication systemsContact Us Today!No matter the brand or age of your machine—if the milling head is the issue, trust YIH KUAN!We'll help you assess, upgrade, and extend the life of your equipment with expert support.Contact us with drawings or photos for a free evaluation.
06. 09. 2025
more
YIH KUAN ENTERPRISE is pleased to announce our participation in InterPlas Thailand 2025, where we will be co-exhibiting with Flying Tiger KJ Co., Ltd. This event is one of Southeast Asia’s most influential trade shows for the plastics and rubber manufacturing industries, bringing together key players and decision-makers from across the region.Exhibition Venue: BITEC – Bangkok International Trade & Exhibition Centre, ThailandExhibition Dates: June 18–21, 2025Opening Hours: 10:00 AM – 6:00 PMBooth Number: 2D35During the exhibition, we will showcase our latest modular milling head solutions, designed to address real-world machining challenges and support efficient equipment upgrades — without requiring full machine replacement. Our experienced team will be available at the booth to provide technical consultations and share insights on how YIH KUAN’s products can support your production needs.What to Expect at Our Booth:Practical solutions for machine retrofittingCustomizable milling head designs for special applicationsProfessional guidance on-siteWe sincerely invite our partners, customers, and industry professionals to visit us at Booth 2D35 to explore collaboration opportunities and learn more about our innovative solutions.For more information about InterPlas Thailand 2025, please visit the official event website: https://www.interplasthailand.com
06. 04. 2025
more
In the manufacturing industry, milling machines are indispensable tools for precision machining. However, as production needs evolve and equipment ages, many users face ongoing challenges that lead them to consider upgrading or replacing their milling machines or heads. Below are the ten most common issues encountered by milling machine users:1. Insufficient Machining Accuracy Affects Product QualityOver time, a milling machine’s precision deteriorates, making it harder to meet increasingly strict tolerance requirements.2. Poor Head Stability Causes Vibration IssuesAn unstable milling head under high load or complex machining leads to vibrations, affecting surface quality and shortening tool life.3. Equipment Aging and Component WearWorn-out mechanical parts cause performance degradation, reduced efficiency, and increased defects in machining.4. Unable to Meet Modern Machining DemandsTraditional milling machines often fail to support multi-angle or high-speed operations, limiting flexibility in product offerings and order fulfillment.5. Low Production EfficiencyOlder machines operate slowly and require frequent manual adjustments, hampering productivity and workflow.6. Incompatibility with CNC or Automation UpgradesSome machines or head designs lack the structure to integrate CNC controls or automation, restricting smart manufacturing possibilities.7. High Maintenance Costs and Frequent DowntimeFrequent breakdowns, costly repairs, and hard-to-source parts lead to longer downtimes and increased operating expenses.8. Machine Layout Limits Workspace OptimizationBulky or poorly designed machines hinder flexible factory layouts and reduce usable floor space.9. Unstable Cutting Quality Increases Post-Processing BurdenRough or uneven surfaces require additional finishing, wasting time and labor resources.10. Excessive Noise and Poor Operator ComfortOlder machines produce high levels of noise, affecting the working environment and operator well-being.The Solution: Modular & Customizable Milling Head Upgrades by ProfessionalsTo address these pain points, YIH KUAN ENT. CO., LTD. offers a comprehensive and flexible range of milling head solutions. Users can enhance machining performance and competitiveness without the need to replace the entire machine.Our core products include:Turret Milling HeadsPlano (Gantry) Milling HeadsAngle Milling HeadsCNC Gear HeadsAll of our products are built with a modular design, allowing users to mix and match configurations based on their needs. This provides flexibility and cost control while keeping up with market demands.Need something customized? YIH KUAN can tailor solutions according to your specifications. From interface dimensions to special functions, our team will work with your drawings and requirements.As a professional milling head manufacturer, YIH KUAN offers end-to-end capabilities—from development and manufacturing to testing and after-sales service. We deliver custom-level flexibility at mass production prices, offering both stability and high cost-efficiency.ConclusionUpgrading your milling machine or head isn’t just about replacing equipment—it's about rebuilding your competitive edge. Choosing the right milling head partner can help you achieve greater accuracy, faster throughput, and reduced downtime.#Contact YIH KUAN today to explore the best upgrade solution for your machinery and your business.
05. 22. 2025
more
YIH KUAN, Precision Manufacturer of Traditional Milling Heads from TaiwanStruggling with unstable spindle speed, vibration, or noisy old milling heads?Don't let outdated equipment slow down your production. YIH KUAN INDUSTRIAL CO., LTD., with over 50 years of precision machining expertise in Taiwan, specializes in high-quality milling heads, angle heads, and customized spindle units — empowering your existing machines with enhanced efficiency and extended service life.Why Choose YIH KUAN Milling Heads?High-Rigidity Structure – Ensures smooth and stable cutting performancePrecision Spindles with Imported Bearings – Quiet operation and long lifespanCompatible with Multiple Milling Machines – Supports common mounting configurationsEasy Maintenance, Full Spare Parts Availability – Fast servicing, no downtime Made in Taiwan, Trusted Worldwide – Exported to 5 continents, quality you can rely on #MultipleOptions #FlexibleSupply #QuickInstallation #ConsultativeSupportWhen Tariffs Rise, A Smarter Upgrade MattersAs global trade policies tighten and complete machine imports face rising tariffs,upgrading your existing equipment is the smarter, more cost-effective choice.Replacing your milling head is like giving your machine a powerful, stable new core —it extends machine life, improves precision, and reduces overall operating costs.YIH KUAN offers global customers flexible and responsive solutions:Flexible quotation options (FOB / CIF / EXW etc.)Small batch supply, volume partnership, or OEM customizationSupport for regional distributors and system integratorsFast shipping & consistent technical support from our expert teamIdeal for:Daily machine maintenance or upgrades at factoriesRetrofit and rebuild specialistsTechnical schools and training centersTool machine OEMs and automation integratorsWhether you're looking for a standard vertical milling head, an angle head solution,or a customized head for special cutting environments,YIH KUAN is your trusted manufacturing partner.Upgrade Your Equipment Today!Simply send us a photo and basic dimensions of your current milling head.Our team will quickly help you identify the ideal replacement model — easy to install and operate.Contact Us|+886-4-2491-4376Email|yihkuan.salesperson@gmail.comWebsite|www.yihkuan.comMade in Taiwan ・ Globally Trusted ・ Professionally Supported#MillingHead #AngleHead #CustomApplications #MachineToolComponents #SmartUpgrade #CostSaving #YIHKUAN #TaiwanMade #PrecisionEngineeringPartner
05. 12. 2025
more
IntroductionIn the mold and die industry, precision, repeatability, and efficiency are not just goals—they're requirements. As demand increases for tighter tolerances and faster lead times, many manufacturers are asking: Is it time to upgrade the milling heads on our existing Bridgeport machines? For those still operating with aging equipment or using standard heads that no longer meet production expectations, upgrading to a modern Bridgeport milling head could be a game-changer.This article explores the key reasons why the mold and die industry should consider upgrading and how a high-quality Bridgeport milling head can bring measurable improvements to your machining operations.________________________________________Enhanced Precision for Complex Mold GeometryModern mold designs often involve complex contours, deep cavities, and multi-angle features. The accuracy of these features heavily relies on the stability and performance of the milling head.Upgrading your Bridgeport milling head gives you:Improved spindle rigidity and reduced vibrationGreater machining precision, especially during fine finishingBetter surface finish for tight-tolerance mold componentsThis precision is essential when producing cores, cavities, sliders, and other mold components where every micron counts.________________________________________Faster Setup and Greater Machining EfficiencyOlder or worn milling heads can slow down your process with inconsistent performance or frequent manual adjustments. A new Bridgeport milling head provides smoother operation and quicker setup changes.Benefits include:Reduced downtime from mechanical issuesImproved feed rate stability during contouring or slottingCompatibility with modern tooling and digital readout (DRO) systemsFor mold manufacturers with tight delivery schedules, this translates directly into higher throughput and fewer delays.________________________________________Cost Savings Without Replacing the Entire MachineMany mold shops still use their trusted Bridgeport machines because of their solid construction and long lifespan. Instead of investing in an entirely new CNC mill, replacing just the milling head can provide a significant performance boost at a fraction of the cost.Why this matters:Extends the life of your existing machineAvoids retraining operators or reconfiguring the shop layoutProvides immediate ROI through faster, more accurate machiningThis is a smart option for small to medium-sized mold makers looking to stay competitive without overspending.________________________________________Versatility for Custom Modifications and RepairsMold manufacturing often requires last-minute adjustments or design tweaks. A Bridgeport milling machine equipped with a high-performance turret head offers the flexibility to make precise modifications on the fly—whether it's trimming edges, adding features, or repairing damaged areas.Perfect for:Short-run custom moldsEmergency toolroom workIn-house mold maintenance________________________________________Why Yih Kuan Bridgeport Milling Heads?At Yih Kuan Enterprise Co., Ltd., we specialize in high-performance turret milling heads compatible with Bridgeport-style machines. Our milling heads come in R8, NT30, and NT40 spindle options to suit various machining needs.Our advantages:Stable construction and superior alignment accuracyDesigned for mold & die applicationsReliable support and easy integration with existing machines________________________________________ConclusionFor the mold and die industry, upgrading to a new Bridgeport milling head isn't just an improvement—it's a smart investment. Whether you're machining complex geometries or simply trying to meet production deadlines more efficiently, a high-quality milling head can help you maintain precision, increase productivity, and reduce costs.Call to ActionReady to upgrade? Explore our selection of Bridgeport-compatible milling heads at Yih Kuan's product page, or contact us today for expert advice tailored to the mold & die industry.
05. 06. 2025
more
§ [From Trade Show Visit to Supply Chain Insight]2025 Taipei AMPA × YIH KUAN Observations ReportThe 2025 Taipei International Auto Parts & Accessories Show (AMPA) kicked off in full swing, as lively and diverse as ever. From headlights, suspensions, and calipers to modified kits, inspection equipment, and precision hand tools, the exhibition floor was buzzing with innovation. Each exhibitor pulled out all the stops to showcase their capabilities and their role in the automotive supply chain.But amidst the dazzling displays, our team from YIH KUAN ENT. CO., LTD., attending as visitors, found something far more revealing — a deeper layer of insight into the real challenges facing manufacturers today.On-Site Conversations That Unveiled Real Processing ChallengesDuring a casual yet in-depth conversation with one auto parts manufacturer, we discovered they were facing serious difficulties in processing certain automotive components. The key components they had been sourcing externally — originally intended to improve machining precision and efficiency — were instead creating new problems: Assembly misalignment leading to high scrap rates Tool runout affecting finished product accuracy Incompatible specifications reducing overall efficiency...What seemed at first to be a quality issue with individual parts actually reflected a much larger problem across the machining supply chain — a lack of system-level thinking and compatibility integration.YIH KUAN’s Reflection: What Kind of Support Do Machining Shops Truly Need?As a professional manufacturer of milling heads, YIH KUAN understands that a milling head is not just a component — it's the driving core of an entire machining system. We believe that for manufacturers facing such bottlenecks, the solution isn’t simply a product, but a tailored system upgrade delivered through consultative support.That’s why we’re actively implementing strategic solutions like: Modular Milling Head Upgrades – Replace outdated parts with modular solutions for greater compatibility and performance‧ On-Site Machining Assessment – Identify pain points and offer customized suggestions and parameter recommendations. Tooling & Interface Integration – Help streamline systems by ensuring all components work seamlessly together.From Observing a Show to Understanding an IndustryThis visit to AMPA reminded us that a trade show is more than a product showcase — it's a mirror reflecting the true needs of the industry. While many booths promoted innovation and automation, there remains a segment of the industry still struggling with the basics: machining stability and operational efficiency.At YIH KUAN, we believe that strengthening these foundational capabilities is essential for long-term competitiveness in Taiwan’s automotive supply chain.Final Thoughts | A Shift in the Role of Machine Tool Makers: From Passive Suppliers to Active EnablersThis AMPA 2025 visit confirmed our belief that our role should go beyond simply quoting specs — we must proactively understand the market, step into the factory, and become a trusted partner to our clients.The future of the auto parts industry will not only be built on cutting-edge products, but also on reliable, scalable, and adaptable manufacturing foundations.And that’s where YIH KUAN is ready to play a key role.
04. 25. 2025
more
The Hidden Link Between Machine Tools and the Food IndustryBy: Columnist – Mechanical Industry ObserverWhen people talk about the machine tool industry, they usually associate it with automotive components, mold manufacturing, or aerospace. On the other hand, the food industry brings to mind bread makers, sealing machines, packaging lines, or automatic filling equipment. These two sectors may seem worlds apart—but in reality, they are tightly connected behind the scenes.In a recent conversation between Yih Kuan Enterprise Co., Ltd., a professional milling head manufacturer in Taiwan, and a prominent figure in the food industry, the close relationship between machine tools and food processing machinery became crystal clear.Machine Tools: The “Mothers” of Food MachineryFood machinery—such as automated filling machines, film sealing systems, conveyor lines, and food molds—are largely composed of metal components. Before these parts can be assembled into functional machines, they must first be precisely machined—through turning, milling, drilling, and tapping—core processes performed by machine tools.In other words, every part of a food machine, from its frame and structure to critical components like shafts and molds, relies on machine tools for precision manufacturing. No machine tool, no food machine.Milling Head Technology: The Heart of Machining EfficiencyYih Kuan specializes in milling heads, including turret milling heads, plano milling heads, and angle heads. These units are the core cutting elements of milling machines. Milling heads directly affect the surface precision and productivity of machined parts, and they greatly enhance the flexibility of machining operations—making complex components possible.For the food industry, rising expectations in hygiene, safety, and customized production have made food equipment increasingly complex and refined. This trend drives machine tool innovation, creating a mutually beneficial cycle between the two industries.Automation Fuels Cross-Industry IntegrationToday's food factories are shifting toward automation and smart production—from raw material handling and filling to packaging and logistics. These systems require high-precision components and robust structural designs, all of which are enabled by machine tools and components like milling heads.In this era of integration, companies like Yih Kuan Enterprise, which focus on high-performance machine tool components, play a pivotal role in bridging traditional machining with emerging industrial needs.Conclusion: Unlocking New Possibilities Through Cross-Industry CollaborationThough the food and machine tool industries may seem unrelated at first glance, they are, in fact, mutually dependent. From the precision machining of food molds to the structural frames of automated machines, machine tools are the silent foundation behind the scenes. For Yih Kuan Enterprise, this represents not only a market expansion opportunity but also a chance to foster collaboration between industries.As food processing evolves toward greater automation, modularity, and stricter hygiene standards, the machine tool industry will advance in parallel—working together to usher in a new era of smart manufacturing.
04. 14. 2025
more
Understanding the Importance of Milling Head SelectionIn the world of precision machining, selecting the right milling head is crucial for achieving optimal performance, efficiency, and machining accuracy. However, many users simply adopt the standard milling head provided by the machine manufacturer without considering whether it truly meets their specific machining requirements. This often limits the machine’s full capabilities, preventing businesses from maximizing their production potential.Recently, Yih Kuan (IK Milling Head) received an inquiry from a customer who owns a Japanese milling machine and wanted to replace its milling head. The customer asked:"Is it possible to change the milling head on my machine?"After reviewing the provided photo, Yih Kuan responded with expert guidance:"Yes, it’s definitely possible! However, it is important to confirm certain dimensions, technical requirements, and machining characteristics to ensure a proper fit and seamless integration."This inquiry highlights a common industry challenge—many manufacturers may not realize that milling head replacement and customization can dramatically enhance their machining capabilities, improve precision, and expand production flexibility.The Role of Milling Heads in Machining PerformanceA milling head is the core component of a milling machine, responsible for performing precise cutting, drilling, and shaping operations. It directly impacts factors such as:Machining accuracy – A high-quality milling head ensures precision in every cut.Production efficiency – The right milling head can reduce machining time and improve workflow.Versatility – Different milling heads offer unique capabilities suited for various machining applications.Longevity – Upgrading to a well-designed, high-rigidity milling head extends the lifespan of the entire machine.By choosing the correct milling head, manufacturers can unlock the true potential of their equipment, enabling them to handle more complex machining tasks and increase overall productivity.Comprehensive Milling Head Solutions by Yih KuanWith decades of expertise in milling head manufacturing, Yih Kuan (IK Milling Head) specializes in producing a wide range of high-performance milling heads, including:CNC Gantry Gear Heads – Designed for high-torque, heavy-duty machining applications, ensuring precise and stable performance.Machining Center Gear Heads – Engineered for high-speed CNC milling centers, optimizing productivity and machining efficiency.Plano Milling Heads – Perfect for large-scale surface milling, providing rigid support and accuracy for various industries.Turret Milling Heads – Ideal for general machining, offering flexibility for manual and CNC-controlled milling operations.Angular Heads – Expand machining capabilities by allowing multi-directional cutting without repositioning the workpiece.Beyond standard models, Yih Kuan also offers customized milling head solutions, tailoring configurations to match unique customer requirements. This ensures seamless integration with existing milling machines, enhancing machining efficiency and versatility.Key Considerations for Milling Head ReplacementBefore upgrading or replacing a milling head, it is essential to assess key factors such as:Spindle interface compatibility – Ensuring the new milling head matches the machine’s spindle mounting specifications.Required machining capabilities – Considering factors like cutting speed, torque, and rigidity needed for specific applications.Machine capacity and structural support – Verifying whether the existing machine structure can handle a more powerful milling head.Automation and CNC integration – Determining if the new milling head is compatible with CNC control systems for precision automation.Proper evaluation of these aspects will ensure a smooth transition and maximize the performance benefits of a new milling head.Unlock Your Machine’s Full Potential with Yih Kuan (IK Milling Head)At Yih Kuan, we understand that every machining requirement is unique. Whether you need a high-precision CNC milling head, a durable plano milling head, or a specialized angular head, our expert team can help you find or customize the perfect solution.Why settle for standard when you can optimize?Enhance your machining capabilities with a tailored milling head upgrade!For professional milling head solutions, contact Yih Kuan (IK Milling Head) today and explore how our expertise can elevate your machining performance to new levels
04. 14. 2025
more
March 12, 2025, 11:07:28Economic Daily – Xu YuqingThe Taipei International Machine Tool Show (TIMTOS) recently attracted professional buyers from over 90 countries worldwide. Yih Kuan Enterprise (IK), one of the exhibitors, promoted its mission of “Rescuing Mechanical Orphans”, showcasing high-quality milling heads and angle heads. This concept resonated with the industry. With the proactive efforts of the company’s second-generation leader and current Executive Vice President, Hung Yang-Chia, the booth attracted a steady stream of visitors, including curious buyers from over 20 countries, including Europe, the U.S., Japan, and India.Upgrading Machinery for Sustainable ProductionIn recent years, trends such as ESG (Environmental, Social, and Corporate Governance) and net-zero carbon emissions have prompted many factories to face the challenge of equipment replacement and idle machinery. Hung Yang-Chia stated that as a trusted partner for global machine tool manufacturers, Yih Kuan is committed to providing comprehensive milling head and angle head solutions to ensure stable machine performance and improved machining precision, allowing customers to maintain uninterrupted production.Many machines in client facilities have been in service for decades. Although machining conditions are limited and precision has declined, these machines still hold production value."Many people assume that these machines are ‘outdated’ or ‘useless,’ leading to a large number of machines being left idle or even scrapped outright," Hung Yang-Chia said.Old Machines Are Not Scrap Metal – Unlock Their Value Through Upgrades"Old machines are not scrap! With the right upgrades, they can still create value, return to production, and generate greater benefits." Hung Yang-Chia actively promotes this concept through both physical exhibitions and online platforms, advocating for an equipment revitalization plan that breathes new life into old machines.To address outdated equipment issues, Yih Kuan offers solutions to restart and upgrade milling heads, ensuring older machines regain functionality through:Enhanced Machining Precision – High-rigidity, high-stability milling heads improve machining accuracy to meet modern production requirements.Expanded Machining Applications – Angle heads and other multifunctional accessories allow old equipment to handle more machining tasks, increasing production flexibility.Reduced Replacement Costs – Avoid unnecessary full-machine replacements, reduce capital expenditures, and align with environmental and carbon reduction goals.Yih Kuan’s solutions, aimed at “Upgrading Old Machines for Sustainable Production,” have garnered significant interest from both existing customers and potential new clients worldwide.Beyond standard products, Yih Kuan also offers customized retrofit services, tailoring upgrade plans based on the specific needs of different industries. This ensures that old and even idle machines can be revitalized and reintegrated into production lines, unlocking greater value.
03. 13. 2025
more
With the widespread adoption of CNC machines such as turn-mill centers, five-axis machines, and fully automated milling machines, automated angle heads have become a key component in modern machining. However, despite these advancements, manual angle heads continue to be in high demand. This phenomenon is driven by several crucial factors that make manual angle heads indispensable in various industries.Why is There Still a Demand for Manual Angle Heads?1. Cost ConsiderationsWhile automated angle heads improve efficiency, their high cost makes them less accessible to small and medium-sized enterprises (SMEs). Many manufacturers opt for more affordable manual angle heads to maintain production flexibility without significant investment.2. Flexibility and VersatilityManual angle heads are compatible with various machines, including traditional milling machines, gantry mills, and horizontal machining centers. They provide greater flexibility when machining non-standard parts, allowing operators to make quick adjustments without the need for complex programming.3. Maintenance and On-Site MachiningIndustries such as shipbuilding, aerospace, and energy equipment maintenance often require on-site machining. Since manual angle heads do not require additional control systems, they offer an easy-to-use and effective solution for repair and maintenance operations.4. Specialized ApplicationsSome industries, such as mold manufacturing, custom product machining, and technical training, still rely heavily on manual angle heads. Operators in these fields require precise control over machining angles, making manual adjustments a preferred choice.Which Markets Have the Highest Demand for Manual Angle Heads?1. Southeast Asia MarketMany SMEs in countries such as Vietnam, Thailand, and Indonesia still use conventional milling machines, creating consistent demand for manual angle heads.The mold manufacturing and machining industries in this region continue to rely on manual machining solutions.2. Indian MarketIndia has a significant number of traditional machines in operation, and cost-sensitive businesses prefer manual angle heads over expensive automated alternatives.The demand for flexible machining solutions in small-scale industries contributes to steady sales of manual angle heads.3. Latin American MarketCountries like Brazil and Mexico have large manufacturing industries but slower adoption of automated equipment, maintaining a need for manual angle heads.Many factories require manual solutions for maintenance and prototyping purposes.4. European Market (Selective Regions)While Western Europe leads in automation, Eastern Europe and small-scale mold factories still utilize manual angle heads for high-precision, low-volume machining.Taiwan’s Position in the Global MarketTaiwan plays a critical role in the global supply of manual angle heads due to its strong precision manufacturing industry. Taiwanese manufacturers are known for:Stable Quality: Taiwan-made angle heads are recognized for their high precision and durability, providing a competitive edge over lower-cost alternatives from China while being more affordable than European brands.Customization and Flexibility: Taiwanese manufacturers, such as Yi Kuan Enterprise Co., Ltd., offer a broad selection of milling heads to cater to various machining needs, including standard and customized options.Strategic Market Influence: Taiwan is a leading supplier of machine tool accessories in Asia, particularly serving Southeast Asia and India with high-quality yet cost-effective products.Yih Kuan Enterprise Co., Ltd. specializes in manufacturing milling heads and provides a wide range of options to meet diverse industrial requirements. Their product offerings ensure that milling machine users can select, upgrade, and modify their setups with confidence, achieving seamless and reliable machining operations.ConclusionDespite the increasing automation in the machine tool industry, manual angle heads remain crucial due to their cost-effectiveness, flexibility, and adaptability in various industries. By selecting the right manual angle head and leveraging customized solutions, manufacturers can enhance their machining capabilities. Taiwan continues to be a strong player in this market, with companies like Yih Kuan Enterprise Co., Ltd. providing top-quality milling heads to meet global demands.
02. 24. 2025
more
Although conventional milling machines have gradually been replaced by CNC (Computer Numerical Control) equipment in modern factories, their flexibility, low cost, and adaptability still secure them a crucial place in various manufacturing environments. Especially in small-batch production, maintenance work, and machining skill training, the value of conventional milling machines remains indispensable.◎Applications of Conventional Milling MachinesPrototype Development and Small-Batch ProductionConventional milling machines are ideal for developing new product prototypes as they allow for quick adjustments and modifications without the need for programming or complex machine setups. For small-scale production, their intuitive operation helps shorten production cycles.Prototyping, Maintenance, and Custom Parts MachiningMany factories still rely on conventional milling machines for prototyping and maintenance work, especially in the upkeep of large machinery or specialized components. By upgrading components and applying jigs and fixtures, conventional milling machines can be adjusted to meet specific needs, enhancing production efficiency.Technical Training and LearningConventional milling machines are essential tools for technical schools and in-house factory training. Learners can manually operate the machines to understand machining principles, develop fundamental metal-cutting skills, and build a solid foundation for advancing to CNC machining.Yih Kuan Enterprise Co., Ltd. provides a wide range of milling heads tailored to different motor specifications, transmission methods, machining strokes, and specialized milling head requirements. Through consultative services, we help users identify their precise milling machine needs and match them with the most suitable milling head modifications.#GantryMillingHead#TurretMillingHead#AngleMillingHeadSelecting the Right Milling Head to Enhance Machining CapabilityOne of the core components of a conventional milling machine is the milling head, which significantly affects machining precision, efficiency, and application range. Choosing the right milling head can improve cutting performance and reduce machining errors. For instance, if a factory frequently processes harder materials, selecting a high-rigidity milling head ensures stable cutting performance. Additionally, for multi-angle machining requirements, an adjustable milling head can enhance flexibility.Upgrading the Milling Head to Improve Production EfficiencyMany factories upgrade their milling heads to enhance the performance of conventional milling machines. Upgrades include installing high-speed milling heads to increase cutting speed or adding automatic feed functions to reduce operator workload. For high-precision machining needs, opting for precision-grade milling heads can significantly improve machining accuracy.ConclusionAlthough automation and CNC machines are becoming mainstream, conventional milling machines remain irreplaceable in factories. Whether for small-batch machining, prototyping, maintenance, or technical training, they play a vital role. By selecting the right milling head, upgrading milling heads, and utilizing customized milling machine components, companies can further enhance machining efficiency, ensuring that this traditional equipment continues to provide value in modern manufacturing.
02. 17. 2025
more
IntroductionVertical Machining Centers (VMCs) are a cornerstone in modern manufacturing environments, known for their efficiency and precision. To further leverage the capabilities of these versatile machines, adding an angular head can transform operations, broadening the scope of projects a VMC can handle. Here's a deeper look into why installing an angular head in your VMC setup is essential for enhancing machining flexibility.1. Increased Range of Machining AnglesDetailed Explanation: Angular heads provide VMCs with the capability to execute machining operations at angles other than the typical vertical orientation. This flexibility is critical when producing parts that have complex geometries, as it allows for the machining of bevels, chamfers, and deep pockets that would otherwise be inaccessible.Practical Impact: Incorporating an angular head minimizes the need for manual repositioning of the workpiece, which can be time-consuming and prone to errors. As a result, manufacturers can expect more precise outcomes with smoother workflows, contributing to overall increases in productivity and reductions in cycle times.2. Enhanced Complex MachiningDetailed Explanation: Angular heads unlock new machining possibilities by allowing VMCs to reach difficult areas of a part with ease. They make it possible to mill, drill, and tap from different angles, which is invaluable for creating intricate features on parts without multiple machine setups.Practical Impact: This enhanced capability is especially valuable in sectors that manufacture complex assemblies, such as aerospace, automotive, and die/mold making. The ability to adhere to strict tolerances and produce complex designs with high repeatability ensures that products meet rigorous industry standards.3. Optimized Tool Utilization• Detailed Explanation: By changing the orientation of the cutting tool, angular heads can significantly extend the range of operations each tool can perform. This adaptability reduces the need for a large variety of specialized tools, which can be expensive and require additional storage and management.• Practical Impact: Better tool utilization leads to cost efficiencies in tooling expenditure. Reducing the number of tool changes also decreases machine downtime and enhances throughput, making the manufacturing process more efficient and less costly.ConclusionAdding an angular head to your VMC is a strategic decision that enhances the machine’s flexibility, expands its machining capabilities, and optimizes the utilization of tooling resources. The adoption of such advanced technology ensures that your manufacturing setup remains competitive, agile, and capable of meeting the evolving demands of modern industries. If you are considering upgrading your VMCs, Yih Kuan's range of angular heads offers the reliability and performance needed to maximize your machining efficiency.Call to ActionExplore the full potential of your VMC with Yih Kuan's innovative angular heads. Visit our website or contact our expert team today to discover how we can help you transform your production capabilities and stay ahead in the competitive manufacturing landscape.
01. 16. 2025
more
The gantry milling head is an indispensable key component in modern machining, particularly suitable for high-precision machining and heavy-duty cutting of large workpieces. This article explores its applications in various machining scenarios, delves into its characteristics, highlights its significance in manufacturing processes, and introduces the professional services provided by Yih Kuan.1. Applications of Gantry Milling Heads in Various Machining ScenariosPrecision Machining and Heavy-Duty Cutting of Large Workpieces The gantry milling head, with its high rigidity and stability, is particularly well-suited for high-load cutting requirements of large workpieces. Whether for aerospace structures, energy equipment components, or mold machining, it excels in delivering consistent and efficient results.High-Precision Machining of Complex Geometries The gantry milling head can flexibly handle various complex shapes and freeform surfaces. Its multi-angle adjustment capability and precise cutting characteristics make it an essential piece of equipment in industries such as automotive, machinery manufacturing, and mold making. Additionally, the gantry milling machine can be equipped with angle heads to enhance flexibility, enabling seamless multi-angle and multi-directional machining.Intelligent and Automated Machining With the development of smart manufacturing technologies, gantry milling heads have become core components of automated production lines. Through tight integration with CNC systems, they enhance efficiency while ensuring machining precision, meeting the needs of diverse batch production.2. Key Features of Gantry Milling HeadsHigh Rigidity and Stability The structural design of the gantry milling head undergoes rigorous mechanical analysis and optimization, ensuring exceptional rigidity and stability. It maintains reliability during heavy cutting, achieving high material removal rates efficiently.Outstanding Machining Precision Equipped with high-precision spindles and CNC systems, gantry milling heads can execute machining tasks within micron-level tolerances, ensuring superior surface finishes and dimensional accuracy.Flexibility and Multi-Functionality Gantry milling heads are compatible with a wide range of tools and accessories, adapting to various machining needs. Whether for milling, drilling, or tapping operations, they excel in delivering efficiency and versatility. Furthermore, using angle heads expands capabilities beyond traditional limitations, achieving diversified process requirements.3. Professional Services Provided by Yih KuanYih Kuan specializes in the development and manufacturing of high-quality gantry milling heads, committed to offering customized solutions for clients:Custom Product Design: Tailor-made gantry milling heads are designed and manufactured based on client requirements to address diverse industrial machining challenges.Technical Support: Comprehensive technical assistance and training services ensure clients can fully leverage the performance of their equipment.After-Sales Services: A responsive after-sales service team provides equipment maintenance and upgrade solutions to ensure production stability and efficiency.Equipment Rebuilding Services: For aging gantry milling machines, Yih Kuan offers professional equipment rebuilding services, including head replacement, revitalizing old equipment to restore or even surpass original performance levels and extend service life.Yih Kuan upholds a commitment to professionalism and innovation, striving to help clients enhance production efficiency and competitiveness. If you have any inquiries or requirements regarding gantry milling heads, feel free to contact us!Contact Information:Phone: 886-4-24914376Email: yihkuan.salesperson@gmail.com
01. 07. 2025
more
IntroductionKnee mills, known for their versatility and precision in a variety of machining applications, remain a staple in workshops and manufacturing facilities. While inherently flexible, the performance of knee mills can be significantly enhanced by upgrading with high-quality milling heads. Yih Kuan's vertical turret milling heads, available in R8, NT30, and NT40 spindle options, offer superior performance and adaptability. This article explores how integrating these advanced milling heads can transform the capabilities of knee mills.Understanding Knee MillsKnee mills, characterized by a vertically adjustable table, or "knee," offer exceptional control and flexibility for machining complex parts. They are favored for their ability to perform intricate milling, drilling, and cutting tasks with high precision.The Role of Upgraded Milling HeadsUpgrading a knee mill with a sophisticated milling head from Yih Kuan enhances its operational capabilities:Precision and Versatility: Yih Kuan’s milling heads provide precision machining with their advanced design and robust construction, making them ideal for tackling complex machining tasks that require meticulous detail.Compatibility and Performance: With spindle options like R8, NT30, and NT40, Yih Kuan’s milling heads are compatible with a wide range of knee mills, ensuring that regardless of the original equipment, enhanced performance is achievable.Key Benefits of UpgradingEnhanced Durability and Reliability: Upgrading to Yih Kuan’s milling heads not only enhances performance but also improves the overall durability and reliability of the milling equipment. High-quality materials and precision engineering reduce wear and tear, extending the lifespan of both the milling head and the knee mill itself.Increased Range of Tool Compatibility: With advanced milling heads like those offered by Yih Kuan, knee mills can utilize a wider range of cutting tools, including specialized ones designed for specific materials or applications. This compatibility broadens the scope of projects that can be handled, accommodating everything from standard milling operations to specialized tasks like engraving or threading.Reduction in Operational Noise and Vibration: Higher quality milling heads are often designed to operate more smoothly and quietly, reducing vibration and operational noise. This not only creates a more pleasant work environment but can also enhance the precision of cuts by minimizing disturbances during machining.Energy Efficiency: Advanced milling heads may be more energy-efficient due to improved design and materials that reduce friction and energy consumption during operation. This can lead to lower operational costs and a smaller environmental footprint.Ease of Maintenance: Yih Kuan’s milling heads are designed for ease of maintenance, featuring components that are easily accessible and replaceable. This simplifies routine maintenance tasks and reduces downtime associated with servicing.Customization and Tailored Solutions: Yih Kuan offers customized milling heads tailored to specific customer needs and machining challenges. This level of customization ensures that the milling head perfectly matches the specific requirements of the knee mill and the tasks it performs, maximizing efficiency and results.Better Surface Finish Quality: The precision and stability provided by superior milling heads result in better surface finish quality, crucial for industries where aesthetics or surface integrity are important, such as in automotive and aerospace parts manufacturing.Increased Operator Safety: With features that might include enhanced guards and more robust safety mechanisms, upgraded milling heads can make the machine safer to operate. Enhanced control and precision also reduce the likelihood of errors that could lead to accidents.Applications in IndustriesManufacturing: Ideal for producing parts with complex designs, especially where precision is critical.Education and Prototyping: Used in educational settings for training purposes and in R&D for developing new products.Custom Machining: Especially useful for custom manufacturing shops that require flexibility to adapt to various jobs.ConclusionKnee mills are an essential component of many machining setups, and their functionality can be greatly enhanced by using Yih Kuan's vertical turret milling heads. Whether you are looking to upgrade an existing knee mill or enhance a new setup, Yih Kuan provides a range of milling heads that ensure top performance and adaptability.Call to ActionTo discover more about how Yih Kuan's milling heads can elevate your knee mill's capabilities, visit our website at Yih Kuan's product page. Contact us today to find the perfect milling head for your needs and take your machining process to the next level.
12. 30. 2024
more
In low-volume, high-mix manufacturing, traditional milling machines stand out for their flexibility and low cost, despite lacking the automation and mass production capabilities of CNC machines. When paired with YIH KUAN’s high-performance milling heads, traditional milling machines can maximize their potential and become a cost-effective and efficient solution for a wide range of manufacturing needs.Advantages of Traditional Milling Machines in Low-Volume, High-Mix ManufacturingHigh FlexibilityTraditional milling machines are ideal for non-standard, short-run, or prototype machining, requiring no programming to start.Operators can manually adjust machining parameters on the fly, handling complex shapes or varying dimensions.Lower Initial and Maintenance CostsThey have a lower purchase cost compared to CNC machines, making them suitable for small shops or budget-conscious manufacturers.With simpler structures, maintenance and repair costs are significantly lower.Simplified OperationNo need for specialized CAM software or programming skills, reducing training costs.Ideal for skilled machinists to perform precise work or last-minute modifications.Quick AdaptationPerfect for frequent workpiece changes, reducing downtime caused by program setup, especially for diverse and small-batch orders.How YIH KUAN Enhances Traditional Milling MachinesTo further boost the performance and versatility of traditional milling machines, YIH KUAN offers a range of premium milling heads and services, transforming your equipment into a highly efficient tool.High-Quality Milling Heads for Flexible OperationsYIH KUAN provides turret milling heads, plano milling heads, and angle heads, enabling multi-angle and multifunctional machining.Customized Solutions to Meet Unique NeedsWhether for irregular workpieces, special materials, or multi-process combinations, we provide tailored milling head solutions to meet specific requirements.Cost Reduction and Efficiency ImprovementWith YIH KUAN’s milling heads, traditional milling machines can handle some complex processes typically reserved for CNC machines, avoiding expensive equipment investments.Durability and Stability for Reliable OperationsMade from high-wear-resistant materials and precision-engineered, YIH KUAN’s products are long-lasting and stable, reducing maintenance costs and downtime.Quick Delivery and Technical SupportYIH KUAN ensures rapid response to customer needs, providing comprehensive technical support for smooth and efficient machining.Traditional Milling Machines vs. CNC Machines: When to Choose Traditional?CategoryAdvantages of Traditional Milling MachinesAdvantages of CNC MachinesInitial CostLower cost, ideal for small workshops or businesses with limited budgets.Higher cost but offers long-term returns for mass production.FlexibilityNo programming needed; perfect for small-batch, diverse workpiece production.Excels in automated, high-volume production.Maintenance CostSimple structure with lower repair and maintenance expenses.Complex systems with higher repair costs.Speed and PrecisionSuitable for prototypes or quick setups, but precision relies on operator expertise.High precision and consistency for large-scale or complex machining.Best ApplicationsResponsive to on-demand production, custom parts, or sample creation; ideal for small shops or single-operator setups.Standardized mass production or projects requiring consistent accuracy.Contact YIH KUAN to Unlock the Full Potential of Your Traditional Milling Machines!YIH KUAN is dedicated to helping you enhance the performance of traditional milling machines for low-volume, high-mix manufacturing. With our customized products, technical support, and premium milling heads, we ensure your operations become more efficient, flexible, and competitive.Phone: +886 424914376Email: yihkuan.salesperson@gmail.comWebsite: www.yihkuan.comSocial Media: Search "YIH KUAN" for the latest updates and success stories!Partner with YIH KUAN to explore new machining possibilities. Contact us today and take your operations to the next level!
12. 17. 2024
more
YIH KUAN’s Manual and Semi-Automatic Milling Heads: Advantages and Selection GuideWhen selecting a milling head, understanding the features and applications of different models is crucial. YIH KUAN (YIH KUAN) offers manual and semi-automatic milling heads to meet diverse customer needs. Below is a comparison of these two types to help you find the best solution.Manual Milling Heads: Flexible, Durable, and Cost-EffectiveYIH KUAN’s manual milling heads are renowned for their operational flexibility and high cost-effectiveness, making them an ideal choice for small to medium-sized workshops or customized machining.Key Advantages:Affordable Price: Manual milling heads have a lower cost, making them particularly suitable for users with limited budgets.Flexible Operation: Manual adjustment of angles and feed allows quick adaptation to various machining needs, especially in small-batch or non-standard part processing.Simple and Durable: Featuring a simple structure, YIH KUAN’s manual milling heads offer long service life and low maintenance costs. The design is optimized to maintain stability under demanding operational conditions.Application Scenarios:Manual milling heads are ideal for tasks that require frequent adjustments to machining angles, such as mold repair, small parts manufacturing, or maintenance work. For customers needing high flexibility with limited production scales, manual milling heads are the most economical choice.Semi-Automatic Milling Heads: A Perfect Balance of Efficiency and FlexibilityIf your production needs require partial automation without the expense of fully automatic equipment, YIH KUAN’s semi-automatic milling heads are the ideal choice.Key Advantages:Improved Efficiency: Semi-automatic milling heads combine manual and automatic functions, enabling partial automation of machining processes to significantly boost productivity.Simplified Operation: YIH KUAN’s semi-automatic milling heads come equipped with easy-to-use CNC adjustment features, reducing the workload of operators while enhancing machining consistency.Economic Choice: Compared to fully automatic milling heads, semi-automatic models strike a balance between price and functionality, making them suitable for medium-sized enterprises engaging in batch production.Application Scenarios:Semi-automatic milling heads are ideal for businesses seeking increased efficiency but with moderate production scales. For example, they excel in batch production of medium-sized parts, saving labor costs and ensuring machining precision.YIH KUAN’s Quality Commitment and ServiceYIH KUAN is dedicated to providing customers with high-quality manual and semi-automatic milling heads. Our products feature stable structures, exceptional durability, and comprehensive after-sales service and technical support. Whether you are a small workshop requiring flexible operations or a medium-sized manufacturer prioritizing efficiency, YIH KUAN can tailor the best solution for your needs.Key Takeaways: How to Choose the Right Milling HeadIf you value cost-effectiveness and operational flexibility, choose manual milling heads.If you need a balance of efficiency and functionality, semi-automatic milling heads are your best option.If you have any questions or specific requirements, feel free to contact YIH KUAN. We look forward to providing you with the most professional service and advice to help you achieve your machining goals!
12. 09. 2024
more
In modern manufacturing, Environmental, Social, and Governance (ESG) factors have become critical indicators for companies striving for sustainable development. YIH KUAN milling heads, known for their high quality and efficiency, not only enhance machining performance but also support users in making tangible progress toward ESG goals. This article explores the relationship between upgrading milling heads and the three ESG dimensions, along with the specific benefits it brings.1. Environmental: Reducing Carbon Footprint and Improving Resource UtilizationEnergy Savings and Emissions Reduction:Replacing old milling heads with YIH KUAN’s high-efficiency models can significantly reduce energy consumption. For instance, their precision-engineered power transmission mechanisms and energy-efficient operation modes decrease electricity usage during machining, thereby lowering carbon emissions.Reduced Material Waste:YIH KUAN milling heads’ high-precision capabilities minimize machining errors and defect rates, conserving raw materials and reducing production waste.Extended Equipment Lifespan:Upgrading outdated milling heads not only extends the overall machine’s lifespan but also reduces the need for disposing of obsolete equipment, thereby mitigating waste management demands.2. Social: Creating a Safer and More Efficient Work EnvironmentEnhanced Operational Safety:The ergonomic design of YIH KUAN milling heads reduces risks of workplace injuries caused by equipment malfunctions or operational errors, providing workers with a safer environment.Increased Job Satisfaction:Upgrading milling heads allows employees to operate more stable and efficient equipment, easing their workload and enhancing their sense of pride and satisfaction with their company.Supporting Technological Advancement:With features like automation and smart functionality, YIH KUAN milling heads help employees master the latest manufacturing technologies, boosting their professional competitiveness.3. Governance: Strengthening Competitiveness and Meeting Sustainability StandardsRegulatory Compliance:Many countries impose stringent requirements on equipment energy efficiency and environmental impact. Choosing YIH KUAN milling heads ensures compliance with international standards, avoiding legal risks.Enhanced Market Competitiveness:The superior performance and sustainable design of YIH KUAN milling heads build greater customer trust and attract ESG-conscious partners and clients.Lower Operational Costs:High-performance milling heads reduce downtime for maintenance and energy consumption, helping companies enhance productivity while lowering operational expenses.YIH KUAN’s Commitment: Realizing Sustainability and InnovationAs a professional milling head manufacturer, YIH KUAN is dedicated to leveraging technological innovation and high-quality products to help clients achieve both productivity improvement and sustainable development. We firmly believe that upgrading milling heads is not merely about improving equipment performance but also a commitment to environmental, social, and governance responsibilities.Choose YIH KUAN milling heads and join us in creating a sustainable future!
12. 03. 2024
more
Introduction In the machining world, flexibility and precision are paramount. Turret milling heads are renowned for their versatility, making them indispensable tools in various milling environments. This article explores how turret milling heads can be effectively used in knee mills, turret mills, and bed mills, enhancing their functionality and expanding their machining capabilities.1. Turret Milling Heads in Knee MillsKnee mills, characterized by their adjustable table (or 'knee'), are popular in tool rooms and small manufacturing setups due to their simplicity and effectiveness. The addition of a turret milling head to a knee mill transforms it into a more versatile machine, capable of more complex operations with improved precision.Enhanced Flexibility: Turret milling heads allow knee mills to perform a variety of functions such as angular milling, drilling, and boring, which are otherwise limited in traditional setups.Applications: Ideal for small batch productions and custom work where frequent adjustments are required.2. Enhancing Turret Mills with Turret Milling HeadsTurret mills themselves offer significant versatility and are preferred for their ease of use and precise control. By integrating a turret milling head, these machines can achieve even greater accuracy and flexibility.Multi-Angle Machining: With a turret milling head, operators can easily adjust the cutting angle without repositioning the entire workpiece, making it perfect for creating complex shapes and profiles.Applications: Suitable for educational institutions, R&D departments, and any manufacturing process where versatility is required without large-scale production demands.3. Turret Milling Heads on Bed MillsBed mills feature a stationary table with the spindle moving perpendicular to the table surface. Adding a turret milling head introduces additional axes of movement, thereby expanding the types of operations that can be performed.Increased Capabilities: A turret milling head on a bed mill allows for more complex geometries and can significantly reduce setup times by facilitating multi-angle cuts in a single setup.Applications: Great for heavy-duty manufacturing environments such as in the automotive and aerospace sectors where large, complex parts are common.ConclusionThe integration of turret milling heads into knee mills, turret mills, and bed mills not only broadens the scope of these machines but also enhances their operational efficiency. This upgrade allows manufacturers to tackle more complex projects with precision, making the most out of their existing equipment.Call to ActionTo learn more about how a turret milling head can revolutionize your milling operations, or to explore the right type of milling head for your machinery, contact Yih Kuan Enterprise Co., Ltd. today. We offer expert advice and high-quality solutions tailored to meet your machining needs.
10. 28. 2024
more
In the composition of a milling machine, the milling head is one of the core components that determines machining performance. The milling head directly affects the precision, efficiency, and stability of the machining process. As a critical part of hardware component manufacturing, choosing a high-quality milling head can significantly improve production efficiency and reduce equipment maintenance costs.As a professional milling head manufacturer, YIH KUAN Enterprise is dedicated to providing a diverse range of milling head products to meet the various machining needs of hardware manufacturers. YIH KUAN’s product line includes vertical milling heads, horizontal milling heads, gantry milling heads, and angle heads, all known for their high precision and stability, capable of handling a wide range of complex metal machining applications.YIH KUAN Enterprise not only provides standardized milling heads but also offers customized solutions tailored to the specific needs of clients, making them suitable for hardware manufacturers of different scales. The milling heads from YIH KUAN feature the following advantages:High-precision machining: YIH KUAN's milling heads are designed with precision to ensure stable accuracy even during long-term operation, making them ideal for machining various precision hardware components.Durability and reliability: YIH KUAN uses high-quality materials to manufacture its milling heads, ensuring that the products remain reliable under heavy loads and extended operation, reducing downtime and increasing production capacity.Diverse options: Whether for traditional milling machines or modern CNC milling machines, YIH KUAN provides suitable milling head accessories to adapt to different machining processes.YIH KUAN's Customization ServicesIn addition to providing high-quality standard products, YIH KUAN also possesses strong technical expertise to design and manufacture milling heads according to clients' specific needs. For hardware manufacturers with special machining requirements, YIH KUAN works closely with them from design to production, ensuring that the milling heads perfectly fit their production processes.YIH KUAN Enterprise’s professional services cover not only the manufacturing and maintenance of milling heads but also provide comprehensive technical support, ensuring that every customer can maximize the efficiency of their milling machines, thus enhancing production efficiency and product quality.
10. 18. 2024
more
In the rubber and plastics industry, milling machines are critical equipment for mold manufacturing and processing, especially in the machining of precision molds and composite materials. These machines significantly improve product accuracy and production efficiency. Depending on different machining needs, the following milling machines are commonly used in the rubber and plastics industry:Vertical Milling Machines:Used for detailed mold processing, suitable for precision cutting on vertical surfaces, particularly for producing complex mold shapes.Horizontal Milling Machines:Suitable for machining flat and long workpieces in large quantities, ideal for large-scale mold cutting.Gantry Milling Machines:Equipped with a large worktable, these machines are ideal for rough and fine machining of large molds and can handle complex angle cutting.CNC Milling Machines:With high precision and automation capabilities, they are suitable for producing high-precision and complex molds, ensuring consistency in each workpiece.Angle Heads:Used for machining at special angles, offering flexible adjustment of cutting directions, especially for irregular-shaped workpieces.◎The Key Role of Milling HeadsMilling heads play a crucial role in the milling process within the rubber and plastics industry. They determine the angle, flexibility, and precision of the cutting process. The choice of milling heads directly affects the quality of the workpiece and production efficiency. Yih Kuan Enterprise's angle heads and gantry milling heads perform exceptionally well in handling complex mold processing, allowing for precise angle adjustments and accommodating diverse workpiece requirements.The flexibility and high precision of milling heads ensure stable machining, while reducing workpiece changeover time, thus increasing production line efficiency. Replacing milling heads not only extends the overall lifespan of the equipment but also adapts to various machining environments, giving companies a competitive edge in mass production.These milling technologies play a critical role in mold processing and mass production in the rubber and plastics industry. By utilizing angle and gantry milling heads produced by Yih Kuan Enterprise, companies can improve production efficiency and meet the demands of precision machining.
09. 20. 2024
more
IntroductionTurret milling machines are foundational in many manufacturing settings, valued for their versatility and precision in detailed machining tasks. To further enhance their capabilities, Yih Kuan Enterprise Co., Ltd. introduces innovative milling heads, including horizontal and angle heads, designed to extend the functionality and efficiency of turret milling machines. For more insights on the importance of angle heads in turret milling, explore our detailed discussion here.Understanding Turret Milling MachinesTurret milling machines are distinguished by their stationary spindle and the table that moves both perpendicular and parallel to the spindle axis to accomplish cutting tasks. This configuration allows for flexible machining operations, making the turret mill ideal for smaller manufacturing jobs involving intricate detailing or prototyping.Key Advantages of Turret Milling MachinesVersatility: They can perform a range of functions including drilling, cutting, and shaping across multiple axes.Precision: With advanced controls, they can achieve precise cuts with high accuracy.Ease of Use: Turret mills are generally more user-friendly and easier to set up compared to larger milling machines.Integrating AdvancedMilling Heads Yih Kuan's new line of milling heads, specifically designed for turret milling machines, expands these capabilities:Horizontal Milling Heads: These enhance the ability to efficiently remove material over large surface areas, making them ideal for jobs requiring extensive milling.Angle Heads: Allow machining at various angles, significantly reducing the setup time and enabling complex geometries to be machined more easily.Applications and BenefitsEnhanced Machining Options: With the integration of these advanced milling heads, manufacturers can take on more complex projects, such as multi-angle cuts and extensive material removal, without the need for multiple setups or different machines.Increased Productivity: The ability to perform diverse tasks with a single setup reduces downtime and increases throughput.Cost Efficiency: By enhancing the capabilities of the turret milling machine, manufacturers can avoid the high costs associated with purchasing specialized machinery.Maintenance and ReplacementMaintaining these advanced milling heads involves regular checks for alignment, wear, and proper lubrication. Signs that indicate a need for maintenance or replacement include unusual noise, decreased efficiency, and poor finish quality. Timely attention to these signs ensures continuous high performance and extends the lifespan of both the machine and the head.ConclusionThe addition of Yih Kuan’s advanced milling heads to your turret milling operations can transform your production capabilities, making it possible to tackle more complex and varied tasks efficiently. For manufacturers looking to enhance their machining processes and explore new manufacturing possibilities, Yih Kuan offers the tools and expertise to make it happen.Call to ActionExplore the full potential of your turret milling machines with Yih Kuan’s innovative milling heads. Contact us today to learn more about how our products can enhance your manufacturing efficiency and productivity.
09. 13. 2024
more
Milling machines play a crucial role in the semiconductor industry. While the core work in semiconductors primarily involves manufacturing tiny electronic components, milling machines are indispensable tools in the production of processing equipment and related precision parts. Yih Kuan Enterprise, as a professional milling head manufacturer, is dedicated to providing high-precision, high-performance milling heads suitable for various applications in the semiconductor industry. Here are the applications of milling machines and Yih Kuan’s milling heads in the semiconductor industry:1. Processing Equipment ComponentsSemiconductor manufacturing equipment requires highly precise components, such as mechanical structures, supports, and bases. Yih Kuan’s high-precision milling heads play a key role in processing these components. By using Yih Kuan milling heads, manufacturers can significantly enhance machining accuracy, reduce errors, and ensure stable operation of the equipment under the high demands of semiconductor manufacturing processes.2. Mold ManufacturingIn the semiconductor packaging process, molds are used to create the casings for chip packaging, requiring extremely precise machining. Yih Kuan’s milling heads are particularly important in mold manufacturing. The specialized milling heads provided by Yih Kuan achieve the required surface finish and dimensional accuracy, ensuring high-quality mold manufacturing and long-lasting durability.3. Heat Diffusion Equipment ProcessingSome semiconductor processes require heat diffusion techniques, and the manufacturing of this equipment often involves milling machines. Using Yih Kuan’s specially designed milling heads allows for better control of heat generation during machining, reducing material deformation and ensuring long-term stability and accuracy of the equipment.4. Test Fixture ManufacturingMilling machines can also be used to manufacture various test fixtures, which are used to hold semiconductor wafers and other components for testing and analysis. Yih Kuan’s milling heads, with their precise design, improve the accuracy and efficiency of fixture manufacturing, ensuring stability and reliability during testing processes.5. Reducing Energy Consumption and Improving EfficiencyIn the semiconductor industry, choosing the right milling heads can effectively reduce energy consumption and improve machining efficiency. Yih Kuan’s high-performance milling heads can reduce mechanical wear and heat generation, thereby lowering cooling requirements and energy consumption. This not only helps to reduce operating costs but also aligns with environmental protection and sustainable development goals.In conclusion, milling machines and Yih Kuan’s specialized milling heads have a wide range of applications in the semiconductor industry. Whether it is for processing equipment components, mold manufacturing, or test fixture production, high-precision and high-performance Yih Kuan milling heads are indispensable. By selecting and using Yih Kuan milling heads, companies can effectively enhance machining accuracy, efficiency, and environmental performance, allowing them to play a greater role in semiconductor manufacturing.
09. 03. 2024
more
IntroductionIn the realm of industrial manufacturing, gantry milling machines stand out for their robust capabilities in handling large and intricate workpieces. The decision between CNC and traditional gantry milling machines can impact production efficiency, precision, and operational cost. This article delves into the distinctions between these two types of machines, discusses the critical role of milling heads manufactured by Yih Kuan, and outlines best practices for their maintenance and replacement.Understanding Gantry Milling MachinesGantry milling machines feature a bridge-like structure that spans over the workpiece, allowing the milling head to move along the X, Y, and Z axes. This setup provides stability and support for machining large parts, making it ideal for heavy-duty industries.CNC Gantry Milling MachinesTechnology: Utilizes computer numerical control to automate and precisely control all movements, ensuring high accuracy and repeatability.Advantages: Offers significant improvements in speed, efficiency, and the ability to produce complex geometries with minimal human intervention.Industries Served: Particularly favored in aerospace, automotive, and precision engineering industries where complex, repetitive tasks are common.Traditional Gantry Milling MachinesTechnology: Operates based on manual adjustments and settings, which requires skilled operators to achieve the desired accuracy.Advantages: Cost-effective for simpler, less intricate tasks. It allows for direct control and adjustments by the operator, often preferred in custom or specialized projects.Industries Served: Used widely in shipbuilding, heavy equipment fabrication, and industries where large scale, less complex machining is required.The Role of Milling Heads in Gantry Milling MachinesMilling heads play a pivotal role in the functionality of both CNC and traditional gantry milling machines. Yih Kuan designs and manufactures high-quality milling heads suitable for a diverse range of machining needs, ensuring that whether your operations require precision CNC applications or robust traditional machining, the right tool is available.Importance of Milling Heads: The performance of a gantry milling machine largely depends on the quality and condition of its milling head. These components are crucial for efficiently cutting, carving, and shaping metal and other materials. The precision and durability of a milling head significantly influence the machining accuracy and the quality of the final product.Maintenance and Replacement Indicators:Maintenance: To ensure consistent performance and prolong the life of milling heads, regular maintenance is crucial. This includes routine lubrication, cleaning, and inspection for wear and tear. Keeping milling heads in good condition helps in maintaining the precision and efficiency of the machine.Signs that Indicate Maintenance or Replacement:Decreased Performance and Efficiency: If the milling machine starts taking longer to complete tasks or struggles with operations that it used to handle easily, it might be time to check the milling head.Poor Surface Finish: A deterioration in the surface finish of machined parts, such as roughness or unexpected marks, can indicate that the milling head is worn out or damaged.Increased Vibration or Noise: An increase in noise or vibration during operation can suggest that the milling head's components may be worn or misaligned.Visible Wear or Damage: Any visible cracks, chips, or wear on the milling head are clear indicators that maintenance or replacement is necessary.Excessive Heat Generation: Overheating during operations can be a sign of a dull or improperly lubricated milling head.Difficulty in Tool Insertion or Removal: Problems with changing tools can indicate issues with the spindle or tool holder components of the milling head.Choosing Between CNC and Traditional MachinesWhen deciding between a CNC and a traditional gantry milling machine, manufacturers should consider:Production Requirements: Evaluate the complexity of the parts being produced and the precision required.Volume: High-volume manufacturers may find the automation of CNC machines more beneficial, while traditional machines may be more cost-effective for lower volumes.Cost: CNC machines represent a higher initial investment but offer savings through faster production times and reduced labor costs over time.ConclusionThe choice between CNC and traditional gantry milling machines depends largely on specific production needs, cost considerations, and desired outcomes. With Yih Kuan’s high-quality milling heads, manufacturers can enhance both types of machines, ensuring efficient and precise machining operations. Yih Kuan remains committed to supporting manufacturers in choosing the right equipment and maintaining it to the highest standards. For further information on selecting and caring for milling heads suitable for your gantry milling machines, please contact Yih Kuan. We are dedicated to helping you optimize your manufacturing processes and achieve superior results.
08. 16. 2024
more
IntroductionAngle milling heads are pivotal in enhancing the versatility and efficiency of machining operations, allowing machines to reach otherwise inaccessible angles with precision. At Yih Kuan, we offer a range of angle milling heads including 90° angular heads, 90° deep milling heads, and 45° universal milling heads, designed to fit various machining setups such as vertical/horizontal machining centers, gantry milling machines, boring mills, and milling machines. This article explores the distinct features and applications of each type to help you select the best milling head for your requirements.Understanding Different Angle Milling HeadsAngle milling heads are specialized tools that facilitate machining at various angles, which is critical when working on complex parts with intricate geometries. Here are the key differences between the angle heads we offer:90° Angular HeadFeatures: This head positions the tool at a precise 90-degree angle relative to the workpiece, making it ideal for side milling, drilling, and tapping operations that require orthogonal approaches.Applications: Perfect for jobs that demand precision in creating perpendicular features and external edges.90° Deep Milling HeadFeatures: Similar to the standard 90° angular head but designed for deeper cuts and extended reach within cavities or alongside protrusions.Applications: Used extensively in mold making and automotive industries where accessing deep pockets and performing complex side milling are necessary.45° Universal Milling HeadFeatures: Offers the flexibility to adjust the tool orientation to 45 degrees, providing an optimal angle for chamfering, beveling, and inclined surface machining.Applications: Ideal for aerospace and general engineering sectors where angled features and chamfers are frequently required.How to Choose the Right Angle Milling HeadSelecting the appropriate angle milling head depends on the specific machining tasks and the geometry of the parts being manufactured:Material and Geometry Considerations: Assess the types of materials you work with and the complexities of the part geometries. For standard side milling and drilling, a 90° angular head might suffice, while more complex parts with deep recesses may necessitate a 90° deep milling head.Machining Center Compatibility: Ensure the selected head is compatible with your existing machining center in terms of mounting, rotational speed, and torque capabilities.Production Requirements: For high-volume production with repetitive angled cuts or features, the 45° universal milling head offers the versatility needed for various operations without the need for frequent tool changes.ConclusionAngle milling heads significantly expand the capabilities of standard machining centers by allowing for precise angled cuts and operations. Whether you need a head for straightforward perpendicular operations, deep pocket machining, or versatile angled applications, Yih Kuan has the solution. Our range of 90° angular heads, 90° deep milling heads, and 45° universal milling heads are engineered to meet diverse manufacturing needs, enhancing both flexibility and precision in your machining processes. For more information on how our angle milling heads can benefit your operations, or to discuss your specific machining challenges, please contact Yih Kuan. We’re here to help you achieve optimal machining efficiency and quality.
07. 26. 2024
more
In the mold industry, traditional milling machines such as turret milling machines and gantry milling machines play a crucial role in ensuring high precision, efficiency, and flexibility in mold manufacturing. Despite the advancements in CNC technology, these traditional machines remain indispensable for various reasons.1. Precision and VersatilityTraditional milling machines are known for their ability to perform a wide range of operations with high precision. Turret milling machines, for example, offer versatile functionalities such as drilling, cutting, and slotting, which are essential for producing complex mold components. Gantry milling machines, with their large worktable and high rigidity, excel in machining large and heavy molds with intricate details.2. Robustness and StabilityThe robust construction of traditional milling machines ensures stable and accurate machining. Gantry milling machines, in particular, provide exceptional stability due to their strong and rigid structure, making them ideal for heavy-duty operations. This stability reduces vibrations and enhances the precision of the final mold, ensuring a high-quality end product.3. Cost-EffectivenessTraditional milling machines often have lower initial costs compared to advanced CNC machines. This makes them an attractive option for small to medium-sized mold manufacturers. Additionally, the maintenance and operational costs of traditional milling machines are generally lower, contributing to overall cost savings for the company.4. Adaptability to Various MaterialsTraditional milling machines can handle a variety of materials, from metals like steel and aluminum to plastics and composites. This adaptability is crucial in the mold industry, where different projects may require the use of different materials. The ability to switch between materials without significant reconfiguration makes these machines highly versatile.5. Skilled Workforce UtilizationMany skilled machinists are well-versed in operating traditional milling machines. Leveraging their expertise can enhance productivity and ensure high-quality outcomes. This existing knowledge base reduces the need for extensive retraining and allows for a smoother workflow within the manufacturing process.6. Customization and FlexibilityTurret and gantry milling machines allow for a high degree of customization. Machinists can manually adjust settings to accommodate specific project requirements, offering flexibility that is sometimes limited in fully automated systems. This customization capability is particularly valuable for producing unique or specialized molds.7. Enhancing Production EfficiencyWhile traditional, these milling machines can be integrated into modern production systems to enhance efficiency. For instance, combining manual adjustments with digital readouts and automated controls can improve precision and reduce setup times. This hybrid approach can maximize the strengths of traditional milling while incorporating modern efficiencies.8. Reducing Energy ConsumptionTraditional milling machines, when properly maintained, can operate efficiently with moderate energy consumption. Implementing energy-efficient practices, such as regular maintenance and optimized machining processes, can further reduce energy usage. This focus on energy efficiency not only lowers operational costs but also aligns with sustainable manufacturing practices.ConclusionTraditional milling machines, including turret milling machines and gantry milling machines, continue to hold significant importance in the mold industry. Their precision, versatility, robustness, cost-effectiveness, and adaptability make them indispensable tools for mold manufacturers. Yih Kuan can assist milling machine users with upgrades and spindle head replacement services. Through performance matching and custom integration, manufacturers can achieve a balance of production efficiency, quality, and sustainability at a lower cost.
07. 03. 2024
more
IntroductionTurret milling machines are versatile tools in the machining industry, known for their ability to perform a wide range of cutting operations. Central to their functionality are the turret milling heads, which define the capabilities and the precision of machining operations. This article explores the differences between "stepped speed" and "variable speed" milling heads and provides guidance on how to select the right one for specific machining needs, with a focus on the offerings from Yih Kuan.What are Turret Milling Heads?Turret milling heads are the part of the turret milling machines where the tool is mounted. They allow the tool to move vertically, horizontally, or at any angle, enabling complex cutting tasks. The choice between different types of milling heads can impact the machine’s versatility, speed, and precision.Stepped Speed vs. Variable Speed Turret Milling HeadsStepped Speed Turret Milling HeadsDefinition and Characteristics: These milling heads operate at predefined speed ranges set by the manufacturer. Speed changes are achieved through a geared mechanism, requiring manual adjustment to shift between different speed settings.Advantages: Provides reliable and stable speed options, typically cost-effective and easier to maintain due to simpler mechanical designs.Variable Speed Turret Milling HeadsDefinition and Characteristics: These heads allow operators to adjust the spindle speed continuously within a range, usually through a dial or a digital interface. This adjustment is done without steps, offering seamless transitions.Advantages: Greater flexibility and precision, allowing the operator to fine-tune the spindle speed based on the material being machined and the type of operation being performed.Choosing the Right Turret Milling HeadChoosing the appropriate turret milling head depends heavily on the specific requirements of your manufacturing environment. Here are some detailed considerations:Assessing NeedsMaterial Types:Soft Materials (Aluminum, Brass, Plastics): Soft materials often require higher spindle speeds to ensure clean cuts and efficient milling. Variable speed heads are ideal for these materials because they allow operators to easily adjust and fine-tune the speed to match the material properties, preventing material deformation or melting.Hard Materials (Stainless Steel, Titanium): Hard materials require lower spindle speeds but higher torque to manage the cutting forces without damaging the tool or workpiece. Stepped speed heads, with their robust gearing and stable speed settings, are typically well-suited for such tasks, as they provide the necessary power at consistent speeds.Mixed Materials: Workshops that handle a diverse range of materials might prefer variable speed heads for their adaptability, allowing operators to switch easily between high and low speeds as needed.Production Volume:High-Volume Production: Environments such as automotive or consumer goods manufacturing, where the same material and operation are repeated, often benefit from stepped speed heads. These heads are designed for longevity and consistent performance under repetitive tasks, making them cost-effective for high-volume production.Low-Volume, Custom Jobs: Specialized industries like aerospace or custom fabrication, where materials and specifications can vary greatly between projects, benefit from the versatility of variable speed heads. These allow for precise speed control and adjustments between jobs without compromising on quality.Budget Constraints:Initial Costs: Stepped speed heads are generally less expensive upfront compared to their variable speed counterparts. They offer a lower entry price, making them attractive for new or budget-conscious operations.Maintenance Costs: Consider not only the initial purchase cost but also the long-term maintenance. Variable speed heads, while more expensive upfront, may require more frequent maintenance due to their complex mechanical and electronic components. However, the ability to optimize tool life and reduce waste might offset these costs.Operational Efficiency: Evaluate the potential for increased productivity and reduced waste, which can influence the total cost of ownership. For example, variable speed heads can lead to better surface finishes and faster job turnaround times, which might justify the higher initial investment.ExamplesFabrication Shop Handling Multiple Materials: A custom job shop working with everything from soft aluminum to hard titanium would benefit significantly from a variable speed head due to the need for a wide range of speeds to match material properties.Dedicated Steel Part Production Line: A production line dedicated to cutting tough steels or other hard materials may opt for stepped speed heads to take advantage of their durability and consistent performance under demanding conditions.ConclusionThe choice between stepped and variable speed turret milling heads should align with your specific manufacturing needs. Understanding the advantages of each can significantly influence productivity and machining quality. At Yih Kuan, we specialize in providing top-quality turret milling heads tailored to meet the diverse needs of our clients. Whether you require stepped speed for consistent heavy-duty use or variable speed for flexibility in high-precision tasks, Yih Kuan is here to assist. For more information or to discuss your specific needs, please contact us.
06. 07. 2024
more
IntroductionGantry milling machines are a cornerstone in the field of large-scale industrial manufacturing, known for their robust construction and versatility in handling diverse machining tasks. Central to their functionality are the milling heads, which define the capabilities and the precision of machining operations. This article delves into the different types of milling heads available for gantry milling machines and discusses how many heads can be installed on a single machine, enhancing its operational flexibility and productivity.Types of Gantry Milling Machine HeadsGantry milling machines can be equipped with various types of milling heads, each designed to meet specific machining needs. Here are some of the most common types:Standard Milling Head: This is the most commonly used head, capable of handling a wide range of milling tasks. It's versatile and can be used for general cutting, drilling, and milling operations.Universal Milling Head: Allows for adjustments in multiple axes, providing the ability to machine at various angles. This head is ideal for complex geometries and multi-angle cuts.High-Speed Milling Head: Designed for precision and speed, high-speed heads are perfect for fine detailing and finishing tasks that require rapid spindle speeds.Heavy-Duty Milling Head: Built to handle large and hard materials, these heads offer increased power and torque, making them suitable for heavy cutting operations.Turret Milling Head: Turret heads include multiple tooling options that can be indexed and changed, offering quick tool changes without manual intervention, thus reducing downtime and increasing efficiency.Angle Heads: These are specialized heads that allow the tool to operate at an angle relative to the workpiece, ideal for inaccessible areas or specific applications where direct vertical or horizontal machining cannot be performed.Configuration Flexibility: How Many Heads Can a Gantry Milling Machine Install?The versatility of a gantry milling machine not only lies in its size and power but also in its ability to accommodate multiple heads. Depending on the size and design of the gantry milling machine, several configurations are possible:Single Head Setup: Most basic gantry mills are equipped with one milling head, suitable for straightforward, singular machining processes.Dual Head Configuration: More advanced machines can be fitted with two heads, either of the same type for parallel processing or different types for performing distinct operations simultaneously. This setup is particularly useful for increasing production rates and offering more versatility in machining. Common dual head configurations include:Standard Milling Head and Specialized Milling Head:This configuration includes a standard milling head, which is suitable for general milling operations.The other head might be a specialized milling head, such as an Angular Milling Head, used for machining at specific angles, or other specialized applications.Standard Milling Head and High-Speed Milling Head:One head is a conventional milling head, suitable for most standard operations.The other is a high-speed milling head, particularly suited for tasks requiring high precision and high surface quality, often used in high-speed cutting (HSC).Standard Milling Head and Heavy-Duty Milling Head:One head is used for regular machining, while the other is designed for heavy-duty applications, featuring higher torque and power, specifically for handling harder or larger materials.Two Universal Milling Heads:In this configuration, both milling heads are universal, capable of flexibly handling a variety of machining needs; each head can perform independent, multi-axis operations.Multiple Head Systems: Some specialized gantry milling machines can accommodate three or more heads, significantly expanding their capability to perform complex and varied tasks in a single setup. This configuration is ideal for high-volume production environments where different processes need to be executed quickly and simultaneously.ConclusionChoosing the right combination of milling heads for a gantry milling machine significantly enhances its versatility and productivity. Whether it involves combining a standard milling head with a high-speed head for precision work, or pairing a standard head with a heavy-duty head for tougher materials, the right setup can vastly improve the output and efficiency of machining operations.At Yih Kuan, we specialize in manufacturing a wide range of milling heads designed to meet various industrial needs. Our expertise ensures that each product is crafted with precision and designed to deliver top performance. We understand that selecting the right milling head can be complex, which is why our team is always ready to provide expert advice and support.If you have any questions about milling heads or need assistance in choosing the best configuration for your operations, please do not hesitate to contact us. We are here to help you enhance your manufacturing capabilities with our high-quality and reliable products.
05. 23. 2024
more
In our recent exploration of the machining world, we've delved into the distinct functionalities and advantages of vertical and horizontal mills, illustrating how each type caters to specific manufacturing needs with unmatched efficiency. As the industry evolves, so does the technology, leading us to a revolutionary advancement that has reshaped modern manufacturing: CNC (Computer Numerical Control) milling machines.What is a CNC Milling Machine? A CNC milling machine is a sophisticated type of milling machine controlled by a computer, enabling precision machining of complex parts with minimal human intervention. Unlike traditional milling machines, which require manual adjustment and operation, CNC mills operate based on digital instructions derived from a CAD (Computer-Aided Design) file.Advantages of CNC Milling MachinesPrecision and Consistency: CNC milling machines offer exceptional precision, capable of producing parts with tight tolerances repeatedly over large production runs.Handling Complex Geometries: With advanced software guiding their operations, CNC mills can handle complex shapes and patterns that would be difficult, if not impossible, to achieve manually.Increased Productivity: Automation and the ability to run 24/7 with minimal downtime significantly increase production capabilities.Flexibility: Quick setup changes and the ease of updating CNC programs make these machines highly adaptable to varying production demands.Reduced Labor Costs: While CNC milling machines represent a significant initial investment, the reduction in manual labor can lead to substantial cost savings over time.Applications of CNC Milling Machines CNC milling machines have found applications in numerous fields, testament to their versatility and efficiency:Aerospace: CNC milling machines produce intricate components designed to withstand extreme conditions, including airframe structures and engine parts.Automotive: Facilitating the fabrication of a diverse array of automotive parts, including engine blocks, custom gears, and complex performance parts.Medical: Supporting the medical industry's need for flawless surgical instruments, orthopedic implants, and custom medical devices, directly impacting patient care and safety.Electronics: Playing a crucial role in manufacturing precise and delicate components essential for the functionality and reliability of consumer electronics.Custom Manufacturing and Prototyping: Offering the versatility to produce parts from a wide range of materials with speed and precision, crucial for innovation and product development across sectors.Conclusion CNC milling machines stand at the forefront of manufacturing innovation, offering unparalleled precision and efficiency that are transforming production processes across a myriad of industries. From aerospace to medical devices and electronics, the versatility of CNC technology is reshaping the manufacturing landscape. At Yih Kuan Ent Co., Ltd., we proudly produce top-tier CNC milling heads essential for the success of any CNC milling operation. Our commitment to excellence ensures that our products meet the highest standards of precision and durability, catering to the diverse needs of industries worldwide.We encourage those looking to enhance their manufacturing capabilities with our cutting-edge CNC milling heads to explore the detailed information and specifications we provide. As a leading contributor to the advancement of CNC milling technology, Yih Kuan Ent Co., Ltd. is your trusted partner in achieving machining excellence. Discover the difference our CNC milling head solutions can make in your production processes by visiting our website or reaching out to our expert team today.
05. 06. 2024
more
IntroductionAmong the variety of milling machine types, bed mills are renowned for their robust construction and high-efficiency machining capabilities, making them a staple in heavy-duty manufacturing industries. This article explores the design, functionality, and various applications of bed mills in modern manufacturing, including the integration of Yih Kuan’s turret milling head, which enhances the versatility and performance of these machines.Bed Mill OverviewDefinition and FeaturesDefinition: A bed mill is a type of heavy-duty milling machine characterized by a worktable fixed onto the machine’s bed, with the spindle moving vertically along the Z-axis.Key Features: Bed mills are known for their high structural rigidity, large table surface area, and excellent load-bearing capabilities, making them ideal for machining large and heavy workpieces.Major ComponentsSpindle Assembly: Drives the cutting tools for various machining operations.Worktable: Secures the workpiece, capable of moving only along the X-axis (horizontal direction).Column and Bed: Provides support for the vertical movement of the spindle, ensuring the machine’s overall rigidity and stability.ApplicationsAerospace: Utilized for machining structural components and engine parts that require extreme precision and rigidity.Mold Manufacturing: Particularly suitable for processing large molds, such as automotive stamping molds.Heavy Industry: Used in the manufacture of large machinery and equipment components, such as generators and large transmission systems.Technological Advances and InnovationsModern bed mills are frequently equipped with CNC systems, significantly enhancing the precision and automation of the machining process. Higher-end models may feature rotating or moving tables, providing greater flexibility and expandability.Maintenance and CareRegular Inspection: Emphasizes the importance of checking lubrication systems and moving parts to ensure smooth operation and longevity.Cleaning and Protection: Due to the size and weight of bed mills, maintaining cleanliness and proper protective measures are crucial to prevent rust and wear.Introducing Yih Kuan’s Turret Milling Head for Bed MillsYih Kuan’s turret milling head is specially designed for use with bed mills, offering enhanced functionality and flexibility. This milling head provides high torque output, making it highly effective for both heavy-duty cutting and precision tasks. The design features quick tool change capabilities, minimizing downtime and boosting productivity. Its compatibility with bed mills allows for a broader range of applications, from simple surface jobs to complex machining operations involving multiple axes.ConclusionBed mills play an indispensable role in the heavy machining sector. As technology evolves, the functionalities of these machines continue to advance to meet the increasingly stringent demands of modern manufacturing. For manufacturers seeking efficient and high-precision machining solutions, understanding and utilizing the advanced features of bed mills, such as those offered by Yih Kuan's turret milling head, is crucial to success. This integration not only enhances the machine's capabilities but also ensures optimal performance and output in challenging industrial tasks.
04. 24. 2024
more
Introduction:
Selecting the perfect milling head is a
crucial step in optimizing your machining operations. YIH KUAN, a leader
in milling head solutions,
offers a diverse range of options, including the Gantry Milling Head (Plano
Milling Head), CNC Milling Head, Turret Milling Head (Bridgeport Milling Head),
and Angle Milling Head (Angle Head). In this comprehensive guide, we will
explore the distinctive features of each milling head and provide insights into
choosing the ideal one for your specific machining needs.
Gantry
Milling Head (Plano Milling Head):
Ideal for large workpieces and heavy-duty machining.
Offers exceptional stability and precision in plano milling
applications.
Consider for projects requiring extensive material removal and
high accuracy.
CNC Milling
Head:
Incorporates advanced computer numerical control (CNC)
technology for unparalleled precision.
Enables complex and intricate machining tasks with ease.
Suitable for industries demanding high repeatability and
efficient programming.
Turret
Milling Head (Bridgeport Milling Head):
Known for its versatility and ease of repositioning, providing
flexibility in machining.
Excellent for both simple and complex milling operations.
Consider for applications where quick tool changes and
adaptability are essential.
Angle Milling
Head (Angle Head):
Designed for machining at various angles, enhancing the
versatility of your milling machine.
Perfect for applications requiring multi-angle cuts and
intricate shaping.
Offers increased accessibility to challenging workpiece
features.
Considerations for Selection:
Workpiece Requirements: Evaluate the size, material, and
complexity of your workpieces to determine the milling head that best
suits your needs.
Precision and Accuracy: Consider the level of precision
required for your machining tasks. CNC Milling Heads are optimal for
high-precision applications.
Flexibility and Versatility: Assess the range of machining
tasks you perform regularly. Turret Milling Heads and Angle Milling Heads
provide versatility for a variety of projects.
Ease of Integration: Ensure seamless integration with your
existing milling machine. YIH KUAN's milling heads are designed for easy
installation and compatibility.
Conclusion:
YIH KUAN's
commitment to innovation and quality is reflected in its range of milling
heads. Whether you prioritize stability, precision, versatility, or advanced
CNC capabilities, YIH KUAN has the perfect milling head for your machining
requirements. Explore the options available at YIH KUAN's product page to
elevate your machining capabilities and achieve unparalleled results.
01. 05. 2024
more
The answer is yes.It is possible to only replace the milling machine head without replacing the entire machine. The head of a milling machine typically includes the main spindle, the tool holder, and the control system, among other components, and these parts may need replacement due to wear and tear, technological advancements, or changes in production requirements.Here are some scenarios where replacing only the milling machine head might be considered:Technological Advancements: If a new milling machine head offers a more advanced control system, higher spindle speed, faster feed rates, or other advantages that are crucial for the existing machine, considering only replacing the head is a viable option.Changes in Production Requirements: If there are changes in production demands and the new milling machine head better meets these changes without requiring a full machine replacement, then replacing only the head may be an economically efficient solution.Cost Considerations: The cost of replacing an entire machine can be relatively high, and replacing only the head might be a more cost-effective option, especially for small to medium-sized businesses or those with budget constraints.Maintenance Reasons: If the other components of the machine are still in good condition and it's only the head that is experiencing issues, replacing only the head can be an effective maintenance solution.However, it's essential to ensure that the new head is compatible with the existing machine, considering factors such as size, control systems, power requirements, and other aspects.
12. 03. 2023
more
Mechanical flange is a common connection method used in engineering, machinery, and pipeline systems. It is used to connect two edges on flat surfaces, typically connecting pipes, valves, pumps, or other equipment together.The main features of mechanical flanges are their ease of disassembly and reliable sealing, making them an essential connection method in many industrial and commercial applications. Here are some characteristics of mechanical flanges:Characteristics:Disassembly: Mechanical flanges are typically composed of two flange faces (flat plate-like parts) and several bolts and nuts. This allows the flange to be easily disassembled and reinstalled, facilitating maintenance and equipment replacement.Sealing: Mechanical flanges can provide a reliable seal, which is crucial for preventing fluid or gas leaks. Sealing is especially important in applications involving high pressure or hazardous substances.Multiple standards: Mechanical flanges come in various standards, including ANSI (American National Standards Institute), DIN (Deutsches Institut für Normung - German Industrial Standards), JIS (Japanese Industrial Standards), and others. Different standards specify the dimensions, number, and location of bolt holes for the flanges.In summary, mechanical flanges are a widely used connection method in engineering and machinery fields, known for their ease of disassembly and reliable sealing. They provide a convenient connection solution for various applications.Therefore, when customers choose YIH KUAN angle head, they need to consider not only their specific usage needs but also how the angle head will connect to their milling machine spindle head. Does it match in size? We will request customers to provide the spindle drawing to assist in checking the dimensions. Once the flange design is confirmed, customers can make the flange themselves, making it convenient to install the angle head upon receiving it.
08. 04. 2023
more
There are two types of gantry milling machine, CNC computer type and non-NC computer type (traditional manual type). It is a milling machine with a portal frame and a horizontal long bed. Gantry milling machines are suitable for machining flat and inclined surfaces of large workpieces in batch and mass production. CNC gantry milling machines can also process space curved surfaces and some special parts. In recent years, the usage habits and processing conditions of gantry milling machines are different, so gantry milling heads have also successively introduced milling heads in different directions for use in machine tools (vertical/horizontal milling heads), and also widely load angle heads/horizontal milling heads. So that the processing range of the gantry milling machine is wider to meet the more difficult processing requirements.Mention traditional gantry milling head, how to choose the correct one to install on a gantry machine? There are two options:- Machine body, according to the connection plate on the gantry milling machine, confirm which type of milling head the connection hole matches.- Application, according to the user's processing conditions.(Such as: processing material, processing efficiency, cutting amount...etc.) Traditional gantry milling heads can generally be distinguished from the size of the motor, gear speed, processing travel and the connection hole position behind the milling head:-Size of motor: 10HP/12.5HP/15HP/20HP/other-Gear speed: 2 stages/6 stages/9 stages/other- Processing travel: 320mm~700mm/other Besides, it can also as a match basis through the connection holes on the back of the milling head (if the user needs to modify or replace the milling head). In necessary, you need to customize a special gantry milling head to match the special body.(Such as: super large gantry milling machine, gantry milling machine with special processing conditions.)
08. 10. 2022
more
The CNC (Computer Numerical Control)
milling machine is a typical machine tool in the machinery sector. It is a
common kind of CNC that can execute repeated drilling and turning activities
that were previously performed by humans.
Ø Classification of CNC milling machines
The total number on a CNC machine
determines its classification. For horizontal movement, axes are designated x
and y, while for vertical movement, axes are labeled z. You will be able to
call these as milling heads. Milling Head Z, Table Z, Table Y, and Table X are
the four axes of this machine. The number of axes it possesses is often
represented in a variety of ways. Out of these, milling heads are the most
important, as they play a major role than other axes.
There is a five-axis machine, for example.
The additional 5th axis comes in the form of a vertical pivot for the mill
head, which ensures outstanding machining flexibility by allowing the end mill
to follow the table at an angle. It's commonly programmed using a set of
standard instructions known as G-codes, which are used to express particular
CNC jobs in alpha-numeric form.
Ø Important features to note in CNC milling
machines
This machine comes in a variety of sizes,
depending on the purpose and area of use, and the material that need to be cut.
Aside from that, the capacity of the motor
has an impact on the speed with which the materials are sliced. Plastic or wood
are often the simplest materials to cut, but steel requires a more powerful
milling machine and more time. You should focus on the specifics before you buy
a milling machine. Then you will never regret about the machine that you
purchase to get work done.
The stiffness of milling may be used to
assess its performance. For instance, the stiffer a mill is the more accurately
it drills or cuts. In comparison to manual mills, CNC mills often feature
superior and harder engines for increased stiffness.
Ø What are the benefits that you can get out
of a milling machine
In comparison to manual operation, we can
increase the speed of cut using a CNC milling machine. When the rigor of the
findings rose, it also lowered rejection. As a result, in the long term, it'll
save a lot of money and time since there will be less waste.
Another advantage of using a cut via CNC
milling machine with such a computerized numerical control machine is the
precision. It is critical in a manufacturing line that all pieces be made
identically. Nothing, however, is perfect. Because a mill may cut with precise
accuracy as near as.0001 of an inch, the operator of a CNC milling machine is
at fault.
Many milling machines also feature beds
that can move at various angles for easier cutting activities, variable angled
cuts, and more complex drilling operations. It is one of the advantages of a
CNC mill over a manual mill. By spraying and blasting hot metal and even
tooling using specially designed coolant, it is possible to retain the quality
raw material using controlled cooling systems.
Final words
Now you have a good understanding of the
different features that milling machines are capable of offering. As you go
ahead and buy a milling machine, you need to focus on these features. Then you
can determine what the best feature that you should be spending your money on
is. Upon the discovery of that perfect milling machine, you can simply stick to
it and get your work done.
07. 12. 2022
more
If you're searching for a CNC Milling Head, the chances are that you
will need a lot of help deciding which one is best for your needs. When you are
on a mission to buy the best CNC milling machine, not just any device will
do.
You have a lot of things to consider and lots of things to think
about. If you don't do ample research ahead of time, you may make a purchase
that is not worthwhile. Don't let yourself make an impulsive buying decision.
You may already know the basics about CNC Milling, but you are still
looking for a specific guide or comparison chart that breaks down all the specs
and whatnot into a more straightforward, digestible form. If this is the case,
you have come to the right place!
Top 9 Tips for Buying Best CNC
Milling Head
The CNC milling head is the essential part of a
CNC mill. It is the heart of a CNC milling machine, which can make the machines
work or not work. Therefore, it is indispensable to choose a good one.
1.Choose the Right Spindle
The spindle is an essential part of the CNC milling head, which
determines the performance and accuracy of your CNC milling machine. Choosing
the wrong spindle will affect your workpiece's accuracy and quality and your
machine's performance and life span.
Therefore, choosing a high-quality spindle with high rigidity, high
precision, and long service life for your CNC milling machine is extremely
important.
2.Make Sure Your Machine Is Plug-and-Play
Another thing to consider when buying a CNC milling head is whether
it's plug-and-play or not. If it isn't, then this means that there will be some
setup required for everything to work correctly together before you can use it.
When this happens, there might be issues with alignment and
calibration (among other things), which could cause problems down the road if
they aren't fixed right away.
3.Choose the Right Tooling
The second step is to choose the proper tooling for your
application. The most common type of tooling is called "tool
holders," which are mounted directly to the spindle and allow you to
change out different bits.
Other options include collets (which grip round objects like drill
bits), end mills (which cut on one side only), or slot drills (which can cut
slots as well as round holes). Slot drills are beneficial if your part requires
multiple holes that align perfectly with one another.
4.Fix Your Requirements
Before searching for the best CNC milling head, you need to know
what you want from it. The first thing to consider is your budget. You should never
buy a product that is beyond your budget.
You also need to consider what kind of work you will be doing with
this machine tool. Any CNC milling head will do if you are a hobbyist who just
wants to make small projects or have fun.
However, if you are an experienced engineer who needs to make
complex parts for big projects, you should buy a high-end product with
additional features.
5.Find Out About the Manufacturer
The next thing you need to do before buying any product is to find
out about its manufacturer to know whether they produce high-quality products
or not.
You should look at their history and determine how many satisfied
customers they have served in the past year or two.
Suppose they have been producing high-quality products for many
years. In that case, this means that they take customer satisfaction seriously
and will provide good service and after-sales service if required by their
customers in the future.
6.Consider Your Budget
Budget is another crucial factor that needs to be considered before
buying any product. You don't need to accept the most expensive product, but
you must purchase something within your budget range.
If the cost of a product is too high, then there are chances that it
might not satisfy all your requirements. If a product falls under your budget
range and has all the features you want in a CNC machine, then this could be
one of the best options for you!
7.Make Sure That the Spindle Fits Your Machine
Perfectly
Before buying any CNC milling head, make sure that the spindle size
fits your machine perfectly. The most common mistake is to choose the wrong
spindle, which will cause damage.
If you have a giant machine, then make sure that you get one that
can handle the more extensive tooling and heavier cutting materials. On the
other hand, if you have a smaller machine, get one that can take smaller tools
and lighter materials.
8.Pay Attention to the Tool Length
Make sure that you pay attention to the tool length when choosing a
CNC milling head to fit your workpiece correctly without causing any damage
while working on it.
You may also need to pay attention to what kind of tooling works
best with whatever material you might be using to get maximum efficiency out of
your new CNC milling head purchase!
9.Look For the Brand
Choosing the right brand can be tricky as many brands claim to offer
high-quality CNC milling heads, but in reality, they don't.
The best way to choose a good brand is by looking at the reviews and
ratings of other customers who have already purchased their products.
Summing Up!
CNC Milling Machine is one of the most devoted machines in the
engineering environment. It can help you perform best on your project within a
short period.
If you are looking for the top 9 tips for buying the best CNC milling heads, read this article because
we have provided you with some excellent ways to make the perfect purchase
without hassles.
The best way to ensure that the product you buy will
suit your needs is to ask as many questions as possible about it. If the shop
selling it does not have good answers, you are well within your rights to
choose another provider.
06. 20. 2022
more
Getting 5-Axis milling machining services
CNC machining solutions are quite
significant, and you may select from a variety of them based on the project and
demands that you have for your items. A manufacturing business may provide you
with 5-axis services, for example. The machining type in question contains
three linear axes and two rotary axes along with an angle head, which might be
in the form of a rotary table or rotary axes just on crank shaft and headstock.
5-axis milling is a sophisticated solution, particularly for complex components
that demand great accuracy. The precision is substantially greater since all
characteristics are done in one setup.
◆What are the benefits of 5-Axis milling
machine services
The 5-axis technique makes it relatively
easy to create complicated forms in a single step, significantly decreasing
machining time, mistakes, and tool costs for the work at hand. As a
consequence, you'll get quicker, more accurate, and more inexpensive outcomes
for your production job.
Because the head may be lowered and the
cutter directed to the surface, this form of machining allows for the use of
smaller cutting tools. As a consequence, a greater cutting speed is reached, as
well as a significant reduction in tool vibration, all of which contribute to
attaining the best outcomes, regardless of the work at hand.
CNC machining is capable of handling
exceedingly complicated pieces made from solids that would normally need casting.
High-temperature alloys such as tool stainless steel, brass, titanium, Alloy,
tungsten, copper, sterling silver, carbon steel, and bronze may all be milled
with the five axis milling. It can also handle polycarbonate, acetal, PP, ABS,
and nylon, among other materials.
When it concerns to drilling holes,
machining saves time. When drilling a sequence of holes with compound angles,
it takes a long time, but with the machine, it's simple to automatically
position the head along the appropriate axis for each hole. As a result, hole
drilling has been simplified and may be accomplished more quickly utilizing
5-axis machining or machining.
◆Things to consider before you go ahead with
5-Axis CNC machine services
When looking for machining services, look
for a company that has been in business for a long time. Keep in mind that
machining service expertise may have a significant impact on the quality of
work and turnaround time. For the finest experience, choose a dependable and
trustworthy manufacturer.
The factory's five-axis CNC milling
equipment are also extremely crucial to consider. The greater the machine's
quality, the better the consistency with which your product outcomes are
delivered. The equipment should be in good working order so that you can get the
results you want in a short amount of time.
Affordability of the service should also be
examined. The costs should correspond to the final product quality. Keep in
mind that the service price is determined on the raw materials utilized. Before
deciding on the finest you can afford, consider what materials the manufacturer
can handle and your demands.
◆Starting your own business to offer CNC
machine services
Since there is a high demand for 5-Axis CNC
machining, you may think about starting your own business around it as well.
This is where you should think about getting the best quality milling machine
available out there. Then you can offer an impressive service to your customers
and get them to buy what you offer. Make sure that you pay special attention to
specific features such as the angle head, as they can contribute a lot towards
the overall functionality that you can get out of the machine.
05. 23. 2022
more
What is a milling head? How to maintain a milling head?Milling machine head aka milling head is an important part of milling machines. The milling head is a combination of different small parts, like driving motor, spindle, and other controlling mechanisms of the milling machine. It holds and rotates the cutting tool of the milling machine on specific or even custom-built centers of machining. It has multiple movement options that can allow machining for four to five axes with ease.Milling head type accessories are either indexing or continuous in regards to their types. These can also offer two to five axes to perform even complex milling operations effectively. However, a continuous milling head can offer an uninterrupted machining experience because the head axis keeps changing.However, on the other hand, the index-type milling heads usually position the milling cutter on a certain axis firstly. Then, it will start the milling operation. These can also handle the machining of plastic, wood, stone, steel, and aluminum.◆Important maintenance tips for milling head1. LubricationOne way to keep tools for milling head services in good condition is by making sure that they are adequately lubricated. In order for milling head to work properly, they must have the proper lubrication that allows all parts to move smoothly. Precision and amount is key when maintaining milling head!2. CleaningAnother important tip for keeping a piece of machinery usable is making sure it’s properly cleaned after use. Many machine parts are often exposed to dirt and other contamination, so it’s crucial to keep your milling head clean to prevent any problems. If you’re having any issues with operating your milling head, dirt could be the cause! In addition, the repair services are needed if you find that some part of your machine needs repair or replacement.3. Daily InspectionsBy doing daily inspections, you can prevent a problem from happening. This is especially important if you’re using your milling head on a daily basis. If something is wrong before you start using your milling head without thoroughly inspecting it first, you may be in for a world of trouble. Thus an inspection can catch the issue before it’s too late.Types of milling machine requires milling head◆ Column Milling MachineThis is the most common milling machine, which has 5 basic components that are the work table, saddle, head, knee, and over arm. Considered as the simplest machine type, its cutting device is vertically suspended to allow drilling of metals. This is typically used when creating car parts because it is small and handy.◆ Turret Milling MachineThe turret is also known as the Bridgeport-type and can be repositioned anytime you want making this machine very functional. Its versatility makes it more practical since a variety of products can be made in addition to car parts.◆ Horizontal type Milling MachineThis machine runs parallel to the ground. The table from which the object to be worked on is placed moves sideways while the cutting device goes up and down.◆ Bed type Milling MachineThe worktable cannot be raised ad lowered, but can be moved longitudinally and laterally along the guide rail of the bed base, and the milling head or column can be moved vertically.◆ Plano Milling MachineThis machine type is basically the same as the bed mill. However, the plano type includes cutters and heads that allow for a wider range of milling actions.◆ Tracer controlled Milling MachineThis type of machine has the ability to reproduce parts based on a master model. Most of the industrial sectors, especially the automotive industry, choose this type of machine because it makes production and specialization of machine parts easier. With the vast classifications of milling machines, you need to choose the one you need according to how you intend to use it. However if you find it's difficult to decide, do not hesitate to seek the help of a specialist who can help you select the one that will give you maximum benefits.How to find the right milling head for your milling machineFinding qualified milling head supplier is a unique process but it’s one of the most important factors. It’s important to check their reference and have a factory tour. It’s easy to get frustrated when you hit dead end, but in most cases, it just requires a little more patience and perseverance to find the perfect supplier for your new machine. To learn more about milling head, contact YIH KUAN today!
05. 10. 2022
more
Many manufacturing organizations have
struggled with the thought of purchasing new machinery or attempting to make
the best selection for their business. If you wonder whether to buy a new CNC
milling machine or a used one, you are at the right place. We will share some
useful facts to clear out all the doubts you have in mind.
l Cost
The cost is the most obvious consideration
when deciding between new and secondhand. The cost of a used automobile vs. a
new car is the first thing that comes to mind. Many decision-makers, on the
other hand, do not consider anything other than the initial cost. A new mill,
for example, may cost $90,000, but a lightly used mill with equal design and
specs would cost just $70,000.
It may seem to be a simple option but
examine the contrasts. To begin, a new mill will typically come with a one-year
guarantee and a two-year warranty on the control. Most secondhand machines are
available with no guarantee, and a warranty on a machine this cheap might be
worth up to $3000. You will need to make sure that all major components of the
machine, including milling heads are in proper working condition at the time of
buying a one. Then you can save money in the long run.
l Installation and delivery
Installation and training are two other
hidden costs of old machinery. All installation methods are included and
delivered by manufacturer qualified experts and engineers with most new machines.
In addition, most new machines come with rigorous product training to guarantee
correct usage, maintenance, and any activities the equipment is capable of.
Depending on the quality of training and the size of the machine, these costs
might reach $4000.
l There’s nothing to inspect in new machines
A consumer should also have the used
equipment examined when they arrive. This is something that the factory experts
would conduct during the new machine's installation. On a fresh machine,
however, nothing is supposed to go wrong. I've seen used equipment in a variety
of situations. Some of my clients have purchased secondhand equipment that have
been installed as if they were brand new. On the other side, I've seen
equipment that required maintenance for thousands of dollars.
Shipping damage is among the worst things
that can happen to a new or secondhand computer. Many electronics and delicate
components are packed inside machines. A lengthy bumpy truck travel through a
variety of conditions may have a significant impact on a machining center. The
only consolation is that a new computer warranty would cover all of these
issues. In most cases, freight insurance will not cover these potential machine
damages.
l Age of the milling machine
Finally, you should think about the age of
the milling machine while making your selection. Do not ignore technological
advancements over time, even though they're not immediately apparent. Some
brands made significant advancements in its basic encoders, which make a significant
impact in contouring and 3D work. Many energy-saving techniques are put into
new machines that were not considered by older equipment.
Final words
If acquired wisely, old machines offer a
lot of advantages. There are many fantastic firms out there, for example, that
sell secondhand equipment after a full evaluation and, if required, repairs.
Some even include a guarantee for a little cost, which you should consider
purchasing.
Smaller start-up enterprises with some
mechanical know-how may also benefit from used machinery since they carry a
lesser financial risk. Though it is a good idea to leave the repair of milling
heads and other parts to factory-trained professionals, certain simple
modifications and fixes may be done at home for a fraction of the price. This
perk may make a major impact in the beginning for small businesses.
04. 14. 2022
more
Milling machines come in many different types with a variety of functions based on certain standard specifications. Some of the most commonly used machines are the following: column, turret, C-frame, horizontal, bed type, planer-style, and tracer controlled. Milling machines facilitate in removing metal pieces through a rotating cutter. The rotation of the cutter takes place at high speed, which helps it cut through metal efficiently. Furthermore, these cutters have cutting edges that play a vital role in cutting materials. Manufacturers often name the different machines according to the kind of control, types of milling head, number of axis present, orientation of the spindle, size of the tool, its purpose, and source of power. While there are several varieties of milling machines available today, they essentially serve the same functions but use different terminologies. Below is the common list of seven types of milling machines. ♦Column Milling MachineThis is the most common milling machine, which has 5 basic components that are the work table, saddle, head, knee, and over arm. Considered as the simplest machine type, its cutting device is vertically suspended to allow drilling of metals. This is typically used when creating car parts because it is small and handy. ♦Turret Milling MachineThe turret is also known as the Bridgeport-type and can be repositioned anytime you want making this machine very functional. Its versatility makes it more practical since a variety of products can be made in addition to car parts. ♦C-frame Milling MachineBecause it is sturdier than a turret, this type is popular in industrial settings. It comes with a hydraulic motor, which makes it very powerful. ♦Horizontal type Milling MachineThis machine runs parallel to the ground. The table from which the object to be worked on is placed moves sideways while the cutting device goes up and down. ♦Bed type Milling MachineThe worktable cannot be raised ad lowered, but can be moved longitudinally and laterally along the guide rail of the bed base, and the milling head or column can be moved vertically. ♦Planer-style Milling MachineThis machine type is basically the same as the bed mill. However, the planner-style includes cutters and heads that allow for a wider range of milling actions. ♦Tracer controlled Milling MachineThis type of machine has the ability to reproduce parts based on a master model. Most of the industrial sectors, especially the automotive industry, choose this type of machine because it makes production and specialization of machine parts easier. With the vast classifications of milling machines, you need to choose the one you need according to how you intend to use it. However if you find it's difficult to decide, do not hesitate to seek the help of a specialist who can help you select the one that will give you maximum benefits. Now you know the main types of milling machines that you will find in almost every industrial sector for cutting materials and shaping them. One of the most important components of milling machine is milling head. If you are looking for a reliable milling head manufacturer for all your mechanical needs, YIH KUAN can definitely help.
04. 01. 2022
Contact Information
- www.yihkuan.com/en-US/
- No.172, Gongye 9th Rd., Dali Dist., Taichung City 412037, Taiwan
- +886-886-4
- +886-886-4